Технология производства керамогранита
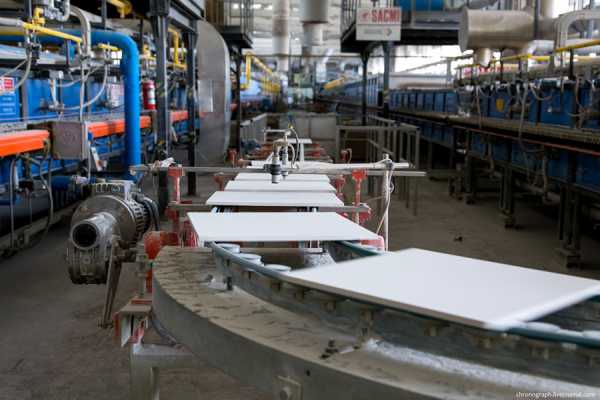
Керамогранит — исключительный по техническим качествам материал, поэтому необходимо, чтобы используемое для его производства сырьё было абсолютно чистым и обладало по возможности совершенной геохимической структурой. Итак, качество сырья является непреложным условием производства хороших изделий.
Процесс изготовления керамогранита начинается со складирования сырья, которое бывает трёх видов: глинистые, неглинистые и инертные материалы. Глинистое сырьё составляют каолиновые глины и каолины, придающие сырьевой основе связывающие свойства и пластичность, что впоследствии, после прессования, позволяет плитке сохранять свою форму. Неглинистые материалы — полевые шпаты — уменьшают пористость обожженных изделий, облегчая процесс спекания и придавая материалу прочность, компактность и стойкость.
Инертные материалы — это кварцевые пески; они образуют «остов» плитки. К сырьевым материалам относятся также пигменты, которые являются оксидами или смесями оксидов металла, почти все они изначально натурального происхождения, переработанные затем особым образом, используются для получения цвета, требуемого производством. После выгрузки и складирования сырья в специальные отсеки, в которых поддерживается постоянная температура, начинается технологический процесс, на первом этапе которого производится помол и окрашивание сырья, которое впоследствии составит основную сырьевую смесь. Сырьё загружается в приёмные бункера, откуда ленточные конвейеры подают его к соответствующим установкам.
Для начала сырьевые материалы, строго дозированные на весовых конвейерах, перемешиваются по заданной рецептуре, в результате чего получается основная сырьевая смесь. Эта смесь подвергается последующей обработке, призванной обеспечить абсолютную однородность массы по размеру и по влажности частиц материалов.
Итак, первый шаг — это достижение гранулометрической однородности. А достигается она в результате мокрого (т.е. в присутствие воды) помола материалов в мельницах, имеющих вид огромных стальных цилиндров, непрерывное вращение которых обеспечивается мощными электродвигателями. Внутри каждой мельницы имеются несколько сообщающихся камер, каждая из которых содержит определённое количество мелющих тел. Последние в результате вращения цилиндров падают одно на другое, измельчая частицы сырьевой смеси.
В качестве мелющих тел используются натуральные материалы (галька) или шары различных размеров из натуральных компонентов, переработанных специальным образом (например, из спечённого глинозёма). Результат — водная суспензия, частицы которой обладают достаточно мелкой и однородной величиной.
Внутри мельница состоит из нескольких сообщающихся камер, разделённых прорезиненными сетками. В каждой камере содержатся мелющие тела, уменьшающиеся по мере перемещения из одной камеры в другую. Смесь перемещается из одной камеры мельницы в другую, только когда зернистость материалов достигает нужных размеров. Получаемая масса — водная суспензия, частицы которой обладают достаточно мелкой и однородной величиной, чтобы можно было перейти к следующей стадии обработки. Эта суспензия называется шликером.
Полученный шликер поступает в огромные подземные бассейны, где, во избежание отстаивания (т.е. оседания составных частей), непрерывно перемешивается с помощью пропеллерной мешалки. Затем сырьевая смесь окрашивается, и получаются те тона, которые впоследствии составят смесь пресспоршка. Окрашивание осуществляется путём добавления в шликер приготовленных ранее красителей, система дозирования которых полностью компьютеризована.
Теперь шликер должен быть обезвожен до нужной степени. Данная операция производится в атомизаторе (башенном распылительном сушиле). Содержащийся в бассейнах шликер при помощи насосов подаётся в атомизатор. Это огромный стальной цилиндр, оснащённый газовой горелкой, которая доводит внутреннюю температуру до 550 градусов. Проходя под высоким давлением через форсунки, шликер распыляется внутрь сушила, где попадает под поток горячего воздуха. Вода быстро испаряется через верхнюю часть атомизатора, а высушенная смесь, пресспорошок, высыпается на транспортёр через его нижнюю часть, который доставляет его в бункера хранения. Цель атомизации — высушить шликер до получения материала, степень влажности которого идеальна для его прессованию.
Процент влажности полученного пресспорошка составляет около 6 %. Это идеальный показатель, обеспечивающий правильное выполнение прессования, в процессе которого плитки обретают форму. Пресспорошки являются главным ингредиентом смесей, которые будут подвергнуты прессованию. Перед прессованием порошки поступают в бункера хранения, где охлаждаются до температуры окружающей среды и становятся однородными по остаточной влажности.
Далее различные цвета извлекаются из бункеров и перемешиваются посредством автоматизированного оборудования в соответствии с формулой или рецептом. Количество цветовых сочетаний бесчисленно. На этом этапе возможно обогащение порошков другими материалами, в виде гранул, порошков или чешуек, придающими готовым изделиям особые эстетические и технические свойства. Полученные таким образом составы являются конечным результатом процесса обработки сырьевых материалов.
Этап прессования преследует три цели: формование плитки – придание пресспорошку установленной формы; трамбование пресспорошка — процедура, позволяющая сырой и ещё необожженной плитке выдерживать последующие нагрузки; уплотнение – предельное сокращение пористости плитки.
Этап формовки начинается с подачи пресспорошка к прессам. Прессование включает четыре стадии:
- Сначала форма наполняется пресспорошком, который подаётся из расходных бункеров, расположенных над прессами.
- Затем форма закрывается, и выполняется первичное прессование под небольшим давлением. В этом случае содержащийся в плитке воздух сжимается и удаляется при лёгком открывании формы.
- После этого имеет место вторичное прессование, которое и обусловливает создание сырой плитки.
- И в последнюю очередь плитка извлекается из формы, а одновременно идёт новая загрузка пресспорошка для последующего прессования.
Производство керамогранита, технологии, циклы, этапы
Керамический гранит – популярный строительный материал, изготавливаемый из специальной мелкодисперсной смеси. Производство керамогранита осуществляется в несколько последовательных этапов. Простыми словами можно описать, как выполняется весь процесс и какими качествами наделяется готовый керамогранит.
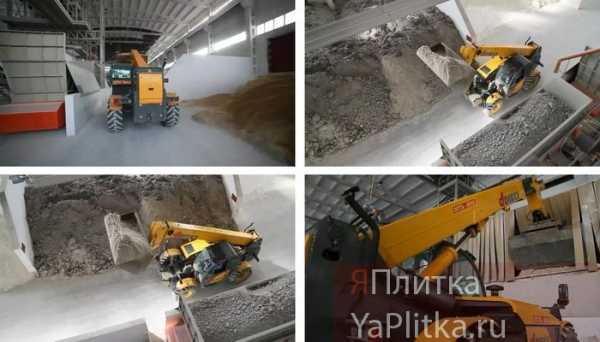
Характеристики керамогранита
Смесь для керамогранита изготавливается из двух различных сортов глины, в состав которой входят минеральные кварцсодержащие материалы и природные пигменты-красители (например, окись железа, придающая кобальтовый оттенок материалу). Состав настоящего керамогранита во многом схож с природным камнем гранитом. Однако этот материал обладает одним преимуществом – в его составе нет никаких радиоактивных включений (как в натуральном граните), подбор компонентов раствора для производства керамического гранита тщательно контролируется. Смесь приготавливают посредством тщательного перемешивания и последующего прессования под большим давлением (около 500 кг/кв.см.) После того, как спрессованный камень немного просохнет, осуществляется обработка керамогранита методом обжига при высокой температуре (около 1200-1300 градусов).
В целом же производство керамогранита выполняется по тому же принципу, что и в природных условиях. Разница лишь в том, что процесс создания камня полностью контролируется мастером, что позволяет получить высококачественный декоративный материал. Керамогранит свойства свои приобретает благодаря правильному выполнению мастером всей технологии производства. Камень становится прочным, устойчивым к воздействию неблагоприятных факторов, имеет красивый внешний вид.
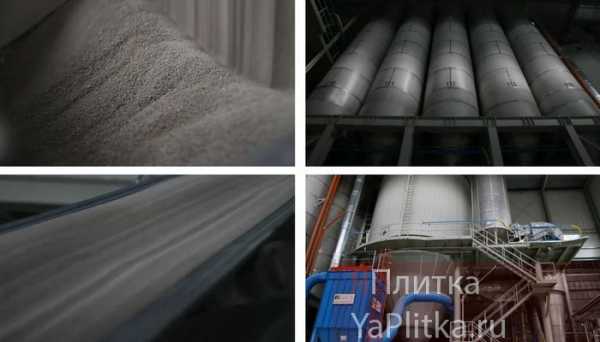
Отличительной особенностью керамогранитного камня является то, что узор у него на срезе и поверхности одинаков. Кроме глины (обычно применяют белую массу) в составе раствора для керамического гранита имеются минеральные компоненты, полевые шпаты и кварц. Покраска керамогранита выполняется на первом этапе изготовления, в процессе приготовления сырьевого раствора. В густую массу добавляют минеральный пигмент и хорошо размешивают. Такой подход позволяет равномерно распределить красящий состав по всей толще керамического гранитного камня. Кроме того, добавление пигмента в раствор исключает выцветание оттенка камня в процессе эксплуатации, под воздействием ультрафиолетовых солнечных лучей.
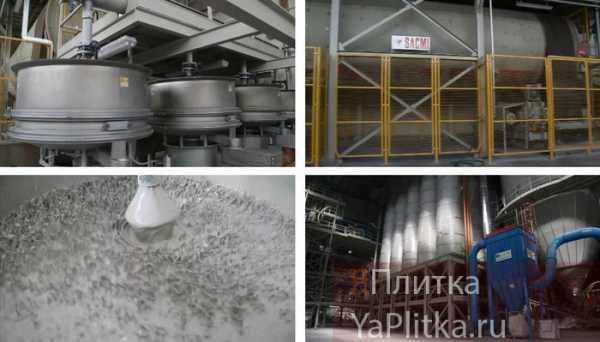
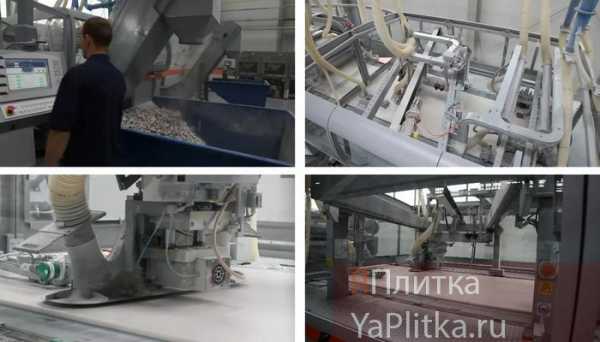
Одним из важных достоинств керамогранита является высокая износоустойчивость. Используемая технология изготовления керамогранита обеспечивает материалу хорошие показатели морозоустойчивости, стойкости к ультрафиолетовому излучению, большим сопротивлением неблагоприятным климатическим и механическим воздействиям.
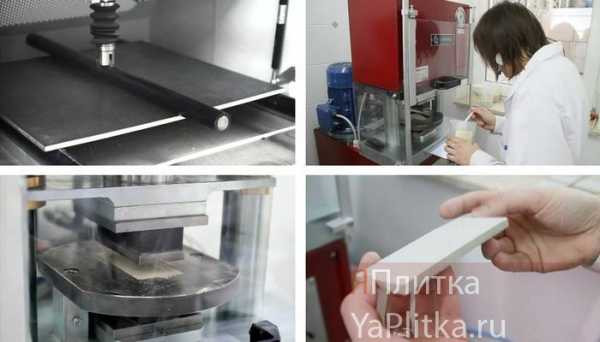
Керамогранит, состав которого обеспечивает плотную структуру материалу, характеризуется низким уровнем водопоглощения. Он не подвержен воздействию щелочных материалов и кислот, может выдерживать огромные механические и ударные нагрузки, давление ветра и внутреннее напряжение, вызываемое резкими перепадами температур. Более того, технология керамогранита настолько качественна и хороша, что материал может успешно противостоять открытому огню (характеризуется отличными огнеупорными свойствами).
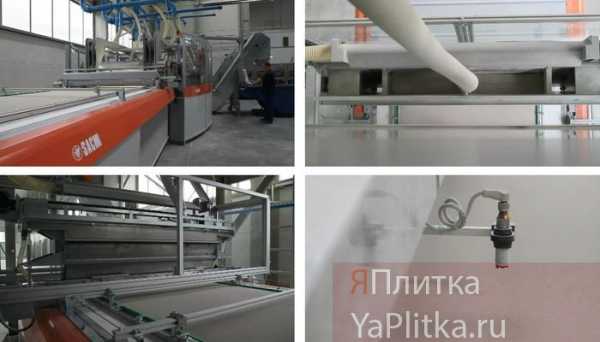
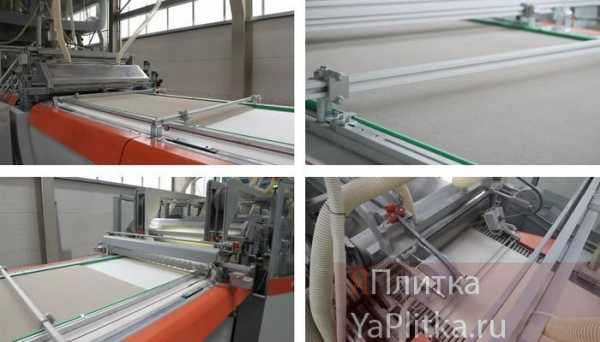
Внешний вид керамогранитного камня может быть разным, в зависимости от способа обработки. Матовый материал после обжига не обрабатывается вообще, сохраняя свой первоначальный природный облик. Рельефный керамогранит имеет на своей поверхности ярко выраженный узор. Полировка плитки керамогранит обеспечивает получение красивого материала с идеально гладкой, ровной глянцевой поверхностью. Полирование керамогранита осуществляется посредством срезания верхнего матового слоя после обжига материала. Изготовление керамогранита в производственных условиях позволяет получить и полуполированный камень. Его создают посредством частичного срезания верхнего слоя. В итоге поверхность керамогранита получается комбинированной, в ней есть и матовые, и глянцевые участки. Нормы расхода керамогранита (количество материала на 1 кв.м. площади помещения) определяются производителем в соответствии с техническими характеристиками готового изделия. В данном случае учитывается размер одного элемента и ширина швов между плитками.
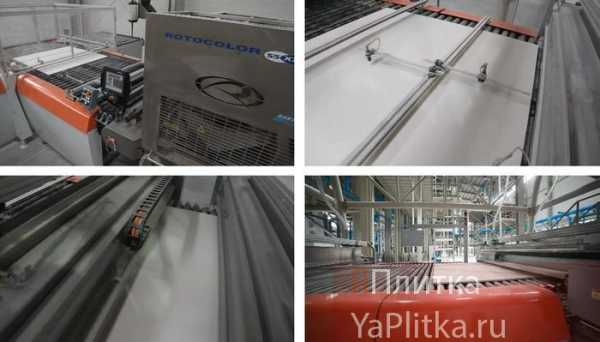
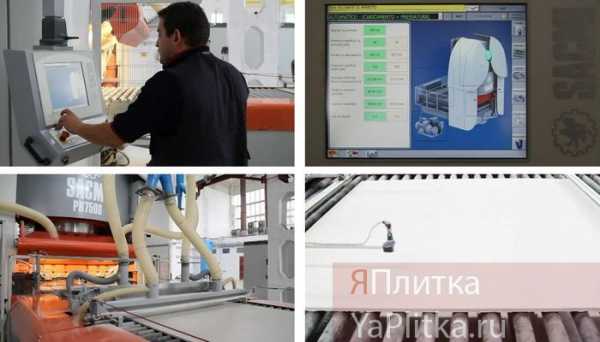
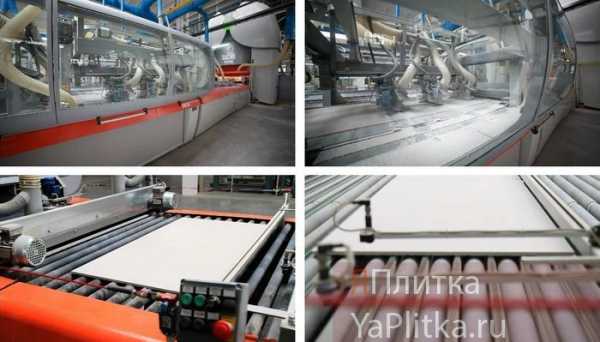
Завод по производству керамогранита поставляет на строительный рынок глазурованный и не глазурованный декоративный камень. В первом случае внешний вид плитки более привлекателен, но её рекомендуется применять только для покрытия пола, на поверхность которого создаются небольшие нагрузки.
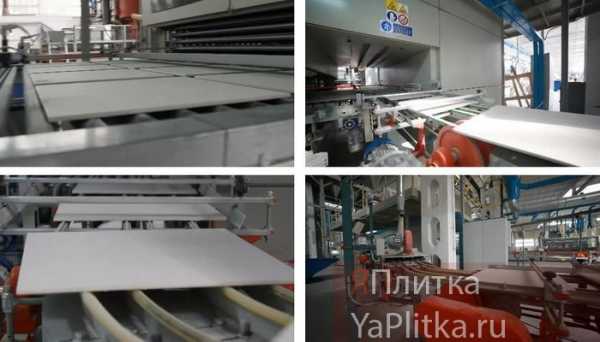
Страны, в которых сейчас действуют заводы по производству керамогранита:
- Россия
- Италия
- Испания
- Турция
- Китай
- США
Производство керамогранита (видео пример с итальянского завода) постоянно совершенствуется.
Изготовители этого строительного материала регулярно изменяют дизайн керамогранита, создавая всё новые и новые текстуры, оттенки и узоры.
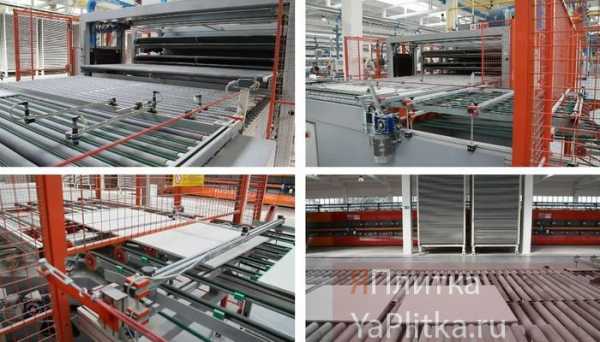
Это важно! Правильно комбинируя между собой различные виды гранита керамического (камень должен иметь одинаковый размер), можно красиво украсить интерьер комнаты и создать уникальный дизайн стен или пола в помещении.
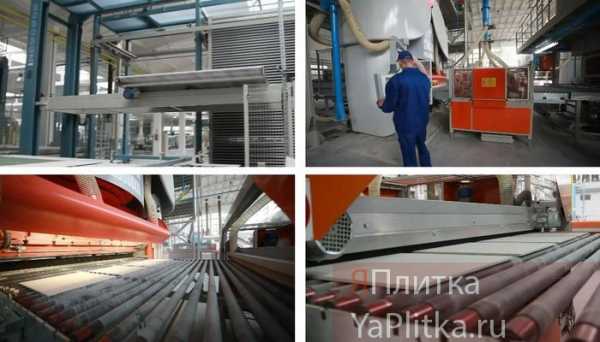
Технология изготовления керамогранита
Строительный материал керамогранит, технология производства которого имеет свои особенности, создаётся исключительно из природного натурального сырья (глины). Материал подвергается однократному обжигу, поэтому сырьё обязательно должно обладать огнеупорными характеристиками и содержать минимальное количество красящих элементов (титана или оксидов железа). Заводы производители керамогранита применяют в качестве сырья такие материалы, как полевой шпат, огнеупорные глины, кварцевый песок и каолин. Перед использованием каждый из этих материалов проходит тщательную проверку (входной контроль). Современное оборудование для производства керамогранита полностью компьютеризировано, и это позволяет мастерам проводить анализы и получать результаты высокой точности. После того, как сырьё проходит полноценный технологический контроль, его допускают (или не допускают) к дальнейшему производству.
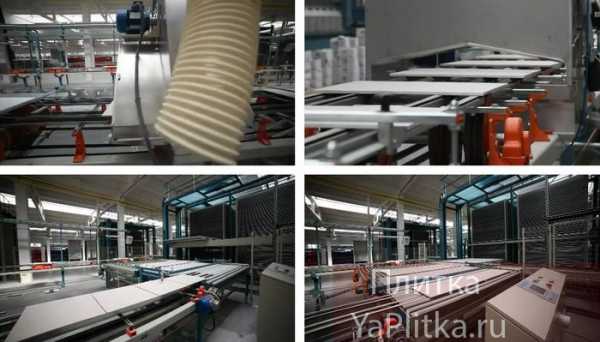
Теперь расскажем, как делают керамогранит. Вся процедура осуществляется последовательно, в несколько этапов. Рассмотрим каждый из них в подробностях.
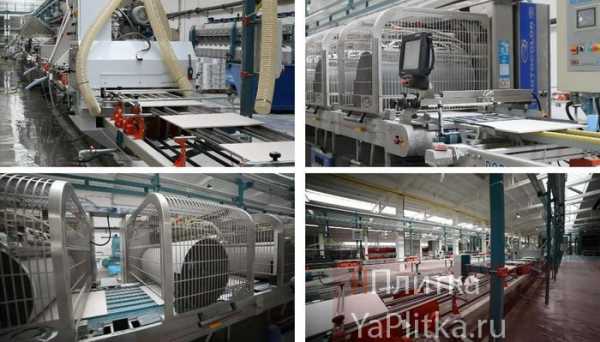
Выбор сырья и приготовление раствора
Производство керамогранита начинается с выбора сырья и приготовления на его основе раствора. Здесь нужно быть очень внимательным, ведь от качества исходного материала будет во многом зависеть качество готового изделия. Керамогранит, глина для которого подбирается мягкая и пластичная, окрашивается специальным пигментом (с основой в виде металлических окисей — хрома, кобальта, железа или марганца). Для того, чтобы готовый керамический черепок получился более прочным, в раствор во время приготовления добавляют полевой шпат и кварцевый песок. Для производства керамогранита ещё необходима глина малой пластичности, насыщенная каолином.
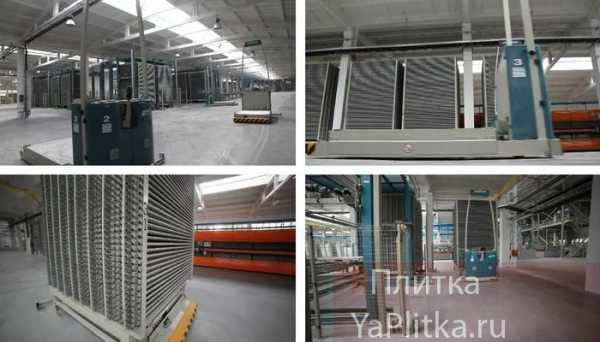
Подготовленное сырьё необходимо хорошо измельчить, используя специальное оборудование для керамогранита (мельница) и метод мокрого дробления. Такой подход обеспечивает раствору однородность, благодаря чему обожжённый черепок получается качественным и прочным. Когда состав хорошо измельчён, его подают в смесительную камеру мельницы, где происходит приготовление порошкообразной смеси. Далее из раствора выпаривают воду, поместив его в камеру с горячим воздухом (с температурой около 600 градусов). Получаемый состав полностью подготовлен к прессованию.
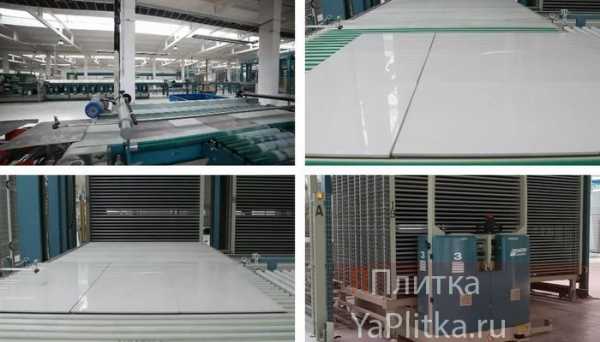
Прессование керамогранита
Качественное изготовление керамогранита возможно только при правильном подходе к прессовке подготовленной глиняной смеси. Гранулированный раствор с содержанием влаги не более 7% прессуется под давлением не менее 400 кг/см2. Такая процедура позволяет получить прочное изделие нужной формы, размера и фактуры.
Сушка сформированного изделия
Сушка следующий важный этап, применяемый при производстве керамогранита. Дело в том, что в процессе прессовки в материале остаётся определённый процент влаги (необходимой для формовки изделия). Главной задачей на этапе сушки является полное обезвоживание наполовину готового продукта. Завод керамогранита использует для качественной сушки материала специальные тепловые камеры с высокой температурой и горячим воздухом. Заготовки керамогранита укладываются туда, а весь процесс просушивания тщательно контролируется ответственными специалистами.
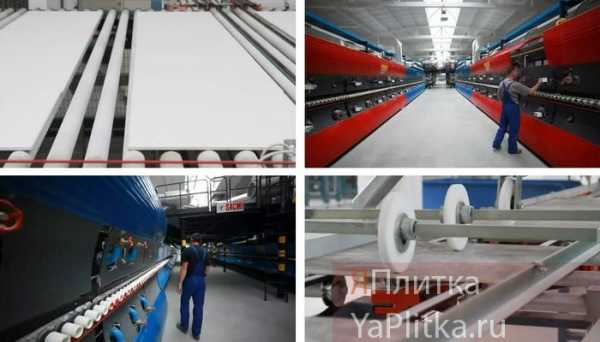
Обжиг
Устройство керамогранита на этапе обжига предполагает воздействие на подготовленный материал высокой температуры. В ходе температурной обработки керамогранит приобретает необходимую прочность. Глиняное сырьё, находясь под воздействием большой температуры, спекается, становясь монолитным. После остывания изделие становится невероятно прочным, с минимальным количеством пор и высокой стойкостью.
Совет. При обжиге керамогранита необходимо следить за уровнем температуры, поскольку от неё зависит оттенок готового строительного материала. Контроль особенно необходим в том случае, если камень покрывается глазурью. Чрезмерно высокая температура приведёт к пережогу поверхности, а если температурный режим будет меньше нормы, то изделие получится недожжённым, а значит, менее прочным.
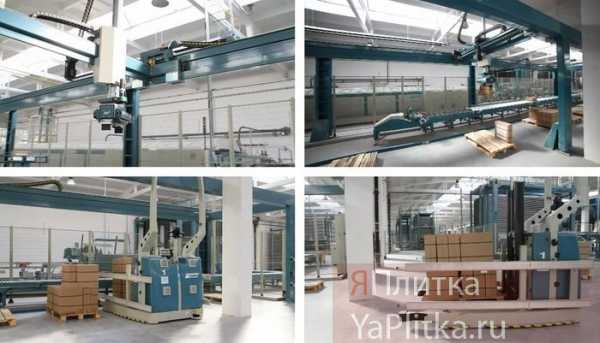
Контроль качества продукции
За качеством готового изделия необходимо следить во время его выхода с автоматической линии. Каждый плиточный элемент проверяется при помощи компьютеризированного оборудования на предмет соответствия европейским стандартам.
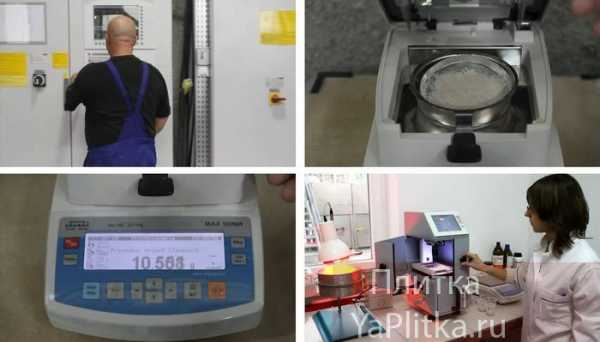
Некачественная плитка сразу убирается из партии и впоследствии перерабатывается специальным механизмом. А вот качественный материал сортируется по цвету, сорту и калибру.
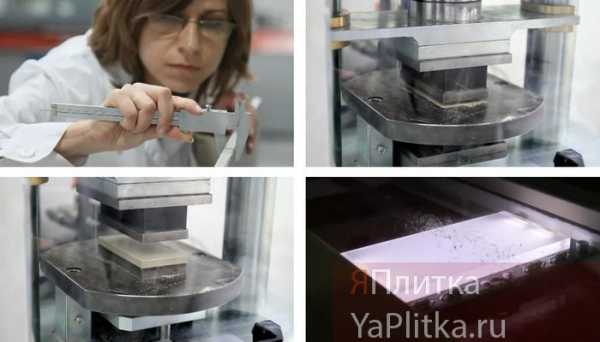
Изготовленный и отсортированный керамогранит (упаковка которого выполняется в автоматическом режиме в специальную тару), отправляется на оптовые склады. Реализаторам остаётся только сформировать ценник на керамогранит, доставка материала конечному потребителю осуществляется сразу же после поступления заказа на склад.
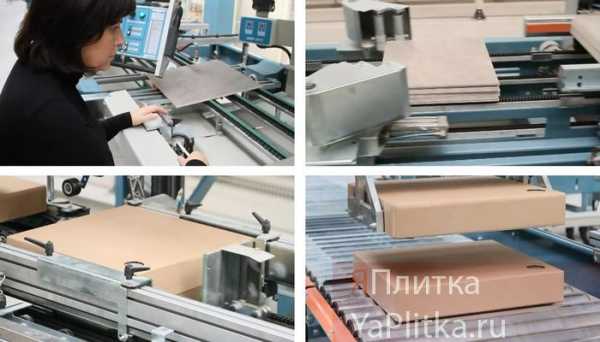
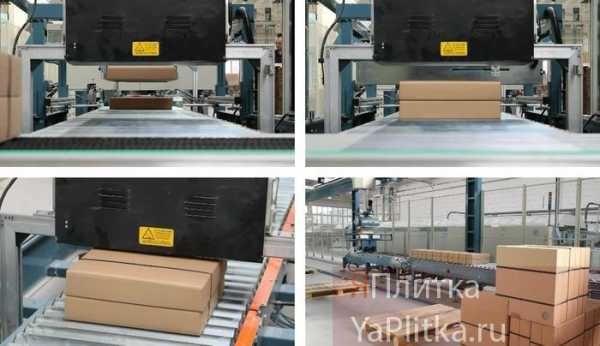
yaplitka.ru
Технология производства керамического гранита
О керамическом граните
Керамический гранит (GRES porcellanato (ит.)) — одна из современных технологий в керамическом производстве. Керамический гранит относится к области высоких технологий и представляет собой новое поколение керамики, имитирующей природный камень. При этом керамический гранит устойчив к воздействию слабо агрессивных сред и по некоторым эксплуатационным и потребительским характеристикам превосходит натуральный камень.
Разработку технологии производства керамического гранита можно назвать крупнейшим достижением керамической отрасли. Создан материал, который по своим техническим и эстетическим характеристикам не только не уступает, но и превосходит натуральный камень. Процессы, протекающие в природе в течение миллионов лет, в промышленных условиях занимают несколько часов.
Целью разработки технологии производства керамогранита было создание материала, пригодного для облицовки полов в помещениях промышленных предприятий. Материал должен был быть способным выдерживать высокое давление, быть устойчивым к абразивным повреждениям, термическому воздействию и едким химическим средам.
Эксплуатационные характеристики материала, изготовленного по изобретенной итальянскими инженерами технологии, оказались столь впечатляющими, что керамогранит получил в настоящее время широчайшее распространение для облицовки самых разных поверхностей в жилых и нежилых помещениях.
Керамический гранит производится на основе высококачественных огнеупорных глин с добавлением кварцевого песка, полевого шпата, каолина, красящих пигментов и др. Смесь прессуют под более высоким давлением (400–500 кг/см?), чем облицовочную плитку, и обжигают при температуре 1200 °C. В результате получается чрезвычайно прочный материал с развитой кристаллической структурой и насыщенной стекловидной фазой, с практически нулевым водопоглощением.
Керамогранит — морозостойкий материал. Для того, чтобы плитка считалась морозостойкой, она должна быть внутри абсолютно плотной и не содержать никаких трещин и пор. В поры обычной плитки очень легко набирается влага, которая при минусовой температуре замерзает и, по законам физики, рвет плитку изнутри. Следовательно, чем ниже водопоглощение плитки, тем выше её морозостойкость. Так вот, водопоглощение керамического гранита меньше одного процента (чаще всего десятая или сотая процента.) Именно поэтому он чрезвычайно устойчив к низким температурам. То есть мороз до — 50°С он выдержит стойко и мужественно, без ущерба для своего внешнего вида, (впрочем, так же, как и жару до +50°С), что и позволяет использовать его для наружной отделки даже на Севере!
Данный продукт обладает высокими физическими свойствами, устойчив к истиранию. Поэтому керамический гранит идеально подходит для использования в местах с интенсивной пешеходной нагрузкой, для отделки жилых помещений, для внешней облицовки зданий (для навесных вентилируемых фасадов).
Подробнее о производстве керамического гранита
Керамический гранит производится по технологии однократного обжига из высококачественных природных сырьевых материалов огнеупорных украинских глин, каолина, полевого шпата, кварцевого песка и испанских объемных красителей. Основное требование, предъявляемое к сырью — минимальное содержание красящих оксидов, оксидов железа и титана. Все сырьевые материалы подвергаются входному контролю.
Лаборатории оснащены современным компьютеризированным оборудованием, позволяющим оперативно производить сложные анализы с высокой точностью, только после заключительного положения отдела технического контроля о качестве сырья, оно поступает в производство.
Весь процесс производства керамогранита от дозировки сырьевых материалов до упаковки готовой продукции, осуществляется на высокопроизводительном итальянском оборудовании SACMI, управляемым и контролируемым компьютерными системами:
- Дозированные, согласно рецепту, сырьевые материалы подвергаются мокрому помолу, который осуществляется в шаровых мельницах непрерывного, либо периодического действия, цель данного процесса повышение реакционной способности массы при обжиге и качественное перемешивание сырьевых материалов.
- Базовый шликер перекачивают в емкости запаса.
- Превращение шликера в пресс-порошок осуществляется в башенной распылительной сушилке «атомизаторе». Шликер, распыленный под высоким давлением в башне атомизатора до капельного состояния, при контакте с теплоносителем отдает влагу, и превращается в сыпучий порошок заданного гранулометрического состояния.
- Для производства керамического гранита СОЛЬ и ПЕРЕЦ кроме базового неокрашенного шликера, готовятся и цветные.
- Процесс дозировки контролируется компьютерной системой.
- Высушенные базовые и цветные порошки проходят лабораторный контроль и поступают в емкости запаса.
- Получение заданного базового и цветных пресс-порошков, осуществляется непосредственно перед их подачей в бункер пресса.
- Прессование плитки осуществляется в гидравлических прессах.
- Механическую прочность достаточную для транспортировки, плитка приобретает, благодаря высокому удельному прессованию, порядка 400 кг. на. кв.см. Роль связки выполняет влага, содержащая в исходном пресс порошке.
- Отпрессованная плитка направляется в вертикальную сушилку, в процессе интенсивной сушки, влажность плитки снижается с 5,5% до 0,5%.
- Путем дискового или безвоздушного напыления на лицевую поверхность плитки, наносится тонкий слой износоустойчивой глазури «КРИСТАЛИНЫ» которая, оплавившись при обжиге, придаст плитке значительное преимущество перед натуральным камнем, защитит от образования пятен в процессе эксплуатации.
- Обжиг керамического гранита осуществляется в роликовой печи в течение 50 минут, максимальная температура обжига — 1210°C градусов. Транспортировка плитки через печи, осуществляется посредством керамических роликов, компьютеризированная система с высокой точностью выдерживает заданный режим термообработки.
- Вся обожженная плитка, подвергается тесту на наличие трещин и поступает на сортировку, причем человек принимает участие, только в классификации качества лицевой поверхности, по всем геометрическим показателям, сортировку плитки, осуществляет электроника.
- Система сортировки позволяет разделять плитку по калибрам таким образом, что линейные размеры плитки, уложенные на один поддон, не отличаются более чем на 1 мм.
- Отсортированная плитка упаковывается, принтером наносится информация, позволяющая идентифицировать продукцию, после ящики укладываются на поддон. Весь процесс сортировки и упаковки осуществляется в автоматическом режиме.
- Выпущенная продукция подвергается контролю на соответствие требований нормативной документации, и только после этого поступает на склад для отгрузки потребителям.
Соответствие европейской технологии производства керамогранита и европейским стандартам качества является отличительно чертой продукции «ЗКС», в частности, керамогранита марки «Уральский гранит».
www.uralgres.com
Технология производства керамогранита
Керамический гранит своими свойствами обязан не только высококачественному экологически чистому сырью, но и продуманной технологии производства.
Рассмотрим:
1.разная технология для разного керамогранита
2.прессование
3.сушка
4.декорирование: цифровая печать
5.декорирование: Нанесение декоративных эффектов
6.обработка поверхности7.ректификация и калибровка
Разная технология для разного керамогранита
В зависимости от того, какой именно керамогранит необходимо получить (матовый или полированный, окрашенный на всю толщину или тоненьким слоем, глазурованный или неглазурованный), порядок операций в технологической цепочке может изменяться.
Прессование
Далее пресс-порошок по транспортеру поступает в расходный бункер гидравлического пресса. Прессование – технологический передел производства, суть которого заключается в придании формы, достаточной прочности и максимальной плотности полуфабрикату для проведения следующих технологических процессов сушки и обжига. Прессование и обжиг – наиболее важные этапы производства керамогранита.
Прессование происходит в несколько этапов.
1. Форма гидравлического пресса наполняется пресс-порошками.
2. Затем форма закрывается, и выполняется первичное прессование под небольшим давлением (около 80 кг/см2). На этом этапе из заготовки удаляется воздух, разрушаются крупные поры и мостики из частиц порошка. Суммарная площадь соприкосновения частиц пресс-порошка увеличивается.
3. После этого происходит уплотнение заготовки при давлении не менее 500 кг/см2. На данном этапе происходит деформация зерен пресс-порошка. При этом влага выделяется в пространство между зернами порошка и склеивает их. Частицы разрушаются, увеличивая общую площадь соприкосновения.
Цели этапа:
• Формование – придание сыпучему пресс-порошку строго заданной геометрической формы.
• Прессование – процедура, позволяющая сырой и ещё необожженной плитке выдерживать последующие нагрузки.
• Уплотнение – предельное сокращение пористости плитки.
• Создание рельефа – предание плите определенной структуры, имитирующей натуральную поверхность
Сушка
На данном этапе заготовки плиток еще не готовы к обжигу, так как содержат слишком большое количество остаточной влаги. Поэтому плитки отправляются в вертикальную сушилку до достижения целевой влажности не более 1%. Общее время сушки составляет 2-2,5 часа. Без этого заготовки пришлось бы обжигать с остаточной влажностью 4-6%, что привело бы к большому проценту брака.
Внутри вертикальной сушилки поддерживаются три независимые зоны с различным температурным режимом, объемом и направлением подаваемого воздуха.
Первая зона – восходящее движение плиток. Рабочая температура воздуха 130-200°С. На данном этапе удаляется большая часть остаточной влажности заготовок.
Вторая зона – нисходящее движение плиток. Рабочая температура воздуха 80-180°С.
Зона стабилизации. Цель данной зоны – приведение температуры плитки на выходе из сушилки в соответствие с требуемым значением.
После сушки заготовки отправляются в накопитель для ожидания дальнейших операций.
Цели этапа:
• Удаление из заготовок остаточной влаги.
• Максимальная механическая прочность до обжига.
• Выравнивание температуры заготовок.
Декорирование: цифровая печать
Первые опытные образцы струйных керамических принтеров были представлены на выставке Cevisama в Испании в 2000 году. С тех пор технология цифровой печати завоевала рынок. И небезосновательно. Вот основные преимущества технологии перед аналогами в виде ротоколора и шелкографии.
- Нет контакта печатающего устройства с поверхностью плитки.
- Абсолютная стабильность изображения (отсутствие износа трафаретов).
- Значительное сокращение расхода пигментов.
- Не требуется изготовление печатных форм и трафаретов
- Минимальное время на смену печатающегося изображения и цвета.
- Сокращение времени на разработку и реализацию идей в готовом продукте.
- Воспроизведение природных и других фактур в фотореалистичном качестве.
6-канальный цвет позволяет достоверно передать текстуру природных материалов, а специальные чернила, создающие эффекты рельефа и отражений позволяют улучшить эти материалы, придавая им дополнительные эстетические свойства.
Декорирование: Нанесение декоративных эффектов
Декорирование плиты происходит непосредственно перед обжигом в печи посредством цифровой печати DOD. На производстве используется современное высокотехнологичное итальянское оборудование — Projecta Evolve. Для создания спец. эффектов на керамогранитную основу наносятся специальные чернила. Производство таких чернил осуществляется ведущим европейским предприятием Torrecid в Испании. На данный момент на производстве TM KERRANOVA и TM GRASARO используется четыре канала для печати спец эффектов для получения максимально достоверной имитации текстуры камня или дерева. Существует несколько разновидностей материалов для печати:
✓ Carving чернила – используются для подчеркивания натуральности рельефа и текстуры плиты, придает прожилкам свечение и глубину.
✓ Glossy чернила – усиливают глубину и блеск прожилок в камне, подчеркивают структуру прожилок дерева.
Обработка поверхности
После обжига некоторые плитки отправляются на линию полирования. В зависимости от режима работы оборудования, используемых инструментов (фикерты, щетки и другие) и типа нанесенной глазури возможно добиться разнообразных эффектов поверхности: от идеально плоской зеркальной полировки до шелковистого на ощупь лощения.
• При полировании верхний слой плиты (∽ 0,6 мм) срезается алмазными роликами и затем шлифуется и полируется магнезитовыми абразивами, позволяя добиться идеально плоской зеркальной поверхности.
• У лаппатированного керамогранита шлифуется фикертами только очень тонкий верхний слой глазури (∽ 0,2 мм), защищающей рисунок, что придает блеск и глубину изображению.
• Для лощения (сатинирования) используются специальные щетки, которые позволяют придать поверхности состаренный вид.
Ректификация и калибровка
Важнейшая характеристика для качественной укладки керамогранита точность размеров. В процессе производства, соответствие заданным размерам достигается двумя способами: ректификацией и калибровкой.
Калибровка — процесс распределения керамогранитных плит после обжига на группы в зависимости от их реальных размеров. Калибр и фактический размер могут отличаться в рамках допусков, установленных в технических условиях. В любом случае калибры и их размеры указываются заводом — изготовителем на упаковке. Калиброванная плитка на выходе из туннельной печи остается с естественными, не обработанными краями.
Ректификация (от лат. rectus – «прямой» и facio – «делаю») – процесс дополнительной обработки боковых торцов керамогранитной плитки алмазными дисками, в результате чего всей партии придается единый строго определенный размер. Это не только навсегда снимает проблему подбора нужного калибра, но и позволяет укладывать плитки с минимальным швом, добиваясь эффекта монолитной поверхности.
grasaro.ru
Керамогранитная плитка, технические свойства, плюсы и минусы, состав, производство
Что такое керамогранит и где его используют
Керамогранит — это искусственный, особо прочный искусственный камень, как правило плоской, правильной формы, используемый для внутренней и внешней отделки помещений и зданий.
Керамогранит еще называют керогранитом, керамическим гранитом.
Родиной керамогранита является Италия, где его называют керамический фарфоровый камень. Название керамогранит, материал получил на постсоветском пространстве, в связи с его высокой прочностью в сравнении с другими плиточными материалами. Этот материал изобрели сравнительно недавно, и стали использовать в Европейских странах в начале 20-го века. В русскоязычном мире керамогранит стали производить в конце 90-х годов 20-го века. В настоящее время качество производства не уступает Европейскому.

фасад из керамогранитной плитки
Керамогранитную плитку используют для облицовки фасадов, в любых климатических условиях, внутренней отделки помещений с повышенной влажностью , такие как ванные комнаты , душевые, бани, санузлы. Хорошо подходит керамогранит в качестве напольного покрытия как внутри помещения, так и на улицах, общественных местах с большой проходимостью. Керамогранит –один из немногих универсальных отделочных материалов, который эффективно используется как для внутренних работ, так и внешних отделках зданий и прилегающей территории.
Состав керамогранитной плитки и ее производство
Название материала – керамогранит, не соответствует его составу, поскольку совсем не содержит добавки гранита. Как отмечалось выше, такое название керамогранит получил благодаря своим эксплуатационным характеристикам, в качестве сравнения с прочностью гранитного камня.
В основу процесса производства керамогранитной плитки заложены принцы образования природного камня в естественных условиях.
Для производства керамогранитной плитки используют каолиновую глину, кварцевый песок, полевой шпагат, минеральные красители из металлов, для придания эстетического внешнего вида материалу и воду.
Каолиновая глина (ее еще называю бела глина) –это глинистое сырье из группы силикатов алюминия. Она образуется в природе, в результате выветривания горных пород, которые содержат полевые шпаты. Характеризуется высокой огнеупорностью и высокой связующей способностью.
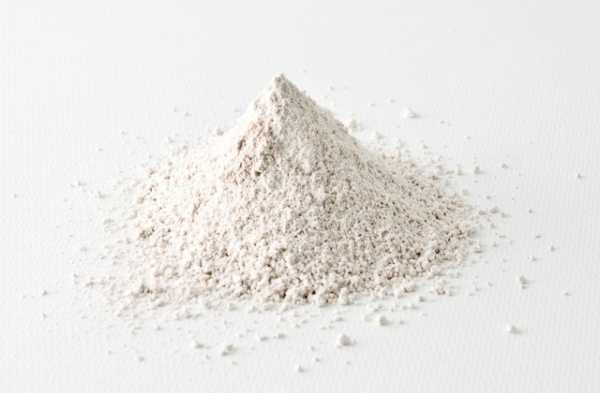
каолиновая глина
Полевой шпат – это породообразующий природный материал магматических пород таких как граниты, сиениты и другие породы, характеризующиеся высокой спайностью, прочностью и твердостью.
Кварцевый песок – это мелкозернистый природный материал, образованный в результате разрушения кварцсодержащих горных пород, с повышенным содержанием кварца. Имеет разнообразную цветовую гамму, в зависимости от природных примесей. Может быть как белого цвета, так и желтым, красным серым. Кварц является породообразующим составляющим пород магматического происхождения
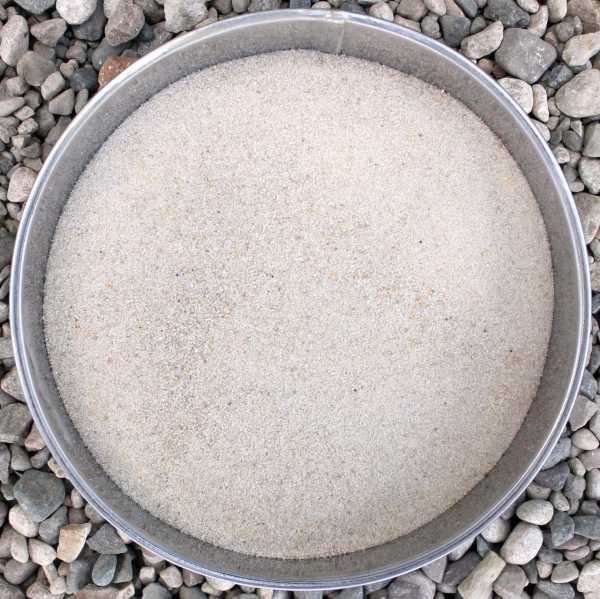
кварцевый песок
Готовую, полусухую, смесь формуют, в соответствии проектом, отправляют под гидравлический пресс с давлением 400- 500 кг/см². После чего, спрессованная, в нужных объемах, смесь отправляется на обжиг в печь , где подвергается температуре 1300 °C. Обжиг осуществляется по нарастанию температуры, от малой к большей. В отличие от производства кирпича, где формованную смесь помещают в уже раскаленную печь. Под воздействием такой температуры керамогранит приобретает свои максимальные качества прочности и износоустойчивости.
При производстве керамогранита, в отличие от других видов искусственных камней, сложность заключается в том, что для получение нужных свойств материала, необходимо точно соблюдать пропорции составляющих в смеси и технологии. Вот почему керамогранитную плитку не изготовить в кустарных условиях. Тут необходимо специальное оборудование.
Таким образом, если разобраться в составе материала, то можно сделать вывод, что материалы, которые используются для создания керамогранитной плитки, являются природными материалами из которых гранит образуется в природе, при естественном протекании химических процессов и воздействия окружающей среды.
Технические характеристики керамогранитной плитки
- Уровень поглощения влаги низкий коэффициент. Такое свойство керамогранит имеет за счет своей низкой пористости. Коэффициент влагопоглощения 0,05%. Этот показатель даже ниже чем у природного камня: https://www.svoyidoma.ru/naturalnyj-kamen-preimushhestva-i-nedostatki-prirodnogo-kamnya/
- Наивысшая степень устойчивости к стиранию, износу и каким-либо серьезным повреждениям, царапинам. Материал сохраняет цвет на протяжении всего существования. Устойчив к постоянному воздействию солнечных лучей. Твердость керамогранита сравнима с алмазной прочностью.
- Механическая прочность очень высокая. Выдерживает нагрузку 200 кг на см², при чем, если использовать керамогранитную плитку в качестве напольного покрытия, то такая прочность одинакова, будь это плитка толщиной 8,6 мм или 30 мм. Средняя прочность на изгиб 55 Мпа. Но этот показатель варьируется от толщины материала.
- Вес керамогранитной плитки варьируется от ее толщины. Материал из самых тонких плит, стандартных размеров, в расчете на один квадратный метр будет примерно 25 кг , а самой толстой 30 мм – до 70 кг/м².
- Высокий уровень жаропрочности, не горит и не поддерживает горение. Устойчива к резким температурным перепадам в пределах 100 °C, без изменения своих свойств и структуры. В целом, керамогранитная плитка выдерживает температуру от – 500ᵒС до +10000°С.
- В состав керамогранита входят только природные составляющие.
- В отличие от гранита не имеет природного радиационного фона, так как не содержит гранит в своем составе.
- Стандартный размер керамогранитной плитки от 5х5 см до 120х360 см. Толщина от 3 мм до 30 мм. Подробнее о видах керамогранитной плитки.
Плюсы керамогранитной плитки
- Высокая прочность. Как отмечалось выше, керамогранит особо прочный материал. Его прочность пи соблюдении правильной методики укладки сохраняется до 200 кг/см2, при любой толщине плитки. Во время повседневной эксплуатации его достаточно трудно повредить. Плитка способна выдерживать значительные статические и ударные нагрузки. При ударном воздействии не раскалывается. Как правило какие–либо повреждения Керамогранитный материал получает при транспортировке, разгрузке, погрузке, на стадии ремонтных работ.
- Не выгорает под воздействием солнечных лучей. Не меняет свою текстуру и рисунок со временем.
- Устойчива к любым загрязнениям. За счет своей плотной структуры не впитывает в себя сторонние жидкости, жиры. Потому все загрязнения легко удаляются обычной мокрой тряпкой или каким-либо моющим средством.
- Материал из керамогранита особо водостойкий, так как керамогранит не пористый. Влагу не впитывает Благодаря таким свойствам керамогранитная плитка, является хорошим материалом для отделки плов помещений с повышенной влажностью, таких как ванный комнаты, санузлы и кухни.
керамогранитная плитка походит для мокрых точек в доме 5. Устойчивость к воздействию кислот. Не меняет окраски, поверхности, своих свойств, при попадании на поверхность любых химических веществ и кислот. После удаления таких жидкостей, на поверхности керамогранитной плитки не будет неэстетичных следов.
6. Устойчивость к истиранию. Рисунок и текстура керамогранитной плитки не стирается совсем, поскольку окрашивающий пигмент пронизывает плитку на всю толщину. При таком выполнении рисунка, даже повреждения на плите в виде ямок незначительных выбоин будут не заметны.
7.Экологичность. Материал состоит из природных компонентов, без химических примесей. 8. Пожаробезопасна, поскольку не горит и не поддерживает горение под воздействием открытого огня. Кроме того, под воздействием высоких температур не выделяет никаких вредных испарений. 9.Разнообразие. Керамогранитная плитка имеет в своем ассортименте большое множество цветового разнообразия, множество рисунков и форм. Также существует множество разновидностей плитки в зависимости от типа поверхности материала и обработки. Это керамогранит с матовой поверхностью, полированной, глазурованной поверхностью, технический и структурный керамогранит, сатинированный. При этом, разновидности керамогранитной плитки постоянно обновляются. Производитель постоянно усовершенствует керамогранитный материал и обновляет его разнообразие. С помощью керамогранитной плитки, Вы можете реализовать все свои дизайнерские фантазии.
Минусы керамогранитной плитки
- Низкая теплопроводность керамогранитной плитки способствует созданию эффекта холодной поверхности. Что бы устранить этот недостаток, в частном домовладении зачастую монтируют систему теплых полов под керамогранитную поверхность. Это требует дополнительных затрат на обустройство полового покрытия. К тому же, в многоквартирных домах теплый пол монтировать запрещается. Этот метод применим только для частного дома.
- Хрупкость. За счет высокой прочности керамогранитная плитка не пластична. Не пластичность приводит к повреждениям при кладке и транспортировке. Потому при работе с керамогранитом это следует учитывать.
- Тяжелая. Квадратный метр керамогранитной плитки толщиной 8 мм весит примерно 18-19 кг. Вес зависит от толщины плиты. Такой вес, при монтаже керамогранитной плитки на стены, создает определенные трудности, так как создает определенное давление на нижние ряды плит и кладка может «съехать». При стеновой кладки двух-трех рядов плитки, следует ждать до набора прочности клеевой смеси на которую укладываются плитки. Высокий вес керамогранитной плитки отражается на скорости стеновой кладки.
- Скользкая поверхность. При попадании влаги на поверхность керамогранитной плитки, она становится очень скользкой. Такая поверхность становится травмаопасной. Потому, для мощения дорожек во дворах, любых поверхностей вне крыши, места в доме где может быть попадание влаги( кухня, ванная комната, прихожая) целесообразно использовать глянцевые, матовые лаппатированные поверхности керамогранитной плитки.
- Как и при кладки любой плитки, пол из керамогранитной плитки будет иметь швы. Этот недостаток спорный. Поскольку одни домовладельцы в наличии швов видят эстетику и они не прилагают никаких дополнительных для уборки мусора между швами. Хотя швы между керамогранитными плитками совсем небольшие и между ими просто не может скапливается крупный мусор. Другие же домовладельцы в наличии швов не видят никакой эстетики и считают что между швами плитки скапливается трудно убираемый мусор.
- Дополнительные трудности в монтаже. Работать с керамогранитной плиткой должны опытные мастера. За счет большой прочности материала, керамогранитные плитки трудно резать. Необходим специальный станок для резки, расходный материал на который обходится не дешево. Опытные мастера нужны еще и для квалифицированной резки, так как при выполнении спилов можно сколоть материал, сделать не ровные срезы, тем самым испортить материал. Кроме того, работы по кладке и демонтажу керамогранита обходятся дороже кладки обычной керамогранитной плитки.
- Цена керамогранитной плитки дороже стоимости керамической плитки.
Керамогранитная плитка используется как для внутренней отделки помещений таки для наружной. Керамогранит пригоден для отделки полов, уличных площадок с большой проходимостью так и фасадов и стен внутри строения. Это идеальное половое покрытие для полов с высокой нагрузкой.
Материал однозначно заслуживает внимания и использования в каждом строительном проекте, будь это частное жилое строительство или благоустройство общественных мест.
www.svoyidoma.ru
Как делают керамогранит — репортаж с фабрики
Керамогранит появился в Италии в конце семидесятых годов двадцатого века и тех пор получил широчайшее распространение по всему миру. В России он называется керамогранит, керамический гранит, или иногда грес. В Италии и остальном мире gres или gres porcelanato,что приблизительно переводится с итальянского как фарфоровая керамика.
Еще совсем недавно керамогранит в нашей стране был всем в диковинку, сегодня им никого уже не удивишь, но далеко не все знают что же в реальности он из себя представляет. Часто даже от продавцов плитки можно услышать что керамогранит прессуется из гранитной крошки, или другие не менее занимательные версии. В этой статье мы расскажем из чего состоит керамогранит и проиллюстрируем фотографиями с фабрик весь процесс его производства, от подготовки сырья до попадания готовой продукции на склад фабрики.
Итак, вопреки распространенным заблуждениям, керамогранит не имеет никакого отношения к граниту и прочим натуральным камням, а производится как и обычная керамическая плитка из глины и по очень похожей технологии, но есть и отличия. Тогда как обычная керамическая плитка производится из красной или белой глины, либо определенных их смесей, в состав керамогранита входят два вида светлых глин, каолиновой и иллитовой, обладающих разными свойствами (в частности иллит более пластичен, а каолинит обладает большей огнеупорностью). Помимо глин в состав керамогранита входят кварцевый песок и полевой шпат.
При взаимодействии всех этих компонентов при высокой температуре и большом давлении происходит процесс остекловывания или витрификации, в ходе которого керамогранит и приобретает свои уникальные свойства. Кстати, подобные процессы происходят и при производстве известного нам всем фарфора, так что можно считать эти два продукта близкими родственниками. Теперь вспомним, что итальянцы называют керамогранит gress porcellanato — фарфоровая керамика.
Для придания керамограниту нужного цвета используются минеральные красящие пигменты, как правило окислы металлов. Керамогранит бывает полной прокраски (другие названия: прокрашенный в массе, tutta massa, неглазированный, full body), в данном случае окрашивается вся смесь из которой прессуется керамогранит и окраска равномерна по всей его толщине.
Второй вид керамогранита — глазурованный, когда сам керамогранит не окрашен (на срезе он сероватого оттенка), а на его поверхность нанесена глазурь нужного цвета. Такой керамогранит называется глазурованным, или смальтированным. Стоимость красителей зависит от цвета и иногда может составлять значительную долю от стоимости готового керамогранита. Попробуйте в магазине поинтересоваться ценами на красный керамогранит полной прокраски, поверьте, результат превзойдет ваши ожидания.
Cырьё, для керамогранита (уже известные нам глина, песок и полевой шпат) хранится в специальных отсеках при определенных параметрах температуры и влажности, и уже готово к превращению в керамический гранит.
Сначала сырье загружается в специальные бункеры, а затем с помощью ленточных конвейеров подаётся на производственную линию. Здесь все компоненты дозируются по определенному рецепту, и попадают в мельницу, представляющую собой огромный металлический цилиндр.
Фотография предоставлена Ассоциацией итальянских производителей керамической плитки Confindustria Ceramica
Перемалывание производится в присутствии воды. Внутри цилиндра-мельницы находится множество мелющих тел: натуральной гальки, либо шаров из определенных материалов, например глинозема или алюбита. Внутри цилиндра несколько камер, в каждой из которых мелющие тела разных размеров. Смесь перемещается от камеры с более крупными мелющими телами к камере с более мелкими, проникая через специальные сетки по мере достижения требуемых размеров. На выходе из мельницы мы получаем суспензию (водный раствор) из мельчайших и одинаковых по величине частиц, называемых шликером (или по итальянски barbottina).
Готовый шликер хранится в специальных бассейнах при постоянном перемешивании, потом в шликер в заданных концентрациях добавляются красящие пигменты, а затем он поступает в атомизатор (башенную распылительную сушилку), где подвергается обезвоживанию. Атомизатор — это вот такой огромный металлический цилиндр внутри которого установлены газовые горелки.
Шликер, распыляясь внутри сушилки, опадает на дно уже в виде порошка, который подается на очередную транспортную ленту.
Влажность порошка после атомизатора составляет 6%, что является оптимальным для последующего прессования. Результатом этого этапа являются пресспорошки, которые имеют соответствующие цвета, хранящиеся вот в этих бункерах.
Впоследствии полученные пресспорошки разных цветов смешиваются в заданных концентрациях для получения нужного оттенка.
Теперь материалы готовы к следующему очень важному этапу — прессованию в ходе которого они наконец-то приобретут свою будущую форму. Прессование происходит при помощи гидравлического пресса, который является одним из самых важных компонентов производства. Именно параметрами пресса определяются максимальные размеры керамогранита производимого фабрикой.
Прессование производится в два этапа Первичное прессование при нагрузке около 80 кг/см2 способствует удалению воздуха. На втором этапе прессования при давлении более 500 кг/см2 происходит формирование плитки. После чего “сырая” плитка помещается в сушильную камеру для полного удаления влаги.
После сушильной камеры влажность смеси в плитке составляет лишь сотые доли процента и плитка уже готова к обжигу. Но до этого (не зря же работали дизайнеры фабрики) плитка как правило проходит еще один этап. Сначала (если необходимо) она попадает в глазуровочную камеру где на нее распыляется глазурь.
Фотография предоставлена Ассоциацией итальянских производителей керамической плитки Confindustria Ceramica
После этого (или вместо этого, в зависимости от дизайна) плитка подвергается окрашиванию или нанесению рисунка, например, с использованием традиционного оборудования Ротаколор. Система состоит из четырех барабанов, каждый из которых наносит на плитку рисунок определенного цвета.
Вот это будет глазурованный керамогранит красного цвета.
Фотография предоставлена Ассоциацией итальянских производителей керамической плитки Confindustria Ceramica
А это, вероятно, керамогранит под камень.
Последние несколько лет получила распространение цифровая струйная печать на керамограните, возможности которой значительно превосходят возможности Ротаколора. Она позволяет наносить на керамогранит любой рисунок с фотографическим разрешением. Главной сложностью здесь пока остается подбор цветов, так как использовать можно только натуральные красители. Так что пока все производители плитки дружно печатают на этих принтерах плитку под дерево и плитку под камень.
После окраски будущие плитки размещаются в специальные хранилища и ждут своей очереди перед этапом, который в корне изменит их свойства, прессованные плитки, которые легко можно раскрошить руками уже совсем скоро превратятся в прочнейший керамогранит.
Обжиг происходит в несколько этапов. Сначала плитки обжигаются при 400 градусах по Цельсию (этап предварительного обжига), потом разогреваются до 900 (предварительный прогрев), затем происходит основной обжиг при температуре 1200-1300 градусов, и наконец постепенное понижение температуры. Во время обжига плитка уменьшается в размерах на 5-10%.
Такие печи работают непрерывно, отключаются только для проведения профилактических работ 1-2 раза в год, остывание и нагрев такой печи занимает по времени около недели. Поэтому все производство рассчитано таким образом, чтобы печь была загружена постоянно. И если, например, выходит из строя пресс, должен оставаться запас готовой для обжига прессованной плитки на все время его простоя.
Далее при необходимости плитка подвергается полировке или реттификации. На фото плитка проходит процесс полировки, на выходе будет плитка с полуполированной поверхностью (по-итальянски lappato), обладающая эффектным неоднородным блеском.
Фотография предоставлена Ассоциацией итальянских
производителей керамической плитки Confindustria Ceramica
Теперь плитка готова. Можно отправлять ее на склад? Пока нет. Осталось еще несколько важных операций. Сначала надо отсеять плитку с дефектами. Это могут быть геометрические искажения плитки, сколы, трещины, пустоты, неравномерность окраски и другие отклонения от заданных параметров. Контроль качества плитки также проходит в автоматическом режиме.
На стенде представлены различные дефекты плитки, у итальянцев вообще с этим очень строго, по российским ГОСТам эта плитка, скорее всего, вполне могла бы попасть к покупателю.
Мы уже знаем,что во время обжига плитка уменьшается в рамерах на 5-10%. Так как глина “живой” материал, то понятно что не существует двух абсолютно одинаковых плиток, и в итоге при номинальном размере плитки, например 500х500 мм из печи выходят плитки и размером 500х500 мм и 495х495 мм и 505х505 мм, попробуйте уложить все это разнообразие в одну и ту же комнату. Чтобы избежать такой ситуации готовая плитка сортируется по калибрам, вариации размеров внутри одного калибра не превышают 1 мм и укладка такой плитки не представляет никакой сложности.
Сортировка по калибрам, как и все уже известные нам этапы производства полностью автоматизирована.
Но на современной фабрике производящей керамогранит есть один этап, где нельзя обойтись без участия человека. Это сортировка плитки по тонам. Тона — это вариации оттенков плитки, которые, аналогично размерам плиток могут различаться на выходе из печи. Кому то может и понравится, когда все плитки на кухне будут разных оттенков, это выглядит натуральнее. Большинство же покупателей плитки хотят однотонный пол, поэтому фабрики вынуждены сортировать плитку по тонам.
И как оказалось, человеческий глаз очень чувствительный и совершенный прибор и никакие компьютерные системы оснащенные самой дорогой оптикой не могут с ним сравниться в способности безошибочно различать оттенки. Поэтому сортировку плитки по тона производит человек, сравнивая плитку с эталонными образцами. Именно этим занята итальянская синьора на фото под присмотром главного технолога фабрики.
Видите разницу?
Теперь осталось всего-то упаковать керамогранит в коробки.
Разложить на палеты так, чтобы на каждой был керамогранит определенного тона и калибра.
И отвезти на склад фабрики, где он будет дожидаться, своего покупателя.
Редакция благодарит группу компаний Ricchetti Group и Ассоциацию итальянских производителей керамической плитки Confindustria Ceramica за содействие в подготовке данной статьи.
Смотрите также статьи:
Производство керамогранита — видео от керамогранитного завода Италон
Монокоттура и бикоттура — плитка одинарного и двойного обжига
Разные тона плитки или почему опасно докупать плитку спустя два года
etoprosto.ru
Технологии производства керамогранита | Гранитея
Керамический гранит производится по технологии однократного обжига из высококачественных природных сырьевых материалов огнеупорных украинских глин, каолина, полевого шпата, кварцевого песка и испанских объемных красителей. Основное требование, предъявляемое к сырью — минимальное содержание красящих оксидов, оксидов железа и титана. Все сырьевые материалы подвергаются входному контролю.
Лаборатории оснащены современным компьютеризированным оборудованием, позволяющим оперативно производить сложные анализы с высокой точностью, только после заключительного положения отдела технического контроля о качестве сырья, оно поступает в производство. Весь процесс производства керамогранита от дозировки сырьевых материалов до упаковки готовой продукции, осуществляется на высокопроизводительном итальянском оборудовании SACMI, управляемым и контролируемым компьютерными системами.
Дозированные, согласно рецепту, сырьевые материалы подвергаются мокрому помолу, который осуществляется в шаровых мельницах непрерывного, либо периодического действия, цель данного процесса повышение реакционной способности массы при обжиге и качественное перемешивание сырьевых материалов. Базовый шликер перекачивают в емкости запаса. Превращение шликера в пресс-порошок осуществляется в башенной распылительной сушилке «атомизаторе». Шликер, распыленный под высоким давлением в башне атомизатора до капельного состояния, при контакте с теплоносителем отдает влагу, и превращается в сыпучий порошок заданного гранулометрического состояния.
Для производства керамического гранита СОЛЬ и ПЕРЕЦ, кроме базового неокрашенного шликера, готовятся и цветные. Процесс дозировки контролируется компьютерной системой. Высушенные базовые и цветные порошки проходят лабораторный контроль и поступают в емкости запаса. Получение заданного базового и цветных пресс-порошков, осуществляется непосредственно перед их подачей в бункер пресса. Прессование плитки осуществляется в гидравлических прессах.Механическую прочность достаточную для транспортировки, плитка приобретает, благодаря высокому удельному прессованию, порядка 400 кг. на. кв.см. Роль связки выполняет влага, содержащая в исходном пресс порошке. Отпрессованная плитка направляется в вертикальную сушилку, в процессе интенсивной сушки, влажность плитки снижается с 5,5% до 0,5%.
Путем дискового или безвоздушного напыления на лицевую поверхность плитки, наносится тонкий слой износоустойчивой глазури «КРИСТАЛИНЫ» которая, оплавившись при обжиге, придаст плитке значительное преимущество перед натуральным камнем, защитит от образования пятен в процессе эксплуатации.
Обжиг керамического гранита осуществляется в роликовой печи в течение 50 минут, максимальная температура обжига — 1210°C градусов. Транспортировка плитки через печи, осуществляется посредством керамических роликов, компьютеризированная система с высокой точностью выдерживает заданный режим термообработки. Вся обожженная плитка, подвергается тесту на наличие трещин и поступает на сортировку, причем человек принимает участие, только в классификации качества лицевойповерхности, по всем геометрическим показателям, сортировку плитки, осуществляет электроника. Система сортировки позволяет разделять плитку по калибрам таким образом, что линейные размеры плитки, уложенные на один поддон, не отличаются более чем на 1 мм.
granitea.ru