особенности подготовки ингредиентов, прессование, обработка поверхности
Замес. При производстве керамогранита каолиновая глина смешивается с полевым шпатом, кварцем и минералами. Для придания плитам керамогранита необходимого цвета в сырьевую массу добавляют минеральные пигменты. Таким образом, цвет распределяется по всей толщине плиты керамогранита, придавая ей однородную структуру. В зависимости от используемых пигментов при производстве керамогранита возможно большое разнообразия цветовой гаммы и рисунков.
Прессование. Процесс пресования плит керамогранита происходит под высоким давлением — до 400-600 кг/см2. При таком давлении внутри сырьевой массы не остается пор и пустот, а частицы исходного материала тщательно спрессовываются.
Обжиг. Закрепляет и усиливает достигнутые при прессовании характеристики полуфабриката. Обжиг плит керамогранита проводится в печи при температуре до 1300 С0. При такой температуре внутри материала происходит перекристаллизация компонентов, и они образуют «стекловатый» монолит.
Обработка поверхности плит керамогранита производится на шлифовальной и полировочной линиях. Полировка поверхности керамогранита производится с помощью специальной пасты, на основе алмазной пыли. При полировке убираются мельчайшие неровности поверхности, и достигается высокий уровень зеркальности — до 80%. Возможна другая степень полирования — до уровня зеркальности 20%. При этом поверхность получается менее ровной на микро уровне. Для того, чтобы поверхность плит была шершавой, керамический гранит не полируют, а шлифуют, покрывают глазурью и закаливают.
По характеру обработки поверхности различаются следующие типы керамического гранита:
— полированный керамогранит — прошедший полную стадию полирования — зеркальность 80%;
— недополированный — прошедший не полную стадию полирования — зеркальность 20%;
— шлифованный (матовый) керамогранит — прошедший только стадию шлифовки более «грубым» абразивным материалом;
— глазурованный керамогранит — неполированный, покрытый специальной глазурью.
Глазурь оставляет керамогранит шероховатым, не скользким и в тоже время защищает его поверхность от масляных пятен и грязи.
Производство керамогранита — оборудование и технология
Керамогранит (керогранит, керамический гранит) — искусственный отделочный материал. Подходит для внутреннего и наружного применения, для облицовки пола и стен.
Изначально керамогранит использовался как техническая плитка, для облицовки производственных помещений и общественных мест, выбор этого материала обусловлен основными свойствами керамогранита — прочность, износостойкость, огне- и влагостойкость, керамогранит выдерживает большие перепады температур.
Родина керамогранита — Италия, где его начали производить в 70-х годах XX века для технических нужд.
Позже, благодаря отличным потребительским качествам, керамогранит завоевал популярность у широких слоев населения и стал применяться повсеместно. Широкое разнообразие видов керамогранита и отличные эстетические свойства позволяют использовать данный материал в различных дизайнерских решениях — от недорогих интерьеров частных домов, до luxury интерьеров.
Производство керамогранита
Производство керамогранита требует множество специализированных установок, больших производственных помещений и складов, высокого качества исходного материала и полное соблюдение технологий производства. Поэтому производство керамогранита относится к «дорогим» производствам, однако, данная особенность нивелируется тем, что производство также является «высокодоходным» и рентабельным.
Принципиальная схема и оборудование для производства керамогранита
Глупо рассказывать вам рецептуру производства, так как, закупая линию, производитель вас обязательно обучит работать на ней. Коротко опишем технологические процессы производства.
Керамогранит производится методом прессования из специальной полусухой смеси. Смесь в свою очередь представляет собой нормализованную и гомогенизированную смесь исходных компонентов — кварцевый песок, беложгущиеся глины или каолины, полевые шпаты и пигменты, вода, часто в смесь добавляют окрашивающие окислы.
Прессование происходит в два этапа. Первый этап, при давлении в 80 кг/см² из смеси удаляются воздушные пузыри, второй этап, при давлении в 600 кг/см² из смеси формируется исходная плитка керамогранита.
Перед вторым этапом на плитку наносится специальный слой, который отвечает за текстурированную имитацию поверхности у керамогранита, например, под мрамор. Качество прессования отвечает в дальнейшем за эксплуатационные свойства керамогранита.
После этого, при помощи оборудования, на керамогранит наносится окраска, рисунок и глазурь (определяется типом готового изделия), а само изделие поступает на сушку, где из него удаляются оставшиеся 4% влажности. Когда изделие полностью обезвожено, его отправляют на обжиг в печь.
Обжиг керамогранита производится при температуре до 1300°C в несколько этапов. Сама печь представляет собой сложное устройство — конвейер с несколькими температурными зонами, длиной более 100 метров, где процесс обжига происходит беспрерывно в несколько этапов, таких как — предварительный обжиг (до 400°C), разогрев (при 900°C), основной обжиг (при 1300°C), постепенное остуживание керамогранита. За процесс обжига керамогранит теряет до 10% размеров.
После обжига плитка поступает на этап контроля и сортировки. Где в автоматическом и ручном режимах проверяются геометрические и физические характеристики плитки, отсеивается брак, плитка, на этом этапе, также калибруется по оттенкам и размерам.
После сортировки — плитка окончательно обрабатывается, на ее поверхность наносят специальные покрытия, плитки шлифуются и полируются. И поступают на упаковку и отгрузку.
Посмотрите видео о различных этапах производства керамогранита
Даже при условии, что в России производят различный керамогранит, это не покрывает всего спроса и керамогранит ввозят в Россию из Европы, Китая, Индии, Турции и других стран. Это обусловлено тем, что спрос на такой материал стабилен, а существующих рынок не способен обеспечить такой объем предложений. Поэтому, организовав собственное производство керамогранита, вы попадаете в благоприятную бизнес-среду и сможете быстро отбить все вложения в бизнес.
Специально для ХОБИЗ.RU
Технология производства Керамогранита
КЕРАМОГРАНИТ (керамический гранит)Керамический гранит также называют: плитка грес, гранитогрес, каменная плитка из искусственного камня. Отличия керамического гранита от керамической плитки обусловлены технологией изготовления этого материала. Отличают керамический гранит от плитки по боковому срезу — на срезе неглазурованного (не покрытого глазурью) керамического гранита структура и цвет материала те же, что и на поверхности.
Производство керамического гранита является высокотехнологичным процессом. Керамический гранит получают из белой специальной глины с добавлением полевых шпатов, кварца и минералов.
Если в дальнейшем не предусмотрено нанесение глазури, изделие окрашивается еще на стадии изготовления: для придания керамограниту необходимого цвета в сырьевую массу вводят минеральные пигменты. Таким образом, цвет распределяется по всей толщине плитки, придавая ей однородную структуру, напоминающую природный гранит. Благодаря такой технологии производства свет и ультрафиолетовые лучи не оказывают влияния на интенсивность цвета. Кроме того, возможно изготовление большого разнообразия цветов и текстур.
В отличие от керамических плиток керамический гранит обладает более высокими показателями износостойкости (относится к самому высокому классу — PEI V), сопротивления механическим и климатическим воздействиям, морозостойкости, устойчивости к ультрафиолетовым излучениям, и т.
Керамический гранит выпускается глазурованным и неглазурованным. Глазурь необходима в случаях когда предусмотрено придание поверхности вида, принципиально недостижимого без глазури. Глазурованная плитка применяется, в основном, для полов, где существует относительно меньшая нагрузка на полы, т.к. глазурь под воздействием песка может стираться. В этом случае ее внешний вид ухудшается, но при этом своей прочности плитка не теряет.
Ведущие производители керамического гранита постоянно совершенствуют технологии производства, что позволяет сегодня выпускать керамический гранит, практически ничем не отличающийся от натурального камня, воссоздающий редкие сорта гранита и мрамора, добиваться огромного разнообразия цветовых оттенков, текстур. Выпускается керамический гранит, имитирующий и другие материалы, например, дерево, венецианскую штукатурку, чистые цвета, и т.д.
Внимание! Оттенки на мониторе и в каталогах могут отличаться от натурального цвета плитки.
Piastrella
ТЕХНОЛОГИЯ ПРОИЗВОДСТВА КЕРАМОГРАНИТА

Керамический гранит — это великолепный строительный материал, обладающий высокими техническими характеристиками и обширной зоной применения (покрытие полов, стен, входных групп и вентфасадов).
Основным сырьем для производства данного продукта являются натуральные экологически чистые материалы: полевой шпат, глина, каолин и кварцевый песок, а для частичного окрашивания применяют специальные природные добавки и красители.
ПРОИЗВОДСТВЕННЫЙ ПРОЦЕСС
I этап: приемка и первичная обработка сырья
Цепочка технологического процесса начинается с качественной приемки, сортировки и складирования производственного сырья.
После определения влажности и химического состава сырья, происходит взвешивание компонентов массы согласно шихтовому составу. Для подкраски массы используют различные добавки, которые вводятся в основу. Взвешенный материал подается на транспортер, по которому он поступает в цех подготовки шликера.
II этап: подготовка шликера
Для производства керамического гранита методом прессования из полусухих порошков принята шликерная технология приготовления массы.
Основная задача этого технологического передела — разрушение природной структуры глин, ее дезагрегирование, удаление вредных примесей из природного сырья, правильное дозирование шихтовых компонентов по заданной рецептуре и придание массе достаточной плотности и однородности путем тонкого измельчения компонентов и их тщательного смешивания.
Тонкий помол всех компонентов производится в шаровых мельницах мокрого помола. В качестве мелющих тел используются уралитовые шары.
Далее готовый шликер через вибросито при помощи мембранного насоса сливается в мешалки медленного хода, где он должен находится не менее 12-ти часов для усреднения.
После выдержки шликер подается по трубам в приемные мешалки цеха распыления.
III этап: распыление
В данном цехе осуществляется обезвоживание шликера. Принцип сушки заключается в следующем: струя керамической суспензии подается поршневым насосом под давлением через сетчатый фильтр и форсунки в сушильную камеру. За счет центробежной силы поток закручивается и вылетает через сопло в виде конусного факела капелек шликера, которые, попадая в нагретое рабочее пространство, быстро отдают влагу и виде шариков оседают в конической части башенной распылительной сушилки, откуда через секторный затвор и вибросито высыпаются на ленточный конвейер.
Готовый пресс-порошок по транспортерам и ковшовому подъемнику подается в силосы для хранения и вылеживания.
IV этап: прессование и сушка
Из силосов вылеживания базовый порошок и окрашенная масса в заданной пропорции по транспортеру подаются в миксер, где происходит их тщательное перемешивание. Далее по транспортеру и элеватору масса подается в стальную воронку для пресса через контрольное сито.
Пресс-порошок засыпается из стальной воронки в устройство для подачи порошка на пресс. Полусухое прессование происходит в три стадии: первичное давление, выдержка (для выхода воздуха), вторичное давление. Удельное давление прессования 350 кгс/см2 Максимальное давление прессования — 2500 тонн.
Далее отпрессованная плитка-сырец выталкивается кареткой пресса на сборник у пресса и по транспортерам подается в горизонтальную сушилку для полного удаления влаги. Сушка осуществляется за счет воздуха, нагретого предварительно газовой горелкой. После горизонтальной сушилки плитка подается на машину для разгрузки сушилки.
V этап: глазурование
По соединительной линии между сушилкой и печью плитка транспортируется от машины для разгрузки сушилки до печи, в это время на плитку наносится ангоб на тыльную сторону и, при необходимости, эффект «рустика» на щеточной машине.
VI этап: обжиг
В процессе обжига происходит полное спекание продукта и приобретение им всех физико-механических свойств. Максимальная температура обжига 1250°С.
VII этап: сортировка и упаковка
Готовая плитка поступает на линию сортировки, где, после автоматического контроля геометрии и визуального контроля, она автоматически упаковывается и укладывается на поддон
Технология производства: состоит из четырех этапов: производство исходной смеси из глины формовка обжиг и проверка качества сортировка и складирование Производство исходной смеси из глины Формовка Обжиг Проверка качества керамогранита Вес керамогранита На современном рынке строительных материалов керамический гранит пользуется высоким спросом и популярностью. Это связано с уникальными физико-эксплуатационными показателями искусственного камня, которые позволяют использовать его в области отделки для решения задач любой сложности. В зависимости от применяемой технологии производства он приобретает специфические параметры: габаритные размеры (ширина, длина, толщина) и объемный вес керамогранита. Плитки керамического гранита — это достаточно тяжелый материал. Исходным сырьем для производства керамогранита являются песок, глина, шпат, красители. Компоненты измельчаются до однородной консистенции и прессуются под значительным давлением. Большая масса и высокая плотность изделия обеспечивают ему особую прочность и долговечность. Для правильного определения массы продукции необходимо учитывать показатель удельного веса керамогранита, который с учетом европейских нормативов составляет около 2400 кг/м3. Эта величина практически равна удельному весу стекла. Стекло и керамический гранит часто применяют вместе для обустройства зданий и монтаже вентилируемых фасадов. Одинаковые параметры удельного веса существенно упрощают рабочий процесс сборки элементов конструкции. Ориентировочно вес м2 керамогранита варьируется в пределах от 11 до 25 кг. Более легкий вариант подходит для использования на стенах, тяжелый — для укладки на полу. Кроме того, масса материала зависит от его формата, поэтому вес плитки керамогранита 30*30 будет меньше веса керамогранита 60*60. Выпускают плитку различных размеров толщиной 7 — 30 мм. Плитка для пола успешно выдерживает повышеную нагрузку и механическое воздействие. Увеличение толщины изделия позволяет применять ее для укладки в местах высокой проходимости, более тонкие — для обустройства стен. Большой вес керамогранита 60х60 создает определенные трудности при монтаже, но при этом такая плитка имеет значительное преимущество в плане долгого срока эксплуатации. Для того чтобы не ошибиться с выбором подходящего варианта можно самостоятельно рассчитать вес упаковки керамогранита. Например, чтобы узнать вес плитки керамогранита 600х600 следует умножить ее объем на удельный вес. Полученный результат одного типоразмера будет различаться в зависимости от толщины изделия. Существует прямая зависимость между массой, толщиной и форматом изделия. Традиционно толщина плитки в формате 30х30 составляет 8 мм, 45х45 — 9 мм, 60х60 — 10 мм. При толщине 8,0-8,5 мм 1 м2 керамогранита весит 18,5-19 кг. Для обеспечения транспортировки товара до места назначения необходимо знать, например, вес керамогранита 300х300, который измеряется в килограммах. Информацию можно взять из каталога продукции, где указан вес керамогранита 30х30 одной плитки, м2 и вес брутто. Также на упаковке обозначается количество плиток в 1 м2 и на поддоне, размер поддона и сколько кв.м товара поместится на нем. |
Сырье Сырье для производства керамического гранита — это несколько видов глины: 1. Тугоплавкая глина — именно она отвечает за все керамические свойства керамогранита; Все вышеперечисленное сырье, смешанное в определенных пропорциях, составляет основу керамического гранита и обеспечивает технологические свойства перерабатываемой массе, внешний вид и технические данные готовых керамических изделий. К «вторичному» сырью относят: Для того, чтобы готовый керамический черепок получился более прочным, в раствор во время приготовления добавляют полевой шпат и кварцевый песок. Для производства керамогранита ещё необходима глина малой пластичности, насыщенная каолином. |
УСТАНОВКИ ДЛЯ ПРОИЗВОДСТВА КЕРАМОГРАНИТА СУХИМ МЕТОДОМ
Процесс подготовки сырья методом «DRY-TECH Porcelain» — это технологическое решение, разработанное компанией “Манфредини & Скиянки” для того, чтобы значительно снизить стоимость процесса изготовления КЕРАМОГРАНИТА, оставив неизменным его качество.
Благодаря скрупулезному анализу керамического сырья своих заказчиков и используя мощности своих лабораторий и своей тестовой промышленной установки, компания “Манфредини & Скиянки” разработала оптимальную рецептуру массы для производства керамического гранита высокого качества по собственной технологии «DRY-TECH».
Основными преимуществами процесса «DRY-TECH» являются:
-
Значительное уменьшение потребления термо и электроэнергии
-
Использование менее дорогостоящего сырья, не прошедшего отбор для традиционного метода производства по причине своей вязкости
-
Нет необходимости в использовании разжижителей
-
Небольшие габариты установки
-
Высокая степень автоматизации
-
Постоянство качества плитки
-
Значительное снижение объемов технического обслуживания по сравнению с традиционными линиями
-
Практически полный отказ от применения воды и выбросов газа, вредящего окружающей среде
Процесс производства «DRY-TECH», разработанный компанией “Манфредини & Скиянки” – это альтернативная традиционному процессу система обработки сырья, наиболее используемая по всему миру. Различные заказчики компании производят данным способом более 850.000.000 кв.м/год напольной и облицовочной плитки.
Последующее развитие технологии «DRY-TECH Porcelain» позволяет использовать ее для производства сухим методом любых типов керамической плитки и получаемые результаты полностью соответствуют действующим нормативам UNI.
Потребление |
Процесс «DRY-TECH» |
Влажный способ |
Вода (л/т) |
36 |
266 |
Электричество (кВт/т) |
39 |
55 |
Природный газ (м. |
3,9 для влажности в 12% |
45 |
Персонала в смену |
2 человека |
3 человека |
Стоимость обслуживания (€/т) |
5,5 |
7,5 |
, 220 10 .
, 0,075%, 750 ppm.
, , , .
CO2 1 15C | |
DRY-TECH | 3,9 .![]() |
45 ./ 80,96 CO2 |
Emissioni di NOX ad una pressione di 1 bar e temperatura di 15°C | |
DRY-TECH | 0 |
1500 mg/Nmc |
DRY-TECH | 10 mg/mc |
30 mg/Nmc |
.
Технологический процесс производства керамической плитки
Акция интернет-магазина Steps.ru |
Cooperativa Ceramica d’Imola вложила в технологию производства керамической плитки и керамогранита не только свой огромный опыт, приобретенный за более чем 130-летную историю компании, но и мастерство коллектива, выполняющего исследования, инновационные разработки и современные способы производства, а также дизайнерский и технологический профессионализм. В технологии производства керамической плитки и керамогранита учитывается всё: исходное сырье для плитки, состав эмалей, способ нанесения изображения и обработки плитки.
Технология производства керамической плитки и керамогранита Cooperativa Ceramica d’Imola обеспечивает необходимое качество продукции, предъявляемое сейчас на мировых рынках (плитка соответствует международным стандартам 9001), и оптимизирует затраты, что выигрышно влияет на формирование конкурентоспособности плитки ТМ Имола на керамическом рынке.
При производстве современной плитки применяются более разнообразные технологии, позволяющие получить материалы практически любых цветов, форм и размеров. Несмотря на свое огромное разнообразие абсолютное большинство керамических изделий можно разделить по способу производства на три группы. Это — неглазурованные плитки (в основном керамический гранит, он же gres porcellanato (итал.)), глазурованные плитки двукратного обжига (как правило, настенная плитка) и глазурованные плитки однократного обжига. Технология их производства во многом схожа, но имеется и ряд принципиальных отличий.
Этапы производства неглазурованной плитки
- Выбор сырья
- Приготовление смеси
- Формовка
- Сушка
- Обжиг
Этапы производства глазурованной плитки однократного обжига
- Выбор сырья (в том числе и для глазури)
- Приготовление смеси (в том числе и для глазури)
- Формовка
- Сушка
- Нанесение глазури
- Обжиг
Этапы производства глазурованной плитки двукратного обжига
- Выбор сырья (в том числе и для глазури)
- Приготовление смеси (в том числе и для глазури)
- Формовка
- Сушка
- Обжиг
- Нанесение глазури
- Повторный обжиг
Выбор сырья
В качестве сырья для основания плитки используют кварцевый песок (ограничивает изменение размеров при сушке и обжиге), глину (обеспечивает необходимую при формовке пластичность), фелдшпатовые и карбонатные материалы (обеспечивают вязкость при обжиге для создания стекловидной и плотной структуры материала).
Основу керамической глазури составляют фритты — сплавы солей со стеклом. Глазурь, состоящая только из фритт, имеет глянцевую поверхность и применяется, как правило, при двукратном обжиге. Для создания матовых глазурей во фритты могут добавлять кварц, окислы металлов, каолин, красящие пигменты.
Приготовление смеси
Приготовление смеси включает в себя несколько операций, которые обеспечивают получение измельченного однородного материала с определенным содержанием влаги, необходимой для последующей формовки. Измельчение сырья нужно для облегчения последующего процесса обжига керамического изделия.
Существует два основных метода приготовления смеси: мокрый и сухой. При использовании мокрого метода измельчение и смешивание составляющих смеси происходит в специальных центрифугах, куда вместе с сырьем помещаются очень прочные шары из металлокерамики и вода. В процессе вращения центрифуги эти шары ударяясь друг с другом измельчают сырье до состояния водной суспензии (шликера). Далее необходимая для равномерного смешивания влага удаляется процессом атомизации (противоточное распыление шликера горячим потоком воздуха с немедленным испарением влаги). В итоге получается порошкообразная смесь с необходимым для формовки содержанием воды (4-7% для метода прессования).
Основное отличие сухого метода от мокрого заключается в том, что сырье измельчается без добавления воды. Увлажнение его происходит позже в специальных машинах.
Технология мокрого измельчения дороже (необходимо много энергии для удаления воды), но дает лучшие результаты. Поэтому при производстве керамогранита и монокоттуры используют именно этот метод.
Формовка
Все современные способы формовки керамической плитки, согласно норм ISO, разделяют на три группы. Группа А — метод экструзии (производство плиток котто, клинкер). Группа В — метод прессования (керамогранит, монокоттура, бикоттура). В группу С вошли все прочие способы (например, ручная формовка, литье стеклянной мозаики).
Наибольшее распространение получил метод прессования (около 98% всей керамической плитки). При прессовании порошкообразную смесь загружают в пресс-формы гидравлического пресса, где она под высоким давлением (до 500 кг/см.кв.) уплотняется и приобретает определенную прочность. Уже на этом этапе плитка может подвергаться дополнительной обработке. Так для получения преполированного керамогранита поверхность плитки шлифуется мягкими щетками еще до обжига. С помощью пресс-форм задаются не только геометрические формы и размеры керамической плитки, но и фактура ее поверхности (например, у Pietra d’Italia — рельефная, у Celadon — вогнутая и т.д.).
Сушка
В процессе сушки из изделия удаляется влага, которая была необходима для формовки. Ее содержание уменьшается до 0,2%. Процесс осуществляется в сушильных установках с сушкой горячим воздухом.
Нанесение глазури
На сегодняшний день существует несколько десятков способов нанесения глазурей на поверхность керамической плитки. Глазурь может наноситься в виде гранул, пастообразной массы или распыленной суспензии. Момент нанесения может происходить по разному: до обжига, после обжига и даже во время обжига. Для придания плитке более эстетичного вида процесс глазурирования может применяться совместно с нанесением различных изображений. Один из самых распространенных способов нанесения орнаментов называется шелкографией, когда через специальную сетку с различными по своей величине и частоте отверстиями с помощью красок наносят рисунки. Чем сложнее рисунок, тем больше сеток применяется.
Обжиг
Затем происходит обжиг плитки, который может длиться от 40 до 120 минут. Печь для обжига — закрытый конвейер длиной от 50 до 80 метров. Посредством подачи газа по трубам на каждые 20 см печи в каждой точке поддерживается определенная температура. Таким образом, в процессе движения по печи изделие обжигается при температуре от 200 до 1200 градусов по Цельсию. Если представить себе график, где по горизонтали отражается расстояние, пройденное изделием внутри печи, а по вертикали — температура на этой отметке, то получится нечто подобное следующему рисунку.
Наиболее важный элемент процесса обжига плитки — разработка и соблюдение температурной кривой. Именно правильное построение температурной кривой отражается на важнейших технических показателях плитки в дальнейшем. Следует отметить, что как только меняется партия сырья, температурная кривая должна быть разработана заново. Поэтому очень важно для производителя плитки постоянный поставщик сырья. И, следовательно, только те производители, кто имеет давний опыт производства, способны обеспечить стабильное качество. Для каждого типа плитки (а иногда и для каждой коллекции) разрабатывается индивидуальный температурный режим. Отличается и максимальная температура обжига для разных материалов. У плитки двойного обжига — около 950°С, у однократного обжига — до 1180°С, у керамогранита — до 1300°С. В процессе обжига при высоких температурах плитка теряет влагу и уменьшается в размерах (ужимается). Величина усадки растет с температурой обжига и может варьироваться от 0% (у плитки двукратного обжига) до 8% (у керамогранита). Т.е. для получения керамического гранита размером 300*300 размер пресс-формы должен быть 324*324.
Однократный обжиг (monocottura), когда глазурь и основание обжигаются вместе — используется, как правило, для производства напольной глазурованной плитки. Высокая температура обжига позволяет получить хорошо спеченный прочный бисквит, и обеспечивает значительную устойчивость глазури к истиранию. При данном способе производства невозможно получить изделия ярких, насыщенных цветов, поскольку при высоких температурах красящие пигменты выгорают и тускнеют. Замечено, что менее яркие глазурованные плитки более устойчивы к истиранию поверхности.
Двойной обжиг (bicottura) используется для производства настенной глазурованной плитки. Он состоит из двух этапов. На первом — обжигается только основание плитки. Обжиг производится при достаточно невысоких температурах. В результате получается высокопористый (более 10%) черепок, не подвергнувшийся усадке и не требующий в дальнейшем сортировки плитки по размерам (калибровки). Далее на основание наносится глазурь и происходит вторичный обжиг, характеризующийся еще более низкой температурой (700-900 градусов). Общий смысл поэтапного обжига — обеспечение необходимых прочностных характеристик бисквита (необходимы высокие температуры), и сохранение цвета желаемой яркости и насыщенности (при низких температурах красящие пигменты практически не выгорают).
Декор производится при помощи 3-его обжига. Сперва на уже готовую плитку наносят необходимый рисунок. Делается это различными способами в зависимости от ожидаемого эффекта — нанесением рисунка через сетки или трафареты красками, золотом, глазурью (иногда в виде порошка). После изделие обжигается при еще более низкой температуре (до 700 градусов). При этом порошок глазури расплавляется, образуя рельефный рисунок. Затем, если декоры производятся на фоновой плитке, осуществляется их нарезка (Berillo, Prado и др.). Достаточно много декоров производится из гипса (основание), а потом раскрашиваются и глазуруются вручную. Такие декоры достаточно часто имеют геометрические отклонения от идеала по причине непредсказуемого поведения гипса при обжиге. О таких отклонениях следует сообщать клиентам при выборе именно таких декоров. Поскольку процесс производства декоративных элементов наиболее длительный и сложный, декоры имеют большую стоимость по сравнению с фоновой плиткой.
После обжига плитки осуществляется визуальный контроль качества — деление на 1, 2, 3 сорта. Далее осуществляется компьютерный оптический контроль качества — снятие геометрических параметров (определение калибров для монокоттуры и керамогранита, определение плоскостных параметров и др.). Затем изделия сканируются для определения и идентификации оттенков плитки, путем сравнения с компьютерной библиотекой ранее произведенных изделий того же артикула.
Просмотров статьи: 31301 с 19.11.2008
Ознакомиться с изданиями из категории «Программа Кафель»
Плитка как это сделано
Актуальные знания о том, как создается этот старинный продукт.
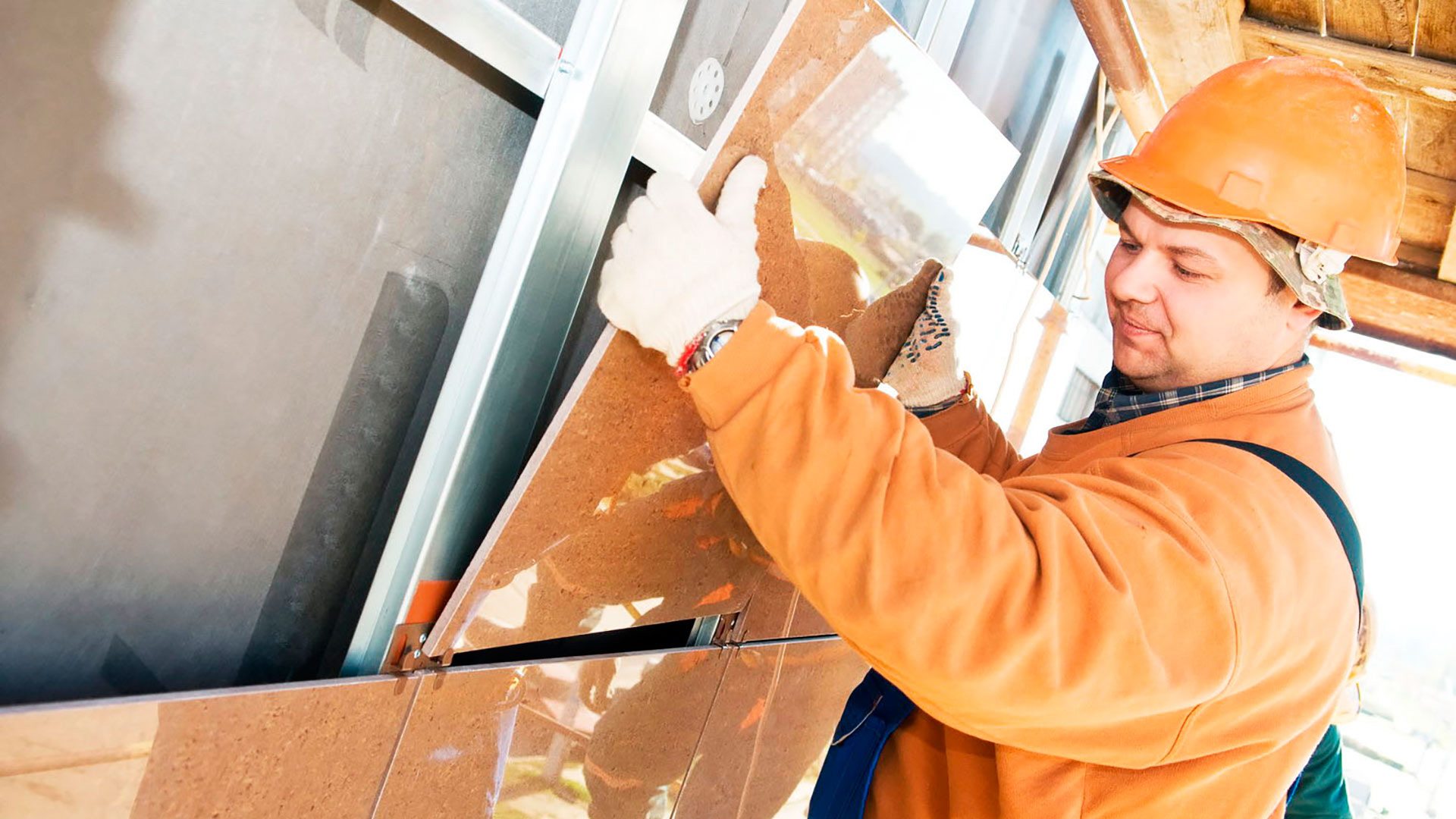
Независимо от того, какое напольное покрытие вы выберете в конечном итоге, оно будет сконструированы или изготовлены каким-либо образом. Но как создается керамика в мире все свое.
Это древний процесс, и его преимущества многочисленны и желательны: красота, долговечность, практичность и универсальность.
Керамическая плитка — это произведение искусства, по которому вы идете — эффектный вход, освежающий Поверхность для ванны / спа, изысканная кухня радует глаз. Керамическая плитка искусство под ногами, которым вы восхищаетесь как владелец и жаждете как посетитель.
Понимание того, как производится керамика, дает вам представление о ней с самого начала.
рождение. Это важная информация, потому что это материалы, которые вы
Если вы выберете этот продукт для пола, вы будете жить с ним долгие годы.
Знание керамической конструкции также поможет вам лучше понять и оценить ее характеристики. аспекты. Вы узнаете, почему некоторые керамические изделия легче чистить, чем другие; почему некоторые более прочные.
Кроме того, понимание того, как делают керамику, может сделать вас лучшим покупателем, поможет вам определить стоимость керамического пола и держать вас «в плюсе» в отношении ваш бюджет на улучшение дома.
Пожалуйста, продолжайте читать, и мы поможем вам узнать, как производится керамика. различные этапы, обсудите альтернативные типы керамики и предложите вам простой чтобы понять систему оценки истирания.
Керамическое производство объединяет землю и огонь.
Основные ингредиенты керамической плитки и общий процесс ее изготовления не имеют это сильно изменилось на протяжении веков.
Вся керамическая плитка создается из натуральных продуктов, добытых из земли, которая формуются в плитки, а затем обжигаются в печах при очень высоких температурах.
Справочник по двум классам керамической плитки.
Существует 2 основных типа конструкции плитки: глазурованная и неглазурованная .
Если посмотреть на глазурованную плитку сбоку, можно увидеть 2 слоя.Тело плитка, или самый большой слой, называется бисквитным. Верхний слой называется глазурью, как в глазированном пончике.
Глазурованная плитка после обжига имеет твердую непористую непроницаемую поверхность. Они есть более устойчивы к пятнам, чем неглазурованная плитка, и их легко чистить. Кое-что рассмотреть для более активных зон вашего дома, таких как кухня и ванные комнаты.
Неглазурованная плитка придаст вашему дому совершенно иную красоту.Они однотонные полностью и без верхнего слоя глазури. Это часто упоминается к как сквозной корпус конструкции.
Они не имеют дополнительных поверхностных покрытий и, как правило, более плотные и долговечные. чем глазурованная плитка. Таким образом, они больше подходят для внутреннего и внешнего применения. где удобство ношения является проблемой.
Если в вашем доме есть зоны повышенной активности или детские «зоны», неглазурованная плитка может быть просто ответом.
Процесс производства керамической плитки состоит из 5 этапов: добыча, смешивание и Смешивание, прессование, глазирование и обжиг.
Шаг 1 базовый и органичный.
Процесс начинается с добычи сырья, которое представляет собой смесь, состоящую из в основном из глины и минералов.
Шаг 2 превращает грязь в мелкий песок.
Глина и минеральная смесь перемешиваются и превращаются в полутонкодисперсный порошок.
Вода добавляется для образования влажной суспензии или консистенции грязи. Затем суспензия перекачивается в большую сушилку.
И результат? Мелкий глиняный порошок, напоминающий теплый мелкий песок.
Шаг 3 видит, как форма обретает форму.
Затем из глины прессуют или формуют плитку. Эти прессованные плитки называются зеленых плиток на данном этапе.
Существует также другой метод под названием экструзия , который может заменить прессование. шаг. Экструдированные плитки формируются путем продавливания глиняного материала через форму для желаемой формы по сравнению с нажатием плитки.
Однако сегодня более распространенным методом является прессование.И после зеленой плитки образуются, их сушат, чтобы удалить часть влаги.
Шаг 4 — фаза глазури.
Это следующий шаг в процессе производства плитки, которая будет есть глазурь.
Если плитка должна оставаться неглазурованной, она пропускает этот шаг и сразу переходит к обжигу. печь.
Жидкая глазурь приготовлена из производного стекла под названием фритта и окрашена. красители.Глазурь наносится либо распылителем под высоким давлением, либо заливается напрямую. на плитку.
Шаг 5 действительно нагревает.
Керамическая плитка теперь обжигается в печи при температуре около 2000 градусов. Фаренгейт.
Плитка, которую обжигают один раз после нанесения глазури, называется плиткой монокотурра . или одинарного выстрела .
Другой тип — biocuttura или плитка двойного обжига . Biocuturra плитки сначала обжигаются после высыхания зеленой плитки, а затем снова обжигаются после применяется глазурь.
Необязательный прочный выбор — фарфор.
Помимо двух видов керамической плитки, глазурованной и неглазурованной, существует еще одна категория. что продолжает набирать популярность — красивый, нарядный, керамогранит.
Керамогранит на 50% состоит из полевого шпата и обжигается при гораздо более высокой температуре. чем обычная керамическая плитка. Это делает керамогранит намного тверже и плотнее. чем другие изделия из плитки.
Их высокая производительность и низкие показатели водопоглощения менее 0,5 процента. сделайте эту плитку достойным выбором для вашего дома.
Кроме того, керамогранит можно использовать для внутренних и внешних работ. а также тяжелые или коммерческие помещения.
После проверки качества готовой плитки она упаковывается, упакованы и готовы к отправке.
Поймите это, чтобы быть опытным покупателем плитки.
Не вся керамическая плитка подходит для каждой зоны вашего дома. Красивый, декоративный плитка, которую вы можете положить на кухонный фартук, не рекомендуется для укладки на полу.
У большинства производителей есть рейтинговая система, основанная на американской Общество испытаний и материалов (ASTM). Много раз вы можете найти эти рейтинги на образце плитки или в каталоге продукции.
Наиболее распространенная система оценивает стойкость керамической плитки к истиранию или общую долговечность. плитки. Вы должны знать 5 классов.
Класс 1: без пешеходного движения.
Эти плитки рекомендуются только для внутренних стен, а не для пола.
Класс 2: легкое движение.
Эти плитки рекомендуются для внутренних стен и для жилых ванных комнат. только пол.
Класс 3: от легкого до умеренного движения.
Эти плитки можно использовать для полов и стен в жилых домах, включая ванные комнаты, кухни, холлы, столовые и семейные комнаты.Они хорошие универсалы исполнитель.
Класс 4: от умеренного до интенсивного.
Эти плитки рекомендуются для жилых, средних коммерческих и легких промышленных предприятий. полы и стены, включая торговые центры, офисы, рестораны комнаты, выставочные залы и коридоры.
Класс 5: интенсивное / сверхтяжелое движение.
Эти плитки можно установить где угодно.Они подходят для напольных и настенных покрытий. в аэропортах, супермаркетах и метро. Плитка не становится более жесткой.
Вы также можете увидеть рейтинг сопротивления скольжению, который измеряется его коэффициентом. трения (COF). Чем выше коэффициент трения, тем более устойчива плитка к скольжению. Это важно при выборе напольной плитки для участков с повышенной влажностью, например для душа или пол в ванной.
Другие рейтинги, перечисленные производителем, могут включать: устойчивость к царапинам, влажность. абсорбция, химическая стойкость и прочность на разрыв.
На этом мы завершаем наш раздел, посвященный изготовлению керамики — ее различным типам. конструкция, процесс производства и оценка плитки с точки зрения активности.
Мы надеемся, что знание того, как делают керамическую плитку, поможет вам с выбором подходит ли он для вашего дома и для вашего стиля жизни.
(PDF) Технологические и композиционные требования к глиняным материалам для керамической плитки
В этом контексте можно наметить некоторые краткосрочные тенденции применения глины
в производстве керамической плитки:
— спрос на очень пластичный и низкий -Fe, низкотитанистая шариковая глина
будет увеличиваться с увеличением производства керамогранита
;
— обычные шариковые глины
будут ограничены корпусами для глазурованной плитки быстрого обжига
(монокоттура);
— мергелевые глины и красные сланцы
будут использоваться только в корпусах красного цвета для глазурованной плитки;
— каолинитовые суглинки
и другие нетрадиционные белоснежные глины будут отклонены или ограничены
для глазурованной плитки быстрого обжига.
Эти тенденции указывают на некоторые нерешенные проблемы и темы для будущих исследований:
— необходимы новые минеральные обработки для снижения процентного содержания железа и титана в шариковых глинах;
— требуется лучшее понимание реологии скольжения, чтобы позволить более широкое использование смектита и интерстратифицированного I / S
;
— необходимо разработать специальные добавки для уменьшения красящего эффекта железа и титана
в керамогранитной плитке;
— эксплуатация огромного количества каолинитовых суглинков, красных сланцев и других глинистых материалов
больше не используется в производстве плитки.
ССЫЛКИ
1. P.G. Burzacchini, Ceram. Inf., 20 (1985) 283
2. M. Bertolani, Fabbri B., Fiori C., Loschi Ghittoni A.G., Ceram. Инф., 21 (1986) 333
3. П.Г. Burzacchini, Ceram.World Rev., 11 (2001) 114.
4. P.G. Burzacchini, Ceram. World Rev., 10 (2000) 96.
5. M. Poppi, La Ceramica, 32 (1979) 1
6. C. Palmonari, F. Cremonini, A. Tenaglia, G. Timellini, La Ceramica, 34 (1981) 1
7. A. Brusa, Int.Ceram. J., October (1999) 73.
8. M. Dondi, Appl. Clay Sci., 15 (1999) 337.
9. A. Escardino, A. Barba, A. Blasco, F. Negre, Br. Ceram. Trans., 94 (1995) 103
10. JE Enrique, A. Escardino, J. Garcia-Ten, V. Cantavella, 4th QUALICER, 2 (1998) 69
11. M. Dondi, Tile & Brick Int. , 10 (1994) 77
12. M. Dondi, G. Guarini, S. Guicciardi, C. Melandri, M. Raimondo, Ceram. Инф., 35 (2000)
985
13. М. Донди, Г.Ercolani, M. Marsigli, C. Melandri, C. Mingazzini C., Interceram, 48
(1999) 75
14. A. Brusa, A. Bresciani, Ceram. Англ. Sci. Proc., 17 (1996) 50
15. Брезина М., Керам. Англ. Sci. Proc., 20 (1999) 113
16. А. Альбертацци, Э. Растелли, Ceram. Acta., 9, № 4 (1997) 5
17. V. Capucci, Int. Ceram. J., 59 (1993) 14
18. Fabbri, C. Fiori, I. Venturi, Ceramurgia, 11 (1981) 131
30
Представленные данные являются ориентировочными и могут изменяться без уведомления |
Arquitecturas Cerámicas | Основы — Arquitecturas Cerámicas
Этот процесс заключается в нанесении тонкого слоя глазури, который прилипает к поверхности изделия в процессе плавления, образуя защитное непроницаемое покрытие, которое добавляет новые технические и декоративные свойства, такие как сопротивление скольжению, химическая стойкость и т. Д. и механическая прочность, а также блеск или цвет.
Используемое сырье может быть измельчено во влажном состоянии, давая шликер, напоминающий суспензию, использованную при изготовлении керамического тела, хотя он содержит частицы меньшего размера и большее количество воды. Их также можно измельчить в сухом виде и диспергировать в воде или нанести в сухом виде для специальных эффектов.
Существует множество глазурей, адаптированных к разным поверхностям и температурам обжига. В настоящее время также можно найти глазури с самоочищающимися или биоцидными свойствами, что является результатом постоянных технологических инноваций в секторе керамической промышленности.
Составы глазури в основном состоят из фритт, нефритсодержащего сырья, добавок и керамических красителей. Эти ингредиенты комбинируются по-разному, в зависимости от целевого продукта.
Компоненты
Фриц . Неорганические химические вещества получают путем быстрого охлаждения (закалки) сложной комбинации материалов, похожих на битое стекло. Использование фритты снижает токсичность процесса, расширяет диапазон обжига и обеспечивает более однородную отделку.
Нефриттовое сырье .Вещества, содержащие различные типы оксидов, ответственные за придание композиции глазури желаемых характеристик.
Присадки . Вещества, добавленные в сырье, улучшают определенные технические качества. Среди различных типов особо следует отметить суспендирующие агенты, дефлокулянты и связующие.
Красители . Вещества, добавленные в сырье, изменяют цветовые характеристики и придают глазурованным поверхностям их безупречный внешний вид.
Процесс
Чтобы выполнить процесс остекловывания на поверхности керамической детали, необходимо заранее нанести слой ангоба, который действует как связь между корпусом и глазурью, обеспечивая надлежащее закрепление между ними. Ангоб устраняет внешние неровности и скрывает цвет основы, обеспечивая однородную поверхность и создавая непроницаемый слой для предотвращения проблем с пористостью.
Глазурь наносится на слой ангоба в виде водной суспензии, все ее свойства приобретаются по окончании обжига, образуя устойчивое, плотное покрытие с однородной толщиной, известное как консолидированный слой.Существуют различные методы нанесения: вручную, сухое нанесение, распыление и непрерывное нанесение завесы, последние два из которых являются наиболее распространенными в керамической промышленности.
Руководство . Это делается с использованием ручных методов, таких как заливка или окунание, или с использованием другой посуды, и выполняется мастером или художником.
Сухое нанесение . Это выполняется с помощью устройств, которые дозируют частицы сухой измельченной фритты разного размера или продукты, полученные гранулированием или термическим размягчением глазури.
Распыление . Это выполняется с помощью вращающегося диска, который наносит мелкие капли на поверхность изделия, образуя сплошной тонкий слой с шероховатой отделкой.
Сплошная завеса . Используется стеклянный колокол. Шликер стекает по внешней поверхности колокола непрерывным водопадом, покрывая керамический корпус слоем глазури большей толщины и гладкой текстуры.
Керамическая исследовательская компания
Процесс производства керамической плиткиПроцесс производства керамической плитки показан на Рисунке 1
Рисунок 1: Блок-схема производственного процесса керамической плитки.После [1] Биффи стр.28
Подготовка туши начинается с дозирования или дозирования различных сырьевых материалов в нужных количествах. Смешивание корпуса из отдельных компонентов следует за грубым измельчением сырья и осуществляется в соответствии с рецептурой корпуса. В настоящее время грубое измельчение материалов часто выполняется поставщиками сырья [2].
Дозирование или дозирование может производиться по объему или по массе. Однако дозирование по массе намного точнее, чем по объему, и поэтому является предпочтительным.Автоматическое взвешивание и подача сырья позволяет лучше контролировать смесь сырья, уменьшая возможные отклонения, которые могут привести к изменению свойств тела [3].
Измельчение твердого сырья включает в себя целый ряд операций, направленных на уменьшение размеров материалов. Цель измельчения — получить более мелкие частицы из более крупных. Кроме того, это также увеличивает реакционную способность материалов (особенно полевого шпата), так что обжиг является эффективным, а также дает такое распределение материалов по размерам, чтобы они могли упаковываться, давая высокую плотность упаковки [4].По сути, существует два метода измельчения, а именно метод мокрого и сухого измельчения. В обоих случаях необходимо снизить степень измельчения материалов, чтобы исключить опасные примеси, которые могут вызвать пятна или неисправности [2].
Для метода мокрого измельчения различные сырьевые материалы, такие как глина, флюс (полевой шпат) и наполнитель (обычно песок), входящие в состав тела, хранятся в отдельных отсеках. Сырье взвешивается пропорционально рецептуре и загружается в шаровые мельницы (рис. 2) вместе с подходящим количеством воды и дефлокулянта для облегчения диспергирования.Одной из целей измельчения является получение высокого уплотнения основного порошка путем получения ряда крупных, средних и мелких частиц в гранулометрическом составе шликера шаровой мельницы [4].
Рис. 2. Типовая шаровая мельница, размер = 20 тоннПри мокром периодическом измельчении мельница загружается, измельчается и затем выгружается с последующим заполнением новой загрузкой для измельчения. Как только шликер достигает желаемого размера, его выгружают в подземный резервуар для хранения и выдерживают в течение 24 часов.Второй способ измельчения — это сухое измельчение. Существует несколько типов мельниц, которые измельчают сырье с влажностью от 8 или 10% до 100%, проходя через сито.
С технологической точки зрения при сухом измельчении невозможно достичь такой же степени тонкости помола, как при мокром измельчении. В настоящее время метод мокрого шлифования является наиболее часто используемым при производстве плиток из керамогранита. При использовании метода мокрого измельчения гранулированный порошок, полученный в процессе распылительной сушки, больше подходит для правильного заполнения прессов благодаря своей оптимальной форме и гранулометрическому составу.Загрязнения, которые могут присутствовать, удаляются просеиванием шликера, полученного мокрым измельчением [4].
Для керамической плитки сушка распылением — это процесс, при котором шликер, полученный на мельнице, преобразуется в гранулят с распределением по размерам и содержанием влаги, пригодным для прессования. Корпусный шликер распыляется под высоким давлением, а вода испаряется из мелких капель с помощью потока нагретого воздуха [6].
На рис. 3 показана схематическая конструкция распылительной сушилки.Объемный насос отправляет промывку на набор фурм, помещенных внутри сушилки. На концах копий шликер распыляется на мелкие частицы с помощью форсунок, а затем распыляется к верху сушильной камеры против одновременно нисходящего горячего воздуха, который быстро испаряет воду из шликера. Полученный распылительной сушкой порошок падает на дно сушилки, где он выгружается с помощью вытяжного клапана. Отработанный воздух проходит через набор циклонов для рециркуляции небольшого количества мелкодисперсного порошка, который он содержит, затем в систему мокрого скруббера для дальнейшей очистки, прежде чем он будет выпущен в виде пара [4,6].Двумя наиболее важными контролируемыми свойствами являются влажность и гранулометрический состав [4].
1 | Сушильная башня | 7 | Дымоход |
2 | Сушилка | 8 | Вытяжной вентилятор |
3 | Скользящий насос | 9 | Циклоны для удаления мелких частиц |
4 | Копье | 10 | Диффузор теплого воздуха |
5 | Форсунка для распыления | 11 | Вытяжной клапан |
6 | Нагреватель теплого воздуха | 12 | Панель управления |
Рисунок 3.Схема распылительной сушилки по Райану [4] стр .122 |
Целью этапа прессования является формование высушенного распылением порошка в уплотненный кусок необожженной плитки. Прессование — это одновременное уплотнение и формование порошка или гранулированного материала, заключенного в жесткую или гибкую пресс-форму [7]. Прессование высушенного распылением гранулята с последующей сушкой определяет размер и геометрию продукта. Прочность без обжига определяется достигнутым уплотнением.
Есть два типа прессов: гидравлический и фрикционный.Наиболее часто используемые прессы в производстве керамической плитки — это гидравлические прессы (Рисунок 4). Они предлагают преимущество постоянно высокого давления, которым можно относительно легко управлять. Их предпочтительно использовать при производстве продуктов однократного обжига, таких как глазурованные и неглазурованные керамические плитки и плитки большого размера, где постоянное давление является обязательным для точности размеров.
Рис. 4. Типовой гидравлический пресс, используемый на заводе по производству керамической плиткиДавление прессования разное для разных типов плитки.В случае белой напольной плитки используется давление ниже 300 МПа, в то время как для керамической плитки того же размера необходимо использовать давление 350-400 МПа [1].
Сушка керамической плитки осуществляется между стадией прессования и процессом обжига. Это выполняется для увеличения прочности необожженной плитки, а также для снижения риска потери плитки из-за деформации, поскольку плитка быстро сжимается или трескается, поскольку в печи быстро выделяется пар. Количество удаляемой воды зависит от метода формования и составляет от 3 до 6% для керамической плитки.Сушка плиток, спрессованных с пылью, более безопасна, чем сушка изделий, изготовленных методом формования пластика с более высоким содержанием влаги, потому что вода, которая отделяет частицы в этих последних изделиях, удаляется и вызывает усадку при высыхании. В настоящее время сушка корпуса плитки осуществляется автоматически и непрерывно в вертикальных или горизонтальных быстрых сушилках [4,8].
Обжиг обычно является заключительным этапом производства керамической плитки, на котором непрочный, необожженный, недавно спрессованный кусок плитки превращается в прочный, долговечный продукт из-за воздействия химических и физических реакций внутри зеленого тела во время нагрева [9 ].После обжига корпус керамической плитки принимает механические и эстетические свойства готового керамического изделия. Быстрый обжиг в один слой обеспечивает полностью равномерное распределение температуры и высокое качество плитки, как показано ниже.
Рис. 5. Типовая печь с роликовым подом с быстрым обжигом на заводе по производству керамической плиткиЦелями процесса обжига в роликовых печах (рис. 5) являются остекловывание массы и стабильность размеров в температурном интервале обжига.Завод по производству керамогранита завершается этапом сортировки. В линии отбора первостепенное значение имеет плоскостность и качество изделий [4].
Ссылки- Biffi, G. «Плитка из тонкого керамогранита — технология, производство и маркетинг» Gruppo Editorale Faenza Editrice
S.p.A (1994) - Fugmann, K.G. «Как производить плитку — подготовка» Interbrick, Том 5 №3, стр.34-40 (1989)
- Биффи, Г.; Cini, L .; Поцци, Д .; Поппи М. «Технические и технологические инновации в керамической промышленности» Ceramica Informacion, стр. 2–26 (сентябрь 1993 г.)
- Ryan, W. «Производство настенной и напольной плитки» Ceramic Research Company, Малайзия, стр. 52-75, стр. 99-147, стр.
185-200 (1999) - Fugmann, K.G. «Мокрый способ непрерывного фрезерования в производстве керамической плитки» Interbrick, Том 3 №1, стр. 42-43 (1987)
- Смит, Г. «Эксплуатация распылительной сушилки» Керамическая промышленность, стр.54-56 (июнь 1993)
- Рид, Дж. «Введение в принципы обработки керамики» John Wiley & Sons 1989
- SITI «Сушка, прессование» Societa Impianti Termoelettici Industriali CRC Centro Ricerche Ceramica Том 5 La Tecnogia Ceramica, стр. 9-24, стр. 61-63
- Manfredini, T .; Пенниси, Л. «Последние инновации в процессе быстрого обжига» Наука о белых изделиях, Американское общество керамики
.
% PDF-1.5 % 1 0 obj > >> эндобдж 4 0 obj / CreationDate (D: 20160527114308 + 02’00 ‘) / ModDate (D: 20160527114308 + 02’00 ‘) /Режиссер >> эндобдж 2 0 obj > эндобдж 3 0 obj > эндобдж 5 0 obj > / ProcSet [/ PDF / Text / ImageB / ImageC / ImageI] / XObject> >> / MediaBox [0 0 595,32 841,92] / Содержание [51 0 R 52 0 R 53 0 R] / Группа> / Вкладки / S / StructParents 0 >> эндобдж 6 0 obj > / ProcSet [/ PDF / Text / ImageB / ImageC / ImageI] >> / MediaBox [0 0 595,32 841,92] / Содержание 66 0 руб. / Группа> / Вкладки / S / StructParents 23 >> эндобдж 7 0 объект > / ExtGState> / ProcSet [/ PDF / Text / ImageB / ImageC / ImageI] >> / MediaBox [0 0 595.32 841,92] / Содержание 82 0 руб. / Группа> / Вкладки / S / StructParents 29 >> эндобдж 8 0 объект > / XObject> / ProcSet [/ PDF / Text / ImageB / ImageC / ImageI] >> / MediaBox [0 0 595,32 841,92] / Содержание 96 0 руб. / Группа> / Вкладки / S / StructParents 1 >> эндобдж 9 0 объект > / ExtGState> / XObject> / ProcSet [/ PDF / Text / ImageB / ImageC / ImageI] >> / MediaBox [0 0 595,32 841,92] / Содержание 109 0 руб. / Группа> / Вкладки / S / StructParents 2 >> эндобдж 10 0 obj > / XObject> / ProcSet [/ PDF / Text / ImageB / ImageC / ImageI] >> / MediaBox [0 0 595.32 841,92] / Содержание 118 0 руб. / Группа> / Вкладки / S / StructParents 3 >> эндобдж 11 0 объект > / XObject> / ProcSet [/ PDF / Text / ImageB / ImageC / ImageI] >> / MediaBox [0 0 595,32 841,92] / Содержание 130 0 руб. / Группа> / Вкладки / S / StructParents 4 >> эндобдж 12 0 объект > / XObject> / ProcSet [/ PDF / Text / ImageB / ImageC / ImageI] >> / MediaBox [0 0 595,32 841,92] / Содержание 141 0 руб. / Группа> / Вкладки / S / StructParents 5 >> эндобдж 13 0 объект > / ProcSet [/ PDF / Text / ImageB / ImageC / ImageI] >> / MediaBox [0 0 595.32 841,92] / Содержание 155 0 руб. / Группа> / Вкладки / S / StructParents 50 >> эндобдж 14 0 объект > / XObject> / ProcSet [/ PDF / Text / ImageB / ImageC / ImageI] >> / MediaBox [0 0 595,32 841,92] / Содержание 166 0 руб. / Группа> / Вкладки / S / StructParents 6 >> эндобдж 15 0 объект > / XObject> / ProcSet [/ PDF / Text / ImageB / ImageC / ImageI] >> / MediaBox [0 0 595,32 841,92] / Содержание 174 0 руб. / Группа> / Вкладки / S / StructParents 7 >> эндобдж 16 0 объект > / XObject> / ProcSet [/ PDF / Text / ImageB / ImageC / ImageI] >> / MediaBox [0 0 595.32 841,92] / Содержание 192 0 руб. / Группа> / Вкладки / S / StructParents 11 >> эндобдж 17 0 объект > / XObject> / ProcSet [/ PDF / Text / ImageB / ImageC / ImageI] >> / MediaBox [0 0 595,32 841,92] / Содержание 204 0 руб. / Группа> / Вкладки / S / StructParents 12 >> эндобдж 18 0 объект > / XObject> / ProcSet [/ PDF / Text / ImageB / ImageC / ImageI] >> / MediaBox [0 0 595,32 841,92] / Содержание 217 0 руб. / Группа> / Вкладки / S / StructParents 13 >> эндобдж 19 0 объект > / XObject> / ProcSet [/ PDF / Text / ImageB / ImageC / ImageI] >> / MediaBox [0 0 595.32 841,92] / Содержание 225 0 руб. / Группа> / Вкладки / S / StructParents 14 >> эндобдж 20 0 объект > / XObject> / ProcSet [/ PDF / Text / ImageB / ImageC / ImageI] >> / MediaBox [0 0 595,32 841,92] / Содержание 236 0 руб. / Группа> / Вкладки / S / StructParents 15 >> эндобдж 21 0 объект > / XObject> / ProcSet [/ PDF / Text / ImageB / ImageC / ImageI] >> / MediaBox [0 0 595,32 841,92] / Содержание 249 0 руб. / Группа> / Вкладки / S / StructParents 16 >> эндобдж 22 0 объект > / ProcSet [/ PDF / Text / ImageB / ImageC / ImageI] >> / MediaBox [0 0 595.32 841,92] / Содержание 259 0 руб. / Группа> / Вкладки / S / StructParents 85 >> эндобдж 23 0 объект > / ProcSet [/ PDF / Text / ImageB / ImageC / ImageI] >> / MediaBox [0 0 595,32 841,92] / Содержание 280 0 руб. / Группа> / Вкладки / S / StructParents 89 >> эндобдж 24 0 объект > / ProcSet [/ PDF / Text / ImageB / ImageC / ImageI] >> / MediaBox [0 0 595,32 841,92] / Содержание 293 0 руб. / Группа> / Вкладки / S / StructParents 104 >> эндобдж 25 0 объект > эндобдж 26 0 объект > эндобдж 27 0 объект > эндобдж 28 0 объект > эндобдж 29 0 объект > / F 4 / A> / Тип / Аннотация >> эндобдж 30 0 объект > / F 4 / A> / Тип / Аннотация >> эндобдж 31 0 объект > / F 4 / A> / Тип / Аннотация >> эндобдж 32 0 объект > / F 4 / A> / Тип / Аннотация >> эндобдж 33 0 объект > / F 4 / A> / Тип / Аннотация >> эндобдж 34 0 объект > / F 4 / A> / Тип / Аннотация >> эндобдж 35 0 объект > / F 4 / A> / StructParent 8 / Тип / Аннотация >> эндобдж 36 0 объект > / F 4 / A> / StructParent 9 / Тип / Аннотация >> эндобдж 37 0 объект > / F 4 / A> / StructParent 10 / Тип / Аннотация >> эндобдж 38 0 объект > / F 4 / A> / StructParent 17 / Тип / Аннотация >> эндобдж 39 0 объект > / F 4 / A> / StructParent 18 / Тип / Аннотация >> эндобдж 40 0 объект > / F 4 / A> / StructParent 19 / Тип / Аннотация >> эндобдж 41 0 объект > / F 4 / A> / StructParent 20 / Тип / Аннотация >> эндобдж 42 0 объект > / F 4 / A> / StructParent 21 / Тип / Аннотация >> эндобдж 43 0 объект > / F 4 / A> / StructParent 22 / Тип / Аннотация >> эндобдж 44 0 объект > эндобдж 45 0 объект > эндобдж 46 0 объект > эндобдж 47 0 объект > эндобдж 48 0 объект > эндобдж 49 0 объект > эндобдж 50 0 объект > поток x
Плитка Технические характеристики, надежность и безопасность материалов
Материалы Eiffelgres не боятся сравнения с натуральным камнем: техническая керамика Eiffelgres представляет собой точку соприкосновения между керамогранитом, производимым промышленными методами, и натуральностью добытого камня.
Технические свойства керамогранита гарантируют высокие эксплуатационные характеристики материала, что является одной из причин, по которой он также известен как технический керамогранит. Он предлагает идеальное решение для архитекторов и дизайнеров: материал для полов и стен, безопасный, прочный, экологически безопасный и обладающий высокой эстетической ценностью.
Заставить миллионы лет пролететь за несколько мгновений. Это наша основная цель: воссоздать необычайную и естественную красоту материи.Наша вторая цель — попросить технологию делать противоположное тому, что она обычно делает, то есть генерировать случайные выразительные черты, характерные для природных материалов.
Мы достигли этих двух целей благодаря упорным исследованиям и экспериментам в лабораториях завода Eiffelgres в Виано-ди-Реджо-Эмилия: самого передового производителя «технического керамогранита» в мире на сегодняшний день.
Технические свойства керамической плитки соответствуют особым требованиям, устанавливающим пределы и устанавливающим ориентиры, которым необходимо соответствовать, чтобы считаться хорошим качеством.
Эти предварительные условия представляют собой декларацию прозрачности в отношениях между производителем и покупателем и действуют как своего рода удостоверение личности для продукта. Стандарты UNI в Италии, стандарты EN в Европе и стандарты ISO во всем мире определяют наиболее важные характеристики керамической плитки первого выбора:
Регулярность
размеры / толщина / прямолинейность углов / прямые углы / плоскостность
Для получения высококачественных кафельных поверхностей на полу и стенах используемый материал должен быть безупречным.Характеристики, позволяющие нам получить превосходное техническое и эстетическое качество, гарантируются модульностью отдельных плиток, которые должны иметь одинаковые размеры и толщину, не должны иметь впадин или выступов (плоскостность) и должны иметь строго под прямым углом стороны.
Производство керамического материала путем однократного прессования под весом в тысячи тонн позволяет получить чрезвычайно ровные поверхности, и твердый керамогранит является ярким примером этого; его однородный внешний вид и четкая шлифовка по бокам и углам — вот некоторые из особенностей, которые помогают идентифицировать его как высокотехнологичное керамическое изделие.
Конструктивные особенности
водопоглощение
Водопоглощение зависит от пористости поверхности материала. Наименее пористым керамическим материалом является керамогранит с содержанием менее 0,5%. Высокотехнологичный керамогранит Eiffelgres впитывает воду на 0,04% благодаря особому процессу прессования, проводимому на заводе в Виано (RE).
Степень пористости керамического материала является важным требованием, поскольку она определяет многие другие характеристики, определяющие качество и надежность плитки.
Массивные механические свойства
сопротивление изгибу
Важным отличительным элементом полов является способность материала выдерживать заданные разрушающие нагрузки. Сопротивление изгибу, которое связано, прежде всего, с толщиной плиты, выше, если водопоглощение ниже: это еще один аспект, по которому керамогранит считается наиболее стойким материалом для плитки.
Механические свойства поверхности
устойчивость к глубоким царапинам
Керамические материалы должны гарантировать устойчивость к царапинам и износу из-за следов, а также к перемещению мебели, стульев, тележек на колесах и т. Д.с течением времени, чтобы сохранить первоначальную целостность их текстуры и их надлежащую функциональность. Отличительная компактность керамогранита гарантирует оптимальные характеристики с точки зрения устойчивости к царапинам и долговечности.
Тепловые и гигрометрические свойства
устойчивость к температурным колебаниям; морозостойкость; коэффициент линейного теплового расширения
Термогигрометрические свойства керамогранита зависят от его необычайной плотности.Поскольку керамогранит имеет самую низкую пористость среди керамических материалов, он поглощает меньше воды и, следовательно, подвергается меньшему риску растрескивания или растрескивания под давлением, вызванным увеличением объема воды при замерзании. Поэтому большие колебания температуры не являются проблемой для керамогранита, компактного материала, однородного по всей своей толщине.
Химические свойства
устойчивость к химическим продуктам
Чтобы противостоять воздействию химических веществ, например содержащихся в чистящих средствах или возникающих в результате использования кислот в определенных рабочих средах, компактность поверхности материала (которая в случае керамогранита распространяется по всей его толщине). ) представляет собой очень важное качество, еще раз связанное с низкой пористостью материала, которая исключает наличие микроскопических трещин, которые могут способствовать проникновению и застаиванию агрессивных веществ.Этому способствует высокая температура обжига, достигаемая в керамических печах (1200 °), что позволяет достичь большей химической инерции.
Функции безопасности
Коэффициент трения (скользкость)
Скользкость пола определяет безопасность людей, идущих по нему, и поэтому является важным требованием к полу.
Коэффициент скользкости, представленный значением «R», относится к методу, указанному в немецких стандартах DIN 51130 и 51097, которые классифицируют продукты на основе их коэффициента трения в соответствии с конкретными требованиями данной среды.
В зависимости от степени скользкости, которая может быть связана с использованием определенных веществ на рабочих местах или с наличием воды, в соответствии с этими правилами обязательно использовать напольный материал, который будет создавать значительное трение между соприкасающимися поверхностями и тем самым создавать пол менее опасен для людей. Чем выше коэффициент трения, тем менее скользкий пол.
Стандарты различают скользкость поверхностей пола в местах, где люди ходят в обуви (R9-R13) и босиком (A, B, C).
Метод измерения, указанный в DIN 51130, различает следующие классы скользкости и указывает, где они могут быть использованы:
- R9 — входы и лестницы с доступом снаружи; рестораны и столовые; магазины; клиники; больницы; школы.
- R10 — туалеты и душевые общие; небольшие кухни в ресторанах и кафе; гаражи и подвалы.
- R11 — объекты пищевой промышленности; кухни среднего размера в ресторанах и кафе; рабочие среды, где много воды и ила; лаборатории; прачечные; ангары.
- R12 — производство продуктов с высоким содержанием жиров, таких как молочные продукты, пищевые масла, колбасы; большие кухни в ресторанах и кафе; промышленные зоны, где используются тапочки; парковки.
- R13 — места употребления большого количества жиров; пищевая промышленность.
При наличии воды, когда люди ходят босиком, к напольному покрытию предъявляются еще более строгие требования.Их можно измерить в соответствии со стандартами DIN 51097 и разделить на группы оценки A, B и C с возрастающими значениями:
- А — раздевалки; участки, доступ к которым осуществляется босиком; пр.
- B — душевые кабины; бортики бассейна; пр.
- C — бортики бассейна наклонные; ступеньки для лазания в бассейны; пр.
Светостойкость
Химические и физические свойства, которые Eiffelgres требует от своих материалов, также включают светостойкость цветов, стандарты для которых установлены немецкими стандартами DIN 51094.
Необходимость проверки этого свойства демонстрируется тем фактом, что керамогранит часто используется в напольных покрытиях снаружи или на фасадах зданий, где материал подвергается воздействию солнечного света в течение продолжительных периодов времени. Керамогранит, как правило, устойчив, особенно керамогранит производства Eiffelgres, который прошел все испытания на способность сохранять неизменным цвет плитки.
ДАТЧИК
В процессе обжига керамогранит уменьшается в размерах до такой степени, которая зависит от температуры печи.Таким образом, может случиться так, что плитки одного и того же изделия, обожженные в разных циклах, подвергаются воздействию температур, которые не являются полностью идентичными, что приводит к линейной усадке и, следовательно, к конечным размерам. Эти плитки не будут точно одинакового размера: они будут иметь разную толщину, другой размер, хотя и в ограниченной степени. Eiffelgres поддерживает процесс закупок своих клиентов и гарантирует, что плитки упакованы в партии однородной толщины, чтобы исключить риск укладки материалов разных размеров на одном и том же участке.
«Номинальные» размеры, указанные на упаковке, — это размеры, используемые для обозначения продукта (например: 60×60), «производственные» размеры, то есть «калибр» (например, 59,5×59,5) или заранее определенное производство.