Линия сборки автомобиля
Все мы сегодня пользуемся технически сложными вещами, но не каждый задумывается о процессе, предшествующем полученному результату. Например, современный легковой автомобиль содержит внутри себя около 20 тысяч деталей. Многие заводы, которые собирают автомобили, проводят у себя экскурсии, так что каждый желающий может посетить завод и увидеть основные этапы сборки автомобиля своими глазами. За символическую плату Вы можете попасть даже на завод BMW.
Для тех, у кого все-таки нет возможности увидеть все своими глазами, рассмотрим основные этапы сборки автомобиля.
Процесс производства автомобиля начинается с цеха штамповки, или прессовочного цеха.
Сюда поступают заготовленные стальные листы, которые проходят штамповку, гибку, пробивание отверстий, в результате чего каждая кузовная панель получает свой финальный вид.
Следом за формовкой кузовных деталей – этап сварки. Отштампованные детали поступают в сварочный цех, где на автоматизированной линии соединяются части днища автомобиля, боковые части кузова, а затем и крыша.
На завершающем этапе сварки кузова устанавливаются навесные детали: крылья, капот и багажник, двери.
Благодаря современным роботизированным линиям, кузов будущего автомобиля появляется буквально на глазах.
Дальше, уже собранный кузов отправляется на оцинковку и грунтовку. Эти операции необходимы, чтобы защитить автомобиль от коррозии и подготовить его к дальнейшей покраске. Также на данном этапе устанавливаются шумоизоляционные маты, на днище автомобиля наносится антигравийное покрытие для защиты кузова от сколов.
В покрасочном цехе роботами окрашиваются внешние детали кузова, наносится лак для обеспечения привлекательного вида и блеска, после чего кузов помещают в печь для сушки лакокрасочного покрытия. На финальной стадии поверхность кузова обрабатывается воском для защиты от внешних воздействий и для защиты скрытых полостей кузова от коррозии.
Следующий этап самый ответственный – сборка автомобиля. Почти все операции здесь выполняются вручную. Роботов используют на начальном этапе только для установки тяжелых агрегатов.
Сборка проводится в следующем порядке:
- Устанавливается двигатель и навесное оборудование
- Собирается подвеска и механизм рулевого управления
- Устанавливаются электропроводка, ремни безопасности, подушки безопасности, система ABS;
- монтируются элементы интерьера (ковровое покрытие, сидения, панель, задняя полка) и экстерьера.
После того, как сборка автомобиля завершена, перед тем как автомобиль попадет к покупателю, каждый автомобиль проходит тестирование. Проверяется внешний вид автомобиля, качество установки навесных деталей, качество лакокрасочного покрытия. Также обязательно проводится функциональная часть: корректируются углы развала схождения колес, на стенде проверяют эксплуатационные характеристики двигателя. Тестируются трансмиссия, система ABS, ходовая часть автомобиля и все электронные системы и приборы автомобиля. Только после этого завод транспортирует готовый автомобиль в дилерский центр, где его будет дожидаться счастливый покупатель.
Понравилась статья?
Автомобили российской сборки обзор моделей 2020-2021 года Москва
Россия – один из крупнейших производителей автомобилей в Европе. Ежегодно с конвейеров многочисленных заводов
сходят десятки тысяч транспортных средств всех сортов – от бюджетных малолитражек до больших люксовых
внедорожников. И речь идет не только об автомобилях российских марок. Последние годы автопроизводители со всего
мира стремятся усилить свое влияние на отечественном рынке, для чего открывают в России все новые заводы и
сборочные линии.

- Тип транспортного средства: малолитражный хэтчбек, семейный седан, модный кроссовер, проходимый внедорожник, практичный универсал — в России собирают всё! Есть даже такие гораздо более редкие модели, как фургон, спортивный хэтчбек или универсал повышенной проходимости. Так что определитесь, для каких нужд в первую очередь вам нужен автомобиль и, исходя из этого, выберите его тип.
- Двигатель: среди автомобилей российской сборки есть как обладатели скромных моторов объемом 1.3-1.4 литра и мощностью менее 100 л.с., так и гордые владельцы силовых агрегатов объемом по 2 литра и больше, выдающие уже под 200 л.с. Первые обеспечивают высокую топливную экономичность (до 5 литров бензина на 100 км пути в загородном цикле), вторые – высокую скорость и тяговитость. Если вы посматриваете на внедорожные модели с полным приводом, стоит также обратить внимание на показатели крутящего момента. Именно момент влияет на то, насколько хорошо автомобиль будет справляться с бездорожьем при езде на низких скоростях.
- Комплектация: самые хорошо укомплектованные бюджетные модели российской сборки – это, как правило, автомобили китайских марок. Зато европейцы, японцы и корейцы отличаются более продвинутыми и современными решениями. Но и стоят они при этом, конечно же, дороже. Оптимальным соотношением богатой комплектации и разумной цены можно назвать последние модели главной российской марки LADA. Такие автомобили, как VESTA и XRAY, получили оснащение на уровне лучших иностранных образцов, но при этом сохранили вполне конкурентные цены.
- Безопасность: покупая автомобиль в XXI веке, ни в коем случае не стоит обходить стороной вопрос защиты пассажиров. Желательно, чтобы на борту машины были хотя бы три базовых системы пассивной и активной безопасности: фронтальные подушки безопасности для водителя и переднего пассажира, антиблокировочная тормозная система (ABS) и система электронного распределения тормозного усилия (EBD).
Ну а чем больше подобных технологий реализовано на борту автомобиля, тем лучше. Просматривая комплектацию модели, обратите внимание на наличие таких аббревиатур, как ESS, BAS, ESC, VSM, ESP, AFU, TPMS.
- Уровень адаптации к российским климатическим и дорожным условиям: все отечественные модели, разумеется, ещё на стадии проектирования были подготовлены к испытаниям российскими дорогами и погодной. Но это далеко не исключение. В наши дни многие иностранные производители не скупятся на адаптацию своих автомобилей для российского рынка. У одних она больше и продуманнее, у других — меньше. Например, очень популярная в нашей стране корейская модель KIA RIO получила увеличенный дорожный просвет в 160 мм и пластиковую защиту картера, аккумулятор увеличенной ёмкости (48Ач), отопительную систему увеличенной мощности (4650 кКал), обработку кузова и днища антикоррозионным покрытием, а также обработку радиатора материалом, защищающим от агрессивной внешней среды.
Приобретая автомобиль российской сборки в салоне официального дилера «РИА АВТО», вы получаете машину с идеальным соотношением цены и качества, ведь налаженное на территории нашей страны производство позволяет компаниям сэкономить на транспортировке готовой продукции. К тому же «российская прописка» транспортного средства гарантирует постоянное наличие качественных оригинальных запчастей. И, наконец, абсолютное большинство подобных моделей проходит дополнительную адаптацию для эксплуатации на территории нашей страны.
Сборка машин в России разоряет европейские автоконцерны :: Autonews
Россия в очередной раз подтвердила свой статус необоснованно дорогой страны: как выяснилось, не только посещение ресторанов, покупка недвижимости и путешествия обходятся здесь дороже, чем в Европе и Азии, – касается это и сборки автомобилей.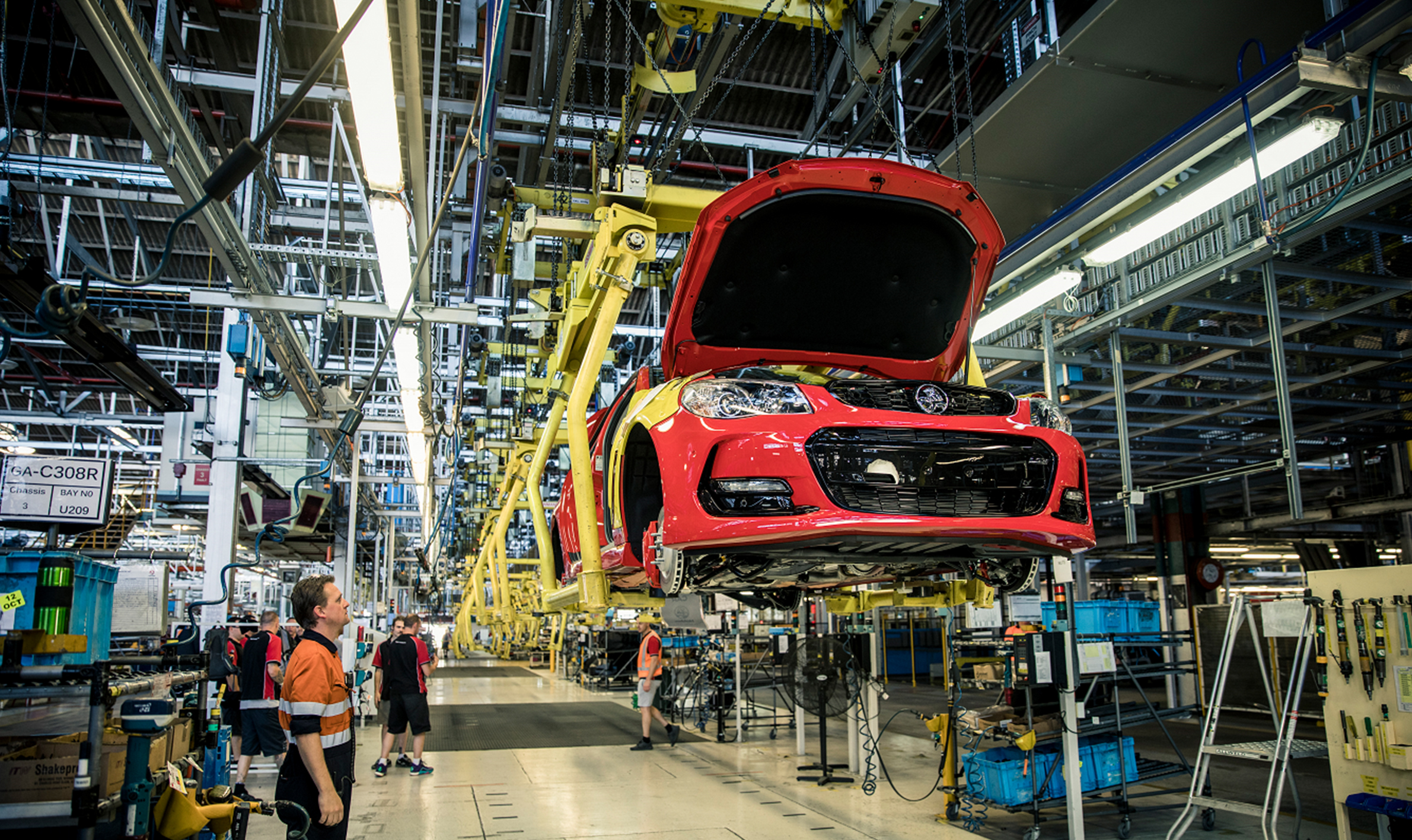
Выступая на форуме «Автоэволюция», он заметил, что французская и японская стороны не ожидали, что их ждут столь значительные издержки. По словам Альтона, сборка автомобилей в нашей стране обходится на 5% дороже, чем в Старом Свете и в Бразилии, и на 15% дороже, чем в Южной Корее и Китае. При этом он развеял миф о дешевизне рабочей силы в России: если оклады действительно не назвать слишком высокими, то затраты, сопряженные с выполнением условий Трудового кодекса, поражают даже привыкших к дороговизне европейцев.
Альтон при этом отметил, что единственное, на чем удается сэкономить, так это на стоимости газа: «Если тарифы на газ в России действительно невысоки, то электричество оказалось довольно дорогим». Что характерно, компания PSMA – не единственный представитель западного автомира, которого неприятно удивила стоимость производства автомобилей в нашей стране.
Недовольны таким положением дел и в Volkswagen – там отмечают, что комплектующие, произведенные в России, обходятся концерну VAG дороже, чем те, что производятся в любой стране Европы. А эксперты уверены, что виной тому – огромный процент брака.
Однако ни PSMA, ни Volkswagen уходить с российского рынка не собираются. Напротив, первые на данный момент ищут новых партнеров для расширения производственных мощностей. Французы и японцы не исключают возможности совместной работы с российскими автомобильными компаниями. «Мы рассматриваем любые возможные варианты сотрудничества с различными российскими автопроизводителями», – в частности, сообщил Дидье Альтон.
Напомним, что в 2010 году PSA Peugeot Сitroen и Mitsubishi открыли в Калуге завод по сборке автомобилей. За прошлый год предприятие выпустило 26 тысяч автомобилей. Почти две трети в общем объеме производства калужского завода пришлись на хэтчбек Peugeot 308 (17 тысяч машин). Было также выпущено около 4700 машин Сitroen C4, производство которых стартовало в июле прошлого года. А в сентябре 2010-го на заводе начался выпуск кроссоверов Peugeot 4007, Citroen С-Crosser и Mitsubishi Outlander.
Между тем растет не только число произведенных в России «иномарок», но и количество автомобилей, ввезенных из-за рубежа. Согласно данным Федеральной таможенной службы (ФТС), за 10 месяцев 2011 года в страну «въехали» 799 тысяч машин – таким образом, импорт по сравнению с периодом за январь-октябрь прошлого года увеличился в 1,5 раза.
Александр Кузьмин
Как собирают качественные автомобили — качество сборки машин
Расскажем как происходит сборка автомобилей на примере японского завода, где собирают качественные машины. Сравним качество сборки, почему авто, собранные за границей качественней машин нашей сборки.
Как собирают машины за границей
На заводе по сборке машин марки Lexus работают свыше 1000 человек — 10 процентов из них вовлечены в работу над увеличением качества сборки. Т.е. каждый десятый работник следит за качеством собираемых машин, чтобы находилось на максимальном уровне.
Тест перед работой
Перед началом рабочего дня на японском заводе, мастера, которые проверяют качество, должны пройти мини тест. Его суть в контроле качества — определение допустимого размера щелей кузовных деталей или минимального размера царапин на кузове. Тест работники проходят каждый день, и задачи меняются.
Если прошёл на отлично, то работник завода отправляется на ответственный участок, если хорошо — к менее ответственным работам. Те, кто «провалил» тест — могут отстранить от работы.
Не всегда человек находится в отличном здравии, случаются физические или психологические причины, по которым не может в данный день работать. Полностью отсекается человеческий фактор, что позволяет повысить качество собираемых машин и не допускать ошибок.
Ошибки на производстве
На участке сборки авто существует шнур-андон. Если работник заметил неисправность при сборке или дефект, то нужно дёрнуть за шнур и производство остановиться до исправления ошибки.
Японские сборщики автомобилей за день применяют шнур-андон для остановки производства более ста раз. И гордятся этим фактом. Ведь, чем больше раз остановлено производство, тем меньше брака в конечной стадии. Теперь, мысленно, сравните данный процесс с производством на российских заводах, где бояться показать число ошибок и дефектов при сборке или скрывают.
Для примера на автосборочном заводе Haval в Китае переняли опыт с применением шнура-андона. В отличие от японцев, там разрешено дергать за шнур только мастерам и при крайней необходимости. Поэтому теряется смысл в применении шнура-андона и количество брака больше.
Что такое кайзен и такуми
Ещё одна замечательная методика повышения качества сборки авто от японцев — принцип кайзен. Абсолютно любой работник завода может улучшить качество производства. Кому как не простым работникам, известно, что удобно или нет. Если замечают, что можно улучшить производство, например, сделав удобное крепление для инструмента и сократив время сборки, то доработки внедрят в рабочий процесс. Наверное, за это сотрудники получают премию.
Самое главное, что обеспечивает качество сборки на японских заводах — такуми — профессиональные работники завода с большим опытом работы. Они проходят серьёзный отбор. В «такуми» посвящают 2-3 человек в год. Именно профессионалы отвечают за самые сложные моменты сборки автомобилей и повышения качества собираемых машин.
Если сравнить методику сборки автомобилей за границей и как собирают наши машины — две большие разницы. Качество сборки зависит не от передовых решений на заводе и высокотехнологичного оборудования, а от простых людей. Это относится и к отвёрточной сборке SKD.
BMW сократит модельный ряд российской сборки
Компания BMW отказывается от производства пяти моделей на калининградском заводе «Автотор» из-за экономической нецелесообразности. В результате предприятие будет выпускать в 2021 году лишь три модели BMW, а общий объем составит примерно 12 тыс. машин, сообщил председатель совета директоров «Автотор Холдинг».
По данным издания «Авторевю», уже в апреле на конвейере «Автотора» останутся только большие кроссоверы BMW X5, X6 и X7. Все остальные модели будут полностью переведены на импорт – это седаны 5-й и 7-й серий, а также кроссоверы X1, X3 и X4. Более того, даже для семейства X5/X6/X7 зарезервирована возможность поставки любой из версий напрямую с американского завода, то есть впоследствии BMW может полностью свернуть российскую сборку.
Таким образом, автомобили BMW скоро могут заметно подорожать – если, конечно, российское представительство не договорится со штаб-квартирой о выгодных закупочных ценах на машины в фиксированных комплектациях, как это было с калининградскими автомобилями. А ведь именно выгодные цены на машины местной сборки и их доступность на дилерских складах позволили BMW в последние два года удерживать лидерство по объему продаж в российском премиум-сегменте. На локализованные автомобили приходилась почти половина продаж марки BMW в нашей стране.
Между тем, еще не так давно компания BMW вынашивала планы строительства собственного завода в России, но специнвестконтракт, переданный на рассмотрение в Минпромторг, так и не был подписан. Стороны не сошлись в условиях работы, после чего в компании BMW полностью исключили возможность строительства локального завода. Участвовать в СПИКе, который заключил «Автотор», баварский концерн тоже не стал.
Все эти годы автомобили BMW выпускали на «Автоторе» по технологиям SKD (крупноузловая сборка) и MKD (мелкоузловая сборка). Максимальный уровень локализации, на который могут пойти в BMW, – это сварка и окраска кузовов (CKD), но для выгодной работы по СПИКу этого недостаточно. Правительство заинтересовано еще и в локализации компонентов, а с тем объемом продаж, который есть у BMW (около 40 тыс. автомобилей в год), производство комплектующих в России экономически нецелесообразно: как уверяют в компании, себестоимость автомобилей от этого только вырастет, да и производителям компонентов такие объемы выпуска неинтересны.
Какие еще модели BMW и по какой цене официально представлены на российском рынке, подскажет каталог «Цена Авто».
Фото: BMW
Toyota остановила сборку автомобилей на половине производственных линий в Японии
Землетрясение, случившееся на северо-востоке Японии в выходные, продолжает сказываться на местной промышленности. Крупнейший автопроизводитель страны, Toyota Motor, в качестве меры предосторожности приостановил работу половины сборочных линий в Японии, рассчитывая вернуть их в строй на следующей неделе. Утверждается, что к дефициту чипов это решение отношения не имеет.
Источник изображения: Nikkei Asian Review
Как отмечает Nikkei Asian Review, на девяти предприятиях Toyota Motor и её дочерних компаний в Японии после землетрясения были остановлены 14 из 28 сборочных линий. Они выпускают широкий ассортимент транспортных средств, от грузовиков до кроссоверов и люксовых моделей Lexus. По независимым оценкам, остановка конвейера вынудит Toyota сократить программу выпуска автомобилей на пять или шесть тысяч машин ежедневно. Подчёркивается, что собственные предприятия Toyota не пострадали, но остановка производства может быть связана с деятельностью поставщиков. С другой стороны, источники призывают не искать причины остановки конвейера среди проблем с поставками полупроводниковых компонентов.
Прочие автопроизводители Японии останавливать сборку машин на местных предприятиях не собираются. В 2011 году многие из них были вынуждены приостановить работу из-за проблем с поставками компонентов Renesas. Сама Toyota тогда не могла возобновить выпуск автомобилей в полном объёме на протяжении целого месяца. На этот раз Renesas Electronics ограничилась приостановкой производства компонентов на несколько дней. Вчера она объявила о возобновлении работы предприятия, находящегося ближе всего к эпицентру субботнего землетрясения. Поставки готовой продукции начались ещё в понедельник, а на полное восстановление объёмов производства уйдёт не больше недели. Землетрясение 2011 года навредило бизнесу Renesas гораздо сильнее, тогда на восстановление объёмов производства ушло три месяца, а на пополнение складских запасов потребовалось полгода.
Если вы заметили ошибку — выделите ее мышью и нажмите CTRL+ENTER.
«Cвадьба» при сборке автомобилей Lada будет проходить в автоматизированном режиме
- Главная / Бизнес
20.01.2021
Отечественный автогигант «АвтоВАЗ» автоматизировал процесс стыковки двигателя и шасси с кузовом при производстве автомобилей на платформе B0.
На тольяттинском предприятии, как сообщает его пресс-служба, в настоящее время продолжается модернизация технических процессов с целью повышения эффективности производства.
Бизнес / Новости
В частности, как отмечают на «АвтоВАЗе», в январе нынешнего года в эксплуатацию были введены новый цех подсборки шасси с силовым агрегатом и полуавтоматическая линия по установке двигателя и шасси на производстве автомобилей на платформе B0.
Цех подсборки шасси с силовым агрегатом представляет собой напольный конвейер со специальной модульной оснасткой, на которой происходит компоновка основных элементов – это силовой агрегат, подрамник, узлы шасси. Указанная оснастка – универсальная и может быть использована для работы с различными моделями автомобилей.
«Рядом с линией компоновки модулей шасси с силовым агрегатом организованы участки сбора кит-комплектов, сформированы прямые логистические потоки для поставки необходимых комплектующих из различных производств», – отмечается в официальном сообщении «АвтоВАЗа». В работе цеха используются роботизированные тележки автоматической доставки.
Готовый к установке модуль с двигателем и шасси поступает по автоматическим транспортным линиям на участок стыковки с кузовом автомобиля (именно этот процесс называют «свадьбой»).
Новая технология, как заявляет производитель, позволила минимизировать использование ручного труда: операторы задают направление и запускают процесс фиксации двигателя, шасси и кузова нажатием клавиши. Сборка машин на новом оборудовании осуществляется «с высоким качеством и в строгом соответствии с производственным ритмом».
«Движок» теперь в Telegram! Подписывайтесь и узнавайте первыми о новинках и результатах тестов!950
Полное руководство по линиям производства автомобилей — детали, изготовленные на заказ, кованые, литые и плакированные — Bunty LLC
Сборочная линия — одно из величайших изобретений 20-го века. Часто упоминаемый в числе первых подрывных практик, он настолько потряс мир, что производители, не сумевшие к нему приспособиться, закрыли свой бизнес.
Сборочная линия была больше, чем просто изобретением, которое ускорило производственные процессы — это была идея, методология, направленная на повышение эффективности и производительности.Практически каждая отрасль быстро приняла и адаптировала ее в соответствии со своими потребностями, и она продолжает развиваться и процветать по сей день.
Сегодня наиболее широко используемый термин среди производителей — это бережливое производство — сборочная линия, на которой работает оптимально, без задержек и проблем, с минимальными отходами и максимальной производительностью. Сегодня эти объекты являются целью любого бизнеса, а не только производственного.
Первая часть этого руководства описывает сборочную линию от ее скромного начала и первых прототипов, главного прорыва Генри Форда, до вклада Toyota в сборочную линию и бережливое производство.Затем руководство переходит к современным тенденциям, их организационному аспекту, новым технологиям, интеграции ИИ и машинного обучения, а также другим разрушительным методам, которые штурмом захватывают мир.
Сегодня мы видим, что каждый бизнес принял организационные методы, используемые современными сборочными линиями.
Они применимы практически к любой существующей компании, и даже к нашей личной повседневной организации задач.
Для того, чтобы компания действительно преуспела в современном быстро меняющемся мире, она должна работать безупречно — с минимальными отходами и максимальной эффективностью.
Вот как сборочные линии сделали это возможным.
История линий по производству автомобилейКогда в разговоре упоминается термин «производство автомобилей», большинство людей сразу же думают о Генри Форде и его революционных сборочных линиях, но на самом деле все гораздо сложнее. Во-первых, сборочная линия была запатентована не Фордом, а другим гигантом автомобильной промышленности, которому приписывают создание современной автомобильной промышленности в том виде, в каком мы ее знаем, но не нарицательным.
В этой главе мы перечислим, как появились линии по производству автомобилей, какими мы их знаем, и как к ним привело постоянное стремление к эффективности и повышению качества продукции в различных отраслях. В этой главе будет рассмотрена их история, а важность разделения труда, взаимозаменяемые части и аналогичные концепции из других отраслей сыграли важную роль в их развитии.
Отделение труда
Эффективные и рентабельные линии по производству автомобилей также обязаны своим существованием древней социальной концепции: разделению труда.На протяжении всей истории концепция разделения труда изучалась, анализировалась и применялась во многих отраслях, начиная с Шумерской империи около 3000 г. до н. Э. В модели разделения труда каждый работник выполняет одну задачу, которая со временем становится его второй натурой. Конструкция отдельных частей единообразна, что способствует повышению эффективности и сокращению общих производственных затрат.
Ранние сторонники разделения труда, однако, также осознавали его подводные камни, наиболее значительными из которых являются снижение удовлетворенности работников в долгосрочной перспективе и меньшие возможности для продвижения по службе. Тем не менее, разделение труда не обязательно по способностям или навыкам, а с упором на одну задачу для каждого рабочего, нашло свое применение во всех отраслях, от судостроения до общего производства и производства автомобилей.
Теоретики разделения труда
Одним из первых теоретиков, взявших курс на разделение труда, был Платон , который постулировал в своей «Республике», что «неравенство человечества… воплощается в разделении труда». Греческий философ, как и многие теоретики, которые пойдут по его стопам, рекламировал бесчисленные преимущества разделения труда как на политическом, так и на экономическом уровне.
Например, ученый и философ 17-го века сэр Уильям Петти наблюдал, как разделение труда привело к повышению производительности голландских судостроительных верфей. Петти с радикальными идеями, которые предшествовали промышленной революции примерно на 100 лет, считается первым современным философом, который предположил, что разделение труда имеет многочисленные социальные преимущества. В своей книге «Политическая арифметика» Петти из первых рук изложил свои наблюдения о разделении труда в судостроительной отрасли.По словам Петти, изначально голландцы строили свои корабли по одному, что считалось долгим и кропотливым процессом. Петти заметил, что, когда труд был разделен таким образом, что определенные рабочие выполняли определенную задачу на каждом построенном корабле, процесс занимал меньше времени.
Десять лет спустя экономист Адам Смит развил идеи Петти, продвигая идею о том, что разделение труда равносильно экономической зависимости страны. Его публикация 1776 года «Богатство народов» сегодня считается одной из самых влиятельных книг по экономической науке.Некоторые идеи Смита в то время считались радикальными и новаторскими, в том числе идея о том, что выбранный человеком вид работы вызван разделением труда и способствует ему. Он подчеркнул важность сочетания навыков с оборудованием для повышения производительности и экономического процветания.
Идеи Смита были квалифицированы и расширены более века спустя французским социологом Эмилем Дюркгеймом , автором книги 1893 года «Разделение труда в обществе».
Благодаря вкладам первых ученых, таких как Дюркгейм, Петти и Смит, а также пионеров в судостроении, разделение труда стало самой эффективной производственной системой в мире.
Ранние концепции в других отраслях промышленности
В годы, предшествовавшие промышленной революции, общество действительно функционировало так же, как то, что предлагал Платон: будь то сапожники, строители или ткачи, один человек создавал единичный предмет на каждом этапе своего пути. Источник «торговли», этот метод производства требовал значительных навыков, на освоение которых могли уйти годы. Кроме того, для овладения определенным ремеслом может потребоваться целая жизнь тренировок и практики. Сегодня ремесленное производство — это специализированная отрасль, стоимость которой многие производители считают непомерно высокой.
Самое раннее свидетельство использования производственной линии и массового производства взаимозаменяемых компонентов относится к году в 12 веке Китай . Многие государственные монополии страны заказывали и осуществляли массовое производство различных металлических компонентов.
Европа приняла массовое производство еще в 1104 году в водном городке Венеции, Италия. В том же году началось строительство крупнейшего промышленного комплекса на континенте: The Venetian Arsenal .Конгломерат оружейных складов и верфей, Арсенал в конечном итоге охватил 15 процентов Венеции по площади, в общей сложности 110 акров, и нанял более 16 000 рабочих. За столетия до того, как Генри Форд усовершенствовал движущуюся сборочную линию, Венецианский арсенал предложил такую возможность, но на каналах, а не на механических ремнях — детали производились массово и устанавливались на корабли, когда они плыли по каналу. На пике производства, в середине 1500-х годов, весь корабль можно было собрать за один день.
Промышленная революция
По мнению многих теоретиков, капитализм в том виде, в каком мы его знаем, родился в результате промышленной революции. Промышленная революция, обозначенная как период между 1760 и 1840 годами, привела к тому, что «инновационные» изобретения и достижения в производстве распространились со скоростью лесного пожара. Разделение труда было основным компонентом промышленной революции, способствуя прорыву в методах производства, в том числе в процессах сборочных конвейеров и погрузочно-разгрузочных работах, во множестве отраслей, которые требовали модернизации.
Наиболее важные концепции производственных линий во время промышленной революции
Поскольку мукомольная промышленность играла важную роль в обеспечении питания населения, она была в авангарде механических и производственных инноваций во время промышленной революции. Многие эксперты считают, что современные методы обработки сыпучих материалов были созданы Оливером Эвансом, который автоматизировал мукомольный завод.
- Оливер Эванс и его автоматическая мукомольная мельница — Первый автоматизированный процесс сыпучих материалов.
- В 1700-х годах помол муки был трудоемким и длительным процессом с множеством этапов, включая измельчение и просеивание.
- Эванс, работая на заводе своей семьи в Ньюпорте, штат Делавэр, отметил, что весь процесс, помимо того, что он длительный, часто приводил к получению некачественного продукта.
- После открытия мельницы в 1785 году Эванс искал альтернативы.
- В отличие от большинства производителей того времени, мыслитель-новатор рассматривал производственный процесс как непрерывное целое.
- Он считается одним из первых, кто рассматривает производственный процесс как нечто большее, чем просто сумму его отдельных частей.
- На своей семейной мельнице Эванс использовал древнеримскую ленточную ковшовую систему вместе с брезентовыми конвейерами для транспортировки муки и автоматизации процесса.
- Его методы были приняты на ряде пивоваренных заводов и заводов как в колониальных США, так и в Великобритании.
- The Portsmouth Block Mills, Хэмпшир, Англия — Самый ранний промышленный пример непрерывного линейного процесса сборки.
- Построенный с 1801 по 1803 год, завод в основном производил детали для Королевского флота.
- Всего в Портсмуте было изготовлено 22 различных типа станков, которые оставались открытыми до 1960-х годов.
- Bridgewater Foundry, England — Современные фабрики по-прежнему устроены таким же образом.
- Литейный завод специализировался на производстве локомотивов и станков, и его здание было построено в линию с отдельными участками для погрузочно-разгрузочных работ и производства.
- Рабочие использовали краны для подъема тяжелых материалов и предметов, а железная дорога, соединенная напрямую с фабрикой, обеспечивала удобство транспортировки.
- Завод Leiston Works — Самая первая поточная сборочная линия.
- Еще до того, как возникла идея о личных автомобилях, транспортная отрасль была лидером в обрабатывающей промышленности.
- Первая поточная сборочная линия использовалась на заводе Leiston Works Factory, который строил портативные паровые двигатели, начиная с 1840-х годов: в 1852 году производство паровых двигателей началось в «Длинном цехе», названном из-за его формы.
- Машиностроение начиналось на одном конце длинного помещения, и части были прикреплены по мере того, как он «продвигался» по комнате.
- Некоторые детали были построены на уровне балкона завода, а затем опущены на двигатель.
- К тому времени, как паровой двигатель прошел через всю комнату, он был готов.
В то время как промышленная революция принесла огромные изменения в обрабатывающую промышленность и произвела первые версии сборочной линии, впереди было еще больше. Взаимозаменяемые (или предварительно изготовленные) детали еще больше изменят производственную отрасль к лучшему.
Взаимозаменяемые детали: огромный прорыв
Немногие могут отрицать превосходное мастерство изготовления индивидуального изделия, будь то пара кожаных ботинок или привлекательный автомобиль. Однако изготовление на заказ — это трудоемкий процесс; тот, который может негативно повлиять на эффективность и прибыль компании. Благодаря использованию сменных деталей в производстве различных товаров, от оружия до автомобилей, массовое производство становится реальностью.Кроме того, заменить или отремонтировать предмет намного проще.
Система Грибоваля
Хотя использование сменных деталей в производстве является обычным явлением в современном мире, это был настоящий прорыв, который восходит к Франции 18 века. Оружие было первыми предметами массового производства, построенными из взаимозаменяемых частей, начиная с пушек и снарядов.
Французский инженер и офицер артиллерии генерал-лейтенант Жан-Батист Вакет де Грибоуаль приписывают содействие повсеместному внедрению стандартизированного оружия, называемого системой Грибоуаль.Система изменила процесс сверления при производстве пушек, используя стандартизированную систему сверления, которая позволила сделать стенки более тонкими и уменьшить общую длину без ущерба для дальности и точности.
Реализованная по королевскому приказу в 1765 году система тезки Грибоваля была расширена его соотечественником и покровителем Оноре Бланом. Конструктор огнестрельного оружия считал, что систему Грибоваля можно использовать в производстве мушкетов. Хотя идея Бланка провалилась во Франции в то время, серийные ружья сыграли важную роль в обеспечении французских побед в наполеоновских войнах, которые велись с 1803 по 1815 годы. Ни Грибоваль, ни Блан, умершие в 1789 и 1801 годах соответственно, не дожили до того, чтобы их концепция стала широко распространенной реальностью в их родной стране.
Производство стандартного оружия Эли Уитни
По другую сторону Атлантики идеи Блана привлекли внимание тогдашнего посла во Франции Томаса Джефферсона. После нескольких лет прислушивания к предложениям Джефферсона относительно стандартизированного производства оружия новое правительство США одобрило испытание этой идеи.Сам президент Джордж Вашингтон наградил изобретателя Эли Уитни грантом на производство 12 000 предварительно изготовленных мушкетов.
Уитни, прославившаяся в 1794 году как изобретатель хлопкоочистительной машины, не успела уложиться в срок, установленный Конгрессом. Они приказали Уитни явиться на сборку, на которой он успешно продемонстрировал, как взаимозаменяемые детали могут произвести революцию в оружейной промышленности. До широкого использования сменных частей сломанное огнестрельное оружие должно было ремонтироваться оружейным мастером на индивидуальной основе.Готовые детали упростили процесс ремонта оружия, навсегда изменив отрасль.
Рэнсом Эли Олдс: отец концепции сборочной линии
На рубеже 20-го века личные автомобили только начинали завоевывать мир, соединяя его так, как это было раньше невозможно. И прорывы в методах производства на конвейере сыграли важную роль в этой игре. Несмотря на распространенное заблуждение, что Генри Форд был мозгом сборочной линии, на самом деле это был один из конкурентов Форда, который изобрел и запатентовал «инновационный» метод производства — Ransom Olds .
Olds Motor Vehicle Company там, где все начиналось
Олдс, производитель автомобилей из Детройта, основал компанию, которая носит его имя по сей день, — Oldsmobile, — которой приписывают начало правления Детройта как автомобильной столицы мира. На момент основания в 1901 году компания Olds была известна как Olds Motor Vehicle Company. С самого начала завод Oldsmobile использовал конвейер в качестве основного средства производства.
Концепция сразу же имела успех: за первый год работы завода с конвейера сошло 425 автомобилей.В следующем, 1902 году, было произведено 2500 автомобилей Olds Motor Company.
Рэнсом сделал еще один шаг вперед в своем «инновационном» видении производства, внедрив модель массового производства, которая изменила производственный ландшафт как самого Детройта, так и автомобильной промышленности в целом. Как и первые производители оружия, первые производители автомобилей изначально создавали автомобили индивидуально, без стандартного шаблона. Таким образом, каждый автомобиль отличался от других. Французский Benz Velo был первым стандартизированным автомобилем: в течение 1894 года выпуска было выпущено 134 идентичных автомобиля.
Модель 1901 года Oldsmobile Curved Dash вошла в историю как первый серийный автомобиль в США. К 1904 году было продано около 5000 моделей Curved Dash.
Генри Форд усовершенствовал сборочную линию
Несмотря на успех Рэнсома Олдса и его одноименной компании, именно Генри Форд оставил свое имя на протяжении всей истории как виртуальный отец автомобильной промышленности. Движущаяся сборочная линия Ford произвела революцию в автомобильном производстве и внесла свой вклад в улучшение условий труда в 20 веке.
Ford получил идею от пищевой промышленности
Идея движущейся сборочной линии родилась после посещения Фордом скотобойни Swift & Company в Чикаго. Это событие даже задокументировано в музее Генри Форда: находясь на мясокомбинате, Форд восхищался конвейерной системой компании, по которой мясо доставлялось к рабочим. Впоследствии Форд спроектировал и построил аналогичную сборочную линию с движущимися платформами и приводными конвейерными лентами на своем заводе в Хайленд-Парке.На мясокомбинате Swift & Co Форд также воочию убедился в преимуществах разделения труда. Рабочим были поручены специализированные задания, что обеспечило высокую эффективность рабочих мест.
Первый автомобиль Moving Assembly Line: Ford Model T
После посещения бойни Форд собрал команду для разработки движущейся сборочной линии для автомобильной промышленности. Группа опытных экспертов, в том числе инструментальщик К. Гарольд Уиллис и начальник завода Питер Э.Мартин адаптировал концепцию девятого воплощения Ford Model T. После длительного периода проб и ошибок, 1 октября 1908 года, первая Model T, собранная за 93 минуты, сошла с конвейера в Детройте. До внедрения движущейся конвейерной ленты среднее время производства Ford Model T составляло около 12 часов.
Полная модель T состояла из более чем 3000 деталей, от шин до клапанов и бензобаков, которые стали унифицированными начиная с 1913 года.Быстрый и организованный производственный процесс был разбит на 84 этапа: один рабочий выполнял одну и ту же задачу для каждого автомобиля. Рабочие сборочного конвейера были специально обучены, чтобы стать виртуальными экспертами в этой единственной конкретной задаче, выполняемой с трехминутными интервалами.
За счет сочетания взаимозаменяемых деталей, движущейся сборочной линии и особенно подготовленных рабочих время, необходимое для сборки транспортного средства, значительно сократилось. Меньшее количество рабочей силы привело к снижению общих производственных затрат, а экономия была передана клиентам Ford.При цене менее 300 долларов , что значительно меньше, чем в прошлом году 850 долларов (около 18 000 долларов в сегодняшней стоимости), Ford Model T принес в массы личные автомобили . Впервые средний класс в целом мог позволить себе качественный личный автомобиль.
Через год после запуска движущейся сборочной линии Ford значительно превзошел по объему производства всех остальных автопроизводителей. В 1914 году с заводов Ford сошло чуть более 308 000 автомобилей. А к 1927 году во всем мире было продано более 15 миллионов автомобилей Ford модели T.
Условия труда улучшены благодаря производственным линиям
Несколько неожиданных, но желанных побочных эффектов движущейся сборочной линии были более безопасные фабрики, более короткая рабочая неделя и улучшенные условия труда. Поскольку у рабочих были унифицированные, статические задачи и назначенная должность, случаи блуждания рабочих по месту работы были исключены, что снизило уровень травм и при этом удерживало сотрудников на задании.
Повышение заработной платы и гарантированная оплата
Ford также привнес в автомобилестроение человечность и сострадание.Хотя этот акт мог быть жестом доброй воли и щедрости, он также помог улучшить моральный дух сотрудников и снизить текучесть кадров. Улучшения условий труда в компании Ford включали введение 5-долларового рабочего дня, «значительной заработной платы для того времени», с гарантированной оплатой. Повышение заработной платы сопровождалось и другими льготами: рабочим больше не разрешалось поднимать тяжести, наклоняться или останавливаться на работе, и никакой специальной подготовки не требовалось. Эти новые стандарты рабочего места означали, что больше людей могло работать, так как почти любой мог выполнять задачи.Иммигранты также имели право на работу.
Поскольку производство товаров было таким длительным специализированным процессом, первые производители искали способы сэкономить время и повысить эффективность. Без вклада вольнодумцев, таких как Эванс, Олдс и Форд, автомобильная промышленность была бы совсем другим зверьком. Вместо того, чтобы сидеть в тени своих предшественников, современные автомобильные компании смотрят в будущее, постоянно совершенствуя свои методы и привнося совершенно новую динамику в ландшафт автомобильных производственных линий.
С самого начала автомобилестроения движущиеся сборочные линии и их взаимозаменяемые части играли решающую роль. С момента своего появления они создавались, чтобы производить автомобили быстрее и эффективнее, чем ручной труд. Сам их дизайн остается отличительной чертой совместных усилий множества производителей, а не одной компании. Десятки компаний-производителей автомобилей работали вместе, чтобы усовершенствовать конвейер в том виде, в котором мы его знаем сегодня.
Сегодняшние сборочные линии далеки от своих первых аналогов. Те, которые используются сегодня на заводах, отличаются оптимизированной технологией и систематическими методами, которые позволяют минимизировать отходы. Это увеличивает ценность транспортных средств без ущерба для удовлетворенности клиентов или производительности.
Этой эффективности современных сборочных линий можно в значительной степени отдать должное Japan и Toyota Industries , которые сыграли решающую роль в разработке технологии этой сборочной линии и улучшении производственных линий, которые используются до сих пор.Производственная система Toyota рассматривается многими инсайдерами отрасли как предшественник того, что сейчас известно как бережливого производства . Таким образом, и Toyota, и Япония признаны лидерами как в автомобилестроении, так и в производственной отрасли.
Обзор бережливого производства и производственной системы Toyota
Система производства Toyota , известная как TPS , представляет собой интегрированную социально-технологическую систему.Философия и практика управления TPS помогают организовать производство, логистику и взаимодействие с клиентами и поставщиками. TPS является предшественником более общего термина «бережливое производство». Основные цели — устранение чрезмерной нагрузки и несогласованности при минимизации отходов.
TPS стремится минимизировать или исключить восемь различных видов отходов. К ним относятся:
- Перепроизводство или крупные отходы
- Время в наличии или в ожидании
- Транспорт
- Обработка
- Наличие на складе
- Механизм
- Изготовление бракованной продукции
- Недостаточно загруженные рабочие
По самой своей конструкции TPS представляет собой основу для устранения отходов при сохранении всех ресурсов.Это эталон обрабатывающей промышленности, который сейчас копируют во всем мире, прежде всего под маркой бережливого производства.
Как Sakichi Toyoda и автоматизированные ткацкие станки проложили путь к TPS
CC Public domain, через Wikimedia CommonsХотя бережливое производство может идти напрямую в Японию и TPS, кредит за TPS должен быть отдан его изобретателю, Sakichi Toyoda . Тойода родился в 1867 году и был основателем Toyota Industries.Даже после своей смерти в 1930 году Тойода остается известным как король изобретателей, на его имя было выдано 85 патентов. Последние, однако, были сделаны с помощью его родственников, в том числе собственных детей.
Интересно, что он был наиболее активен в области ткацких станков и добился большого прорыва в 1896 году, когда он разработал ткацкий станок, который автоматически прекращал работу в случае обрыва нити . В то время порванная нить представляла серьезную проблему качества в процессе ткачества.Рабочим приходилось постоянно контролировать ткацкие станки на предмет обрыва нитей. Если одна оборванная нить не будет вовремя поймана, это приведет к серьезному дефекту плетения, который повредит всю ткань.
Это был только первый метод, внедренный в производственную систему Toyota. Вот все методы, разработанные Toyota и используемые сегодня в бережливом производстве.
То, что Тойода обнаружил и восстановил порванную нить, положил начало процессу его изобретения системы, в которой машина или производственный процесс останавливался при обнаружении неисправности.Он хотел избавить машину от таких ошибок, для чего решил использовать комплексный подход под названием Jidouka. В переводе с японского это слово означает автоматизация. Тем не менее, Toyoda внесла небольшие изменения в свой написание, что позволило перевести его как autonomation — автоматизация с человеческим участием .
Подход компании Toyoda «Пять причин»В своем изобретении TPS Тойода использовал то, что он назвал принципом «пять почему» , который является неотъемлемой частью TPS и является одной из его основ.Подход «пять почему» потребовал от Toyoda спросить «почему?» пять раз при возникновении проблемы с системой. Спросив пять «почему», он смог найти корень проблемы, а не просто устранить и устранить симптомы неисправности.
Ткацкий станок, приведший к первому сборочному конвейеруОдно из величайших достижений Тойоды произошло в 1925 году, когда он изобрел ткацкий станок Model G . Ткацкий станок работал полностью сам по себе и вообще не требовал вмешательства человека или наблюдения.Операторам приходилось лишь изредка пополнять свои челноки пряжей для автоматического устройства смены челноков. Это был самый совершенный ткацкий станок в мире: он значительно улучшил качество и производство ткани. Благодаря его изобретению один неквалифицированный рабочий мог контролировать от 30 до 50 отдельных ткацких станков. Спрос на эти автоматизированные ткацкие станки резко вырос во всем мире, и Тойода построил свою первую сборочную линию в 1927 году, чтобы удовлетворить спрос на эти станки. Ткацкие станки автоматически перемещались от станции к станции на сборочных линиях, используемых для их создания.В 1929 году он продал патент на автоматический ткацкий станок британской компании Platt Brothers. Интересно, что продажа патента на ткацкий станок дала начальный капитал для развития автомобильной компании.
Подход JIT и основание Toyota Motor CompanyВскоре после продажи патента на свой автоматизированный ткацкий станок Тойода начал производство автомобилей в 1933 году как отдельное специализированное подразделение своего завода по производству автоматических ткацких станков Toyoda. Производство автомобилей на заводе возглавил сын Тойоды Киичиро.
К 1937 году подразделение по производству автомобилей официально отделило от подразделения компании по производству автоматизированных ткацких станков — Toyota Motor Company была официально основана .
Под руководством Киичиро Тойода она стала собственной независимой компанией. Киичиро хотел создать лучший автомобиль в мире. Самая первая его модель называлась Model A. Она имеет кузов Chrysler, раму и заднюю ось производства Ford, а также переднюю ось и двигатель производства Chevrolet.В то время TPS не походил ни на что прежде в мире.
К этому времени TPS включила еще одно теоретическое изобретение Сакичи Тойоды, концепцию автоматизации под названием Just-in-Time, или JIT. Эта концепция изначально возникла в результате инцидента, во время которого Киичиро опоздал на поезд, находясь в Англии. Поезд действительно ушел вовремя. Однако Киичиро опоздал на поезд на несколько секунд.
На основе этого, казалось бы, несущественного инцидента Сакичи разработал концепцию, согласно которой материалы для TPS должны поступать на завод именно тогда, когда они необходимы, а не слишком рано или слишком поздно.Он представил и включил эту концепцию в TPS в 1936 году.
Тайити Оно: уменьшение размера лота и появление TPSХотя заслуга в создании TPS в значительной степени принадлежит Сакичи Тойода, его фактическое улучшение, если не фактическое создание, следует приписать японскому промышленному инженеру и бизнесмену по имени Taiichi Ohno . Оно пришел в Toyota Motor Company в 1943 году, и ему сразу же было поручено возглавить цех механической обработки. В то время в этом магазине были станки, которыми управлял опытный мастер.
Под руководством Оно механический цех был преобразован в последовательность операций, в которой машины были расположены таким образом, чтобы каждый мастер отвечал за несколько станков. Это преобразование уменьшило размер лотов в магазине и позволило каждому мастеру возглавить от 5 до 10 отдельных машин.
Революция в организации производства от непрерывного производстваЕще одним изменением, приписываемым Оно, стала революция в производственной организации, которая включила в себя концепт JIT компании Toyoda.Оно полностью реализовал эту концепцию вскоре после того, как возглавил цех механической обработки.
До его приезда фактическое производство, которое происходило в цехе, было спланировано заранее. Менеджеры и руководители должны были попытаться угадать или оценить, каким будет потребительский спрос, а затем на основе этой оценки определить, какой тип и сколько товаров производить. Затем программа производства была продвинута через производство в процессе, который был буквально известен как система выталкивания.Конечно, эта система была очень несовершенной, потому что не было реального способа предсказать, сколько и какие продукты будут покупать клиенты.
Прогнозы системы выталкивания часто были неверными, что приводило к тому, что в любой момент времени производилось слишком много или слишком мало продуктов.
Под руководством Оно было отказано от выталкивающей системы в пользу отслеживания запасов и воспроизведения только того, что покупатели вытащили из запасов. Эта система называлась вытягивающей системой и была основана на той же системе, которая использовалась в то время в американских супермаркетах.
По сути, система записывала, что покупатели сняли с полок и купили. Товары, продаваемые в наибольших количествах и самыми быстрыми темпами, производились и пополнялись.
Оно полностью внедрило вытяжную систему в TPS в 1948 году.
Система КанбанСистема вытягивания давала ряд преимуществ для производства и TPS, но не без недостатков. А именно, не было возможности быстро передать информацию из супермаркета обратно на завод.На самых ранних этапах системы требовалось, чтобы кто-то записал названия продуктов и количество на листе бумаги, а затем отправил их на производственное предприятие.
Со временем бумага, на которой была записана информация, была заменена на постоянных карточек с цветовой кодировкой и подробной информацией — система называется Канбан. Карты пошли по кругу. Каждый раз, когда покупатель снимал детали с полок супермаркета, сами карты возвращались в производство.Затем они прошли производство вместе с множеством других продуктов. В конечном итоге они снова оказались на полках супермаркетов с урезанными товарами и, таким образом, были готовы к следующему циклу.
Непрерывное совершенствованиеЭйдзи Тойода реализовал еще одну концепцию, называемую непрерывным совершенствованием, которая станет краеугольным камнем TPS. Он почерпнул эту идею из буклета Ford, который он получил и привез с собой после посещения завода Ford. В буклете изложена философия постоянного поощрения сотрудников к высказыванию своих идей по улучшению.
Вдохновленный этой идеей, Эйдзи представил TPS и Toyota Motor Company в 1950 году. Интересно, что Toyota поддержала эту идею, в то время как Ford в конце концов отказался от нее.
Линия стоп и система освещения AndonЕще одна концепция, представленная в 1050, — остановка линии . В основе этой идеи лежал тот же принцип автоматизации, который внедрил и разработал Сакичи Тойода. По сути, он останавливал производство всякий раз, когда в системе обнаруживалась неисправность или дефект.
Оно также применил эту систему на сборочных линиях. Он пошел дальше, настаивая на том, чтобы руководители спешили на помощь работнику, который обнаружил дефект или отклонение от нормы, но не смог отремонтировать или устранить его достаточно быстро в отведенное ему время. Хотя эта идея в значительной степени приписывается Toyota Motor Company и TPS, она не совсем чужда другим производителям автомобилей.
Генри Форд — концепция, аналогичная остановке линии на его собственном заводе еще в 1930 году.
Как и ожидалось, концепция изначально привела к значительному количеству остановок на конвейере и производстве. Сам процесс в то время не был достаточно стабильным, чтобы его можно было продолжать. Однако Со временем Оно улучшило систему, что позволило производственным линиям начать работать более эффективно и плавно.
Его усовершенствование произошло благодаря технологии под названием Andon light system . Эта система включала в себя загорание зеленого света, когда все было в порядке, желтого света, когда были обнаружены небольшие проблемы, и красного света, когда линия была немедленно остановлена на заводе.
Современные производственные линии автомобилей, которые используются сегодня, на самом деле не сильно отличаются от базовых систем Ford прошлых лет, если вы посмотрите на самые основы. Автомобили по-прежнему переходят от станции к станции и от рабочего к рабочему по устойчивой конвейерной линии. Все отдельные рабочие выполняют порученные им задачи на назначенных им станциях. Когда каждый рабочий завершает работу и каждая задача выполнена, с конвейера сходит новый автомобиль, готовый к работе и готовый к работе.
Последние изменения
Хотя основные процессы на конвейере более или менее одинаковы, это не означает, что они были невосприимчивы к последним инновациям.
- Стандартизация — Ключевое различие между сегодняшним днем и потом заключается в децентрализации производства : большинство деталей, используемых при производстве автомобилей, больше не производятся собственными силами. Они производятся другими поставщиками на других заводах в стране или по всему миру.Эти поставщики также используют свои собственные версии сборочных линий для производства автомобильных деталей. Автопроизводители могут иметь собственные производственные мощности, на которых они производят собственные автомобильные детали. Производственные мощности расположены не в одном здании с автомобильным заводом. Они могут даже не находиться в том же городе, штате или стране, что и автомобильный завод. Концепция, лежащая в основе покупки или производства автомобильных запчастей на другом заводе по производству автомобилей, включает в себя стандартизацию. Стандартизация — это концепция, доведенная до совершенства компанией Ford с ее взаимозаменяемыми частями.
- Совместное использование платформы — Генри Форд говорил клиентам, продавая свой автомобиль Model T: « Вы можете иметь любой цвет, если он черный. »На его сборочном конвейере в то время не было возможности производить автомобили любого другого цвета, кроме черного. Сегодня производители автомобилей производят автомобили самых разных цветов, марок и моделей. Благодаря инновациям, внедренным такими людьми, как Toyoda, Ohno и другими, стало гораздо больше свободы в производстве сборочных линий.Сама эта свобода основана на концепции под названием , разделяющей платформу . Совместное использование платформы подразумевает, что автомобильная компания разрабатывает и создает автомобили для совместного использования деталей с другими марками и моделями автомобилей. Таким образом, они могут легко производить больше моделей.
- Робототехника — Сегодняшние сборочные линии обеспечивают механизацию деталей и инструментов. Во многих аспектах производством занимаются роботы, которые заняли место рабочих. На некоторых этапах сборочной линии работа выполняется за счет комбинации труда робота и человека .Роботы пригодились для производства автомобилей, потому что многие аспекты производства автомобилей на самом деле опасны и требуют больших физических затрат. Он включает в себя повторяющиеся движения, которые создают напряжение и стресс для человеческого тела. Роботы избавляют рабочих от этого риска. Они делают создание новых автомобилей на конвейере безопаснее и проще во многих отношениях.
- Заводской дизайн и чистота — Наконец, современные сборочные линии сегодня часто называют чистыми , световыми и открытыми .Это уже не те переполненные, грязные, жирные и небезопасные предприятия, какими они были на заре автомобилестроения.
Типы производственных линий
Сегодня производители автомобилей используют на своих заводах множество различных производственных линий. Тип, который используется на объекте, будет зависеть от фактических условий на заводе. Это также будет зависеть от того, какая производительность требуется на самом заводе.
I-линияСамая простая и базовая сборочная линия — это I-line.Это прямая линия , которая короче и в некоторых случаях не автоматизирована. Он не имеет изгибов и обеспечивает легкий доступ как операторам, так и материалам.
Важно, чтобы сборочная линия I-line была короткой; если он будет слишком длинным, это создаст препятствие, потому что переход от одной стороны I-образной линии к другой занимает слишком много времени.
Это также может увеличить отходы при надзоре за линией из-за больших расстояний ходьбы. Операторы могут контролировать только ограниченное количество процессов, которые включают как свой собственный, так и два смежных.
П-образныйU-line — это тип сборочной линии, используемой сегодня в бережливом производстве. Это самый известный , получивший высочайшие отзывы как лучший макет. Это лучшее решение для ручного производства. Однако даже эта линия может создать проблемы, если в U-образной форме находится более одного оператора. Фактически, операторы всегда должны находиться в пределах U-образной части линии, потому что материалы и инструменты поставляются извне.Для установки требуются различные желоба и направляющие для перемещения материалов по линии, которые катятся по линии роликами, находящимися под самой линией.
Для U-линии требуется отдельный оператор, который должен обрабатывать процессы пополнения для устройства. Основное преимущество U-line заключается в том, что все процессы находятся под рукой. Операторы могут контролировать не только свои собственные процессы, но и смежные с ними. Кроме того, они могут видеть процессы, происходящие по ту сторону U-образной линии.
U-образные линии используются, когда требуется работа с несколькими станками. Рабочий может выполнять работу, выполняемую как в начале, так и в конце линии, благодаря тому, как линия настроена.
Его масштаб также можно отрегулировать, увеличивая или уменьшая масштаб. Руководители просто должны перемещать рабочих, чтобы увеличить или уменьшить масштабы операций на U-линии. Когда есть высокий спрос на производство, руководители могут назначить одного рабочего на каждую станцию. Когда производственные потребности низкие, на все станции может быть назначен один рабочий.
Модель S-LineЭтот тип сборочной линии наиболее часто используется в автомобильной промышленности . Он создается с помощью нескольких I-линий, которые расположены таким образом, чтобы создать S-образную форму. При использовании на больших заводах он может легко быть длиннее мили. Благодаря такой форме логистические операции и транспортировка материалов не тратятся зря, и она намного легче вписывается в завод.
L-образныйL-line — это последняя конструкция конвейерной линии, используемая сегодня на заводах.L-линия обычно создается по необходимости, потому что на заводе просто не хватает места для другой производственной линии. Он похож по конструкции на I-line и представляет те же проблемы.
Машинки ручной работы
Хотя это наиболее распространенные типы сборочных линий, которые сегодня можно найти на многих заводах по производству автомобилей, они не используются некоторыми избранными производителями автомобилей. А именно, Aston Martin и Ferrari предпочитают создавать свои автомобили вручную.
Каждый из автомобилей этих компаний изготавливается на заказ в соответствии с требованиями каждого клиента.Фактически, они даже изготовят индивидуальное сиденье водителя по точным размерам заказчика. При этом у компаний нет необходимости в сборочных линиях на своих производственных площадях.
Объединение потоков материалов в рамках производства
Вышеупомянутые схемы линий сегодня можно найти на множестве автомобильных заводов. Однако на других предприятиях можно встретить слияние производственных линий. В редких случаях производственные линии могут быть временно или навсегда разделены, особенно когда фабрика должна производить различную продукцию.
Основным преимуществом объединения вторичной производственной линии с основной линией является быстрое использование материалов . Фактически, владельцам заводов часто не нужен склад для хранения излишков материалов, потому что они будут немедленно израсходованы во время производства.
Однако для того, чтобы эта установка работала, скорость и спрос на вторичной линии должны соответствовать спросу и скорости первой. Когда обе линии идут в ногу друг с другом, инвентарь для отслеживания магазина отсутствует.
Три типа линий слияния, используемых сегодня на заводах, включают:
- Гребневая линия, которая включает в себя слияние всех второстепенных линий с одной стороны линии
- Линия корешка, которая включает в себя сборочные линии, идущие со всех сторон. Это также называется линией «рыбьей кости» .
- Сложная линия , иногда называемая потоком создания ценности, которая включает в себя множество ветвей и сложных систем, объединяющих все типы линий в одну
Все три линии способствуют быстрому и стабильному использованию запасов, устраняя необходимость в дополнительном складе, что может сэкономить компании деньги.
Современное производство, окружающая среда и удовлетворенность работников
Промышленная революция привела к беспрецедентному росту производительности и производства по всему миру. Никогда прежде технологии, позволяющие заменять детали и сборочные линии, не были найдены где-либо еще.
Эта технология отвечает за удобство и богатство продуктов и услуг, которыми люди повсюду пользуются и которые в большинстве своем ежедневно воспринимают как должное.Более того, сегодняшнее глобальное процветание в значительной степени связано с изобретением, обслуживанием и постоянным совершенствованием производственных процессов.
Улучшения сборочной линии
Усовершенствования, обнаруженные сегодня на сборочных линиях, придают большее значение различным частям высокотехнологичных процессов, используемых сегодня на заводах. Сегодня производство осуществляется посредством так называемых параллельных процессов — множество параллельных операций, которые используются на заключительных этапах сборки.
Эти действия отмечены сложными коммуникациями, графиками производства и планами материальных потоков , все из которых основаны на компьютерных технологиях, которые также отслеживают системы и помогают снизить затраты на хранение и отслеживание запасов.
Современные сборочные линии также включают концепцию под названием Совместная разработка приложений или JAD . JAD объединяет людей, работающих в производственных сферах, с теми, кто работает в сфере информационных технологий или ИТ на одном производственном предприятии.Его основное преимущество заключается в значительном сокращении времени, необходимого для выполнения одного проекта.
Фактор окружающей среды
Более того, сегодня производственные линии работают не только на то, чтобы навести порядок в самой своей архитектуре. Они также значительно улучшают работу , улучшая среду , окружающую помещения, в которых они расположены. Хорошим примером может служить завод Subaru, расположенный в Лафайете, штат Индиана. Этот завод перерабатывает 99,8% отходов производственной деятельности.
Кроме того, многие мировые компании, в том числе производители автомобилей, теперь поощряют своих поставщиков либо забрать, либо переработать свою собственную упаковку. Переработка или возврат упаковки сокращает расходы поставщика. Это также означает, что им придется покупать меньше упаковочных материалов. Многие обнаруживают, что даже нестандартные детали, которые в противном случае были бы выброшены, можно переработать и использовать для новых целей.
Человеческий фактор
В отрасли не секрет, что рабочим автозаводов часто бывает скучно на работе.Они выполняют одни и те же задачи изо дня в день, в конечном итоге теряя интерес к тому, что они делают. Когда они теряют интерес, они ставят под угрозу цель производства и качество продукции.
Чтобы избавиться от скуки рабочих, такие компании, как Toyota, теперь предоставляют рабочим возможности для физических упражнений и отдыха. Рабочие вместе тренируются во время перерывов и имеют возможность расслабиться и пообщаться во время смены.
Им также предоставлены усовершенствованные инновации, которые делают их работу проще и интереснее.Эти новые улучшения ускоряют темпы производства продукции и снятия автомобилей с конвейера. Им нравится работать с меньшим количеством материалов, что снимает не только их скуку, но и снижает физическое и умственное напряжение, которое может возникнуть в связи с их работой.
Такие компании, как Toyota, также заинтересованы в капитале компании. Они получают выгоду через участие в прибыли, бонусы и другие финансовые стимулы . Эти денежные льготы предназначены для увеличения объемов производства и обеспечения ежедневной занятости рабочих.Чем лучше они работают, тем больше увеличивают свою зарплату.
Хотя улучшение сборочных линий и производства, возможно, не было в первую очередь сосредоточено на человеческом опыте, владельцы компаний нашли уникальный стимул для того, чтобы их сотрудники были довольны во время работы.
Качество продукции, а также темпы производства в значительной степени зависят от того, насколько хорошо рабочие на фабрике действительно любят выполнять свою работу.
Когда им предоставляются стимулы, такие как финансовые бонусы, а также новые технологии, с которыми можно работать, сотрудники с большей вероятностью примут участие в проекте.Они также менее склонны рисковать своей работой и здоровьем в производственном цехе.
Доказано, что способность общаться, тренироваться и чувствовать связь с остальной производственной командой повышает моральный дух рабочих. С повышением морального духа улучшаются качество и скорость работы сборочных линий. Этот аспект улучшения сборочных линий имеет не меньшее значение, чем защита окружающей среды, сокращение затрат и создание автомобилей, готовых к работе в демонстрационных залах.
Как работают автомобильные производственные линии
Производственные линии кажутся чем-то, что возникло на рубеже 19-го века, но на самом деле они существуют дольше, чем это.По сути, производственная линия использует разделение труда. В системе разделения труда вместо того, чтобы каждый человек выполнял всю работу от начала до конца в одиночку, каждый берет на себя небольшую часть работы, собирая вместе более мелкие части, пока работа не будет сделана.
Конечно, люди всегда распределяли работу по дому или ферме. Но на протяжении большей части истории человечества, если что-то нужно было построить или обработать, один человек делал это от начала до конца. Квалифицированные мастера оттачивали искусство изготовления одного конкретного изделия.Они учили других выполнять ту же работу, работая над продуктом от начала до конца. Как только продукт был готов, мастер мог обменять готовый продукт на другие товары, в которых он или она нуждались.
Единственная проблема этой системы в том, что она требует очень много времени. Кроме того, чтобы стать квалифицированным мастером, может потребоваться несколько лет обучения. Также здесь делались очень дорогие товары, которые делали ремесленники.
Когда мастера начали разбирать отдельные задачи, связанные с созданием определенного продукта, они обнаружили, что работа идет немного быстрее.Первоначально люди все еще выполняли полуквалифицированный труд в собственных домах. Например, у модистки один человек может вырезать дома выкройки шляп, в то время как другой собирает искусственные цветы, другой связывает ленты в банты, а третий сшивает ткань, и, наконец, третий человек собирает готовую шляпу.
Тем не менее, эти работы требовали небольшого мастерства, и процесс был немного медленным. Однако при более механизированном процессе люди вскоре обнаружили, что процесс может продвигаться намного быстрее.Кроме того, при использовании большего количества оборудования люди, производящие продукт, могут быть менее квалифицированными. Например, вместо того, чтобы искать рабочего, который знал, как разрезать ткань шляпы по выкройке, модистке теперь нужно было только найти человека, который мог загружать ткань в раскройную машину. Вместо того, чтобы знать, как шить, рабочие просто должны были пропустить ткань через швейную машину. Процесс шел быстрее, а из-за неквалифицированной рабочей силы он был дешевле. Переход к добавлению машин в производственный процесс сделал возможным массовое производство разнообразной продукции, включая автомобили.
Как сборочная линия произвела революцию в автомобильной промышленности
К началу 1900-х годов автомобили с бензиновым двигателем стали продаваться лучше всех других типов автомобилей. Рынок автомобилей рос, и потребность в промышленном производстве росла.
Первыми производителями автомобилей в мире были французские компании Panhard & Levassor (1889 г.) и Peugeot (1891 г.). Daimler и Benz начинали как новаторы, которые экспериментировали с автомобильным дизайном для тестирования своих двигателей, прежде чем стать полноценными производителями автомобилей.Они заработали свои первые деньги, лицензируя свои патенты и продавая свои двигатели производителям автомобилей.
Первые сборщики
Рене Панар и Эмиль Левассор были партнерами в бизнесе деревообрабатывающего оборудования, когда решили стать производителями автомобилей. Свой первый автомобиль они построили в 1890 году с двигателем Daimler. Партнеры не только производили автомобили, но и внесли улучшения в конструкцию кузова.
Левассор был первым конструктором, который переместил двигатель в переднюю часть автомобиля и использовал заднеприводную компоновку.Эта конструкция была известна как система Panhard и быстро стала стандартом для всех автомобилей, поскольку обеспечивала лучший баланс и улучшенное рулевое управление. Панара и Левассора также приписывают изобретение современной трансмиссии, которая была установлена в их Panhard 1895 года.
Panhard и Levassor также разделили лицензионные права на двигатели Daimler с Armand Peugot. Автомобиль Peugot выиграл первую автомобильную гонку во Франции, которая получила широкую известность и увеличила продажи автомобилей.По иронии судьбы, гонка «Париж — Марсель» 1897 года привела к автомобильной катастрофе со смертельным исходом, в результате которой погиб Эмиль Левассор.
Вначале французские производители не стандартизировали модели автомобилей, поскольку каждый автомобиль отличался от другого. Первым стандартизированным автомобилем стал Benz Velo 1894 года. В 1895 году было изготовлено 134 идентичных Velos.
Американская сборка автомобилей
Первыми производителями коммерческих автомобилей с газовым двигателем в Америке были Charles и Frank Duryea .Братья были производителями велосипедов, которые заинтересовались бензиновыми двигателями и автомобилями. Они построили свой первый автомобиль в 1893 году в Спрингфилде, штат Массачусетс, а к 1896 году компания Duryea Motor Wagon Company продала тринадцать моделей Duryea, дорогого лимузина, производившегося до 1920-х годов.
Первым автомобилем, массово производимым в Соединенных Штатах, был Oldsmobile Curved Dash 1901 года, построенный американским производителем автомобилей Рэнсом Эли Олдсом (1864-1950).Олдс изобрел основную концепцию сборочной линии и положил начало автомобильной промышленности в районе Детройта. Впервые он начал производить паровые и бензиновые двигатели вместе со своим отцом, Плинием Фиском Олдсом, в Лансинге, штат Мичиган, в 1885 году.
Олдс сконструировал свой первый паровой автомобиль в 1887 году. В 1899 году, имея опыт в производстве бензиновых двигателей, Олдс переехал в Детройт, чтобы основать Olds Motor Works с целью производства недорогих автомобилей. Он произвел 425 «Curved Dash Olds» в 1901 году и был ведущим производителем автомобилей в Америке с 1901 по 1904 год.
Генри Форд революционизирует производство
Американскому производителю автомобилей Генри Форду (1863-1947) приписывают изобретение усовершенствованной сборочной линии. Он основал Ford Motor Company в 1903 году. Это была третья автомобильная компания, созданная для производства автомобилей, которые он проектировал. Он представил модель T в 1908 году, и она имела большой успех.
Примерно в 1913 году он установил первую сборочную линию с конвейерной лентой на своем автомобильном заводе в Форд-Хайленд-Парк, штат Мичиган.Линия сборки снизила затраты на производство автомобилей за счет сокращения времени сборки. Например, знаменитая модель Т Форда была собрана за девяносто три минуты. После установки движущихся сборочных линий на своем заводе Форд стал крупнейшим в мире производителем автомобилей. К 1927 году было выпущено 15 миллионов моделей T.
Другой победой Генри Форда стала патентная битва с Джорджем Б. Селденом. Селден, обладатель патента на «дорожный двигатель». На этом основании все американские производители автомобилей выплачивали Селдену гонорары.Форд отменил патент Селдена и открыл американский автомобильный рынок для производства недорогих автомобилей.
роботов для производства автомобилей | Робототехника для автомобилестроения
Роботы для производства автомобилей дают автомобильным компаниям конкурентное преимущество. Повышают качество и снижают гарантийные расходы; увеличить пропускную способность и устранить узкие места; и защитить рабочих от грязной, сложной и опасной работы. На заводах по сборке автомобилей роботы используются исключительно для точечной сварки и покраски, но есть много других возможностей для использования роботов в цепочке поставок.OEM-производители, производители Tier 1 и другие производители запчастей выиграют от использования роботов в автомобилестроении.
Производители обращаются к роботам по многим причинам. В автомобильной промышленности три важнейших фактора — качество, мощность и безопасность.
Повышение качества в автомобильной промышленности
Роботы для автомобильных заводов снижают вариативность изготовления деталей. С высокой повторяемостью, они никогда не утомляются и не отвлекаются, поэтому каждый цикл выполняется одинаково. Они также не роняют детали и не обращаются с ними таким образом, чтобы вызвать повреждения.Это снижает количество отходов, которые ранее были вызваны человеческой ошибкой, что также означает меньшую вариативность при сборке автомобиля. Автомобильные роботы, оснащенные системами технического зрения, могут даже обнаруживать изменения в поступающих материалах и адаптировать свои запрограммированные траектории в соответствии с требованиями. Это, в свою очередь, приводит к большей удовлетворенности клиентов, меньшему количеству ошибок и снижению гарантийных расходов.
Обращение к производственным мощностям
Цепочки поставок для автомобильной промышленности работают экономно с минимальными запасами для защиты от задержек в производстве. Производители автомобильных запчастей стремятся к постоянному времени и контролю процессов на каждом этапе производственной линии.Даже самая незначительная проблема может остановить сборочную линию. Роботы не страдают усталостью в конце смены, поэтому продолжительность цикла постоянна весь день, каждый день, а пиковая производительность одинакова. Более того, запуск роботов через перерывы и смены смен дает дополнительную производительность производственных линий по сравнению с линиями, обслуживаемыми вручную.
Защита рабочих
Многие рабочие места в автомобилестроении опасны. Иногда опасности очевидны, например, при заливке расплавленного металла в литейном цехе.Другие времена, они более коварны, как и опорно-двигательного аппарата в результате подъема, скручиванию и повторяющихся движений. Роботы могут предотвратить эти риски для людей. При сборке автомобилей роботы защищают рабочих от воздействия дыма от сварки и покраски, а также от вспышки сварного шва и шума штамповочных прессов. Автомобильная робототехника сокращает количество несчастных случаев и исков о травмах, отстраняя рабочих от этих грязных и опасных задач и условий.
Повышение гибкости
Автомобильные роботы имеют три преимущества перед жесткой или специализированной автоматизацией:
- Минимальное время переключения с одного задания на другое .Гибкая конструкция захвата — это часто все, что нужно для загрузки новой программы обработки деталей.
- Способность работать с семействами продуктов . Будь то роботы на сборочном конвейере, быстрая точечная сварка кузовов различных типов автомобилей или компактная машина для обрезки целого ряда пластиковых деталей, роботы могут переключаться практически мгновенно. Используя системы технического зрения или другие технологии, такие как RFID-метки, можно обрабатывать самые разные детали.
- Снижение риска устаревания .Когда линейка продуктов исчезает, робота можно повторно развернуть с небольшими дополнительными затратами или бесплатно. Напротив, жесткая автоматизация обычно прекращается.
Автомобильные приложения для роботов
В каждом легковом и грузовом автомобиле есть тысячи деталей, и для их изготовления требуется множество производственных процессов. Достижения в области технологий автомобильной робототехники, таких как системы технического зрения и измерения силы, означают, что больше, чем когда-либо, они подходят для робототехнической автоматизации.
Вот некоторые из наиболее подходящих областей применения:
- Сварка (Точечная и дуговая) : Большие роботы с высокой грузоподъемностью и большим радиусом действия могут сваривать панели кузова автомобиля точечной сваркой; в то время как меньшие роботы сваривают такие узлы, как кронштейны и крепления.Роботизированная сварка MIG и TIG обеспечивает одинаковую ориентацию горелки в каждом цикле, а повторяемость скорости и дугового зазора гарантирует, что каждая сварка выполняется в соответствии с одними и теми же высокими стандартами.
- Сборка: такие задачи, как заворачивание шурупов, установка лобового стекла и установка колес, — все это кандидаты на роль роботизированного манипулятора на автомобильных заводах. На многих заводах по производству автомобильных запчастей роботы — например, высокоскоростные машины «Дельта» — собирают более мелкие узлы, такие как насосы и двигатели.
- Обслуживание станка : Выгрузка горячего формованного изделия из машины для литья под давлением или литья под давлением, а также загрузка и выгрузка обрабатывающих центров с ЧПУ — все это хорошие примеры роботов, обслуживающих производственные машины.
- Удаление материала: поскольку он может многократно следовать по сложному пути, робот является идеальным инструментом для легких операций по обрезке и резке. Примеры включают раскрой тканей, таких как обшивка потолка, обрезка кромок пластиковых формованных изделий и отливок под давлением, а также формы для полировки. Технология определения силы позволяет роботу поддерживать постоянное давление на поверхность в подобных случаях.
- Перенос детали : Заливка расплавленного металла в литейном цехе и перенос металлического штампа с одного пресса на другой — неприятная работа для людей, но это идеальные задачи для роботов.
Дополнительные сведения о робототехнике в автомобильной промышленности
Сборочные предприятия и производители запчастей являются одними из крупнейших пользователей робототехники в автомобилестроении. Программировать и развертывать роботов проще, чем когда-либо, но каждый проект интеграции сопряжен с уникальными проблемами.Вот почему производители, заинтересованные во внедрении автомобильной робототехники, должны работать с опытным партнером по интеграции для проектирования и установки.
Acieta успешно установила более 5000 промышленных роботов за последние 37 лет в Северной Америке. Чтобы узнать, как мы можем помочь вам внедрить роботизированное производство для автомобилей, свяжитесь с нами сегодня.
|
|
Что происходит на конвейере сборки автомобилей? (с иллюстрациями)
Линия сборки автомобилей — это место, где автомобили собирают из множества мелких компонентов и деталей.Обычно рабочие линии по сборке автомобилей разделены на различные компоненты: они устанавливают детали на шасси движущегося транспортного средства в определенном порядке. Это позволяет транспортному средству начать поездку по сборочной линии в виде голой рамы и завершить поездку по сборочной линии, выехав с завода. Каждый компонент автомобиля устанавливается на автомобиль, когда он движется по конвейеру. Большинство заводов производят от 60 до 100 автомобилей в час на типичной сборочной линии.
Изобретенная Генри Фордом линия сборки автомобилей позволила построить такой автомобиль, как Model T, с гораздо меньшими затратами, чем аналогичный автомобиль, построенный одним рабочим.Доказано, что эта теория работает настолько хорошо, что почти каждый тип продукции массового производства, производимой сегодня на производственных предприятиях по всему миру, производится на сборочной линии. Специальные отделы, такие как отдел трансмиссии, несут ответственность за установку двигателя и трансмиссии на транспортном средстве, идущем по сборочной линии. Другие отделы, обычно встречающиеся на конвейере сборки автомобилей, — это отделы салона, дверной линии и шин. Когда автомобиль проезжает мимо конкретной рабочей зоны рабочего, существует определенное количество времени, посвященное завершению процедуры установки, назначенной для этой рабочей станции.
Несмотря на то, что каждая станция на конвейере сборки автомобилей важна, существуют некоторые трудности, которые требуют снятия транспортного средства с конвейера и отправки в зону ремонта.Это также создает проблему на линии, поскольку все компоненты, подлежащие установке, ориентированы на конкретное транспортное средство, движущееся по линии. Когда транспортное средство снимается с линии, все станции на линии должны удалить компонент, предназначенный для этого конкретного транспортного средства, чтобы обеспечить надлежащее снабжение деталями, подходящими для следующего транспортного средства на линии.
Одна из последних остановок на конвейере сборки автомобилей называется финальной сборкой.Этот отдел заправляет автомобиль бензином, а также проверяет его на отсутствие каких-либо компонентов. После того, как транспортное средство было проверено и было подтверждено, что вся сборка на транспортном средстве завершена, рабочий заводит транспортное средство и уезжает с конвейера на стоянку. Это происходит почти 100 раз за восьмичасовую рабочую смену на большинстве заводов по сборке автомобилей по всему миру.
Как это работает: Сборка автомобилей
Автосборочные заводы могут показаться простыми: с одного конца идут материалы, а с другого — готовые автомобили.Но это еще не все, в том числе очень сложный график, который гарантирует, что все будет происходить правильно и вовремя.
Движущаяся сборочная линия, на которой автомобили непрерывно перемещаются между рабочими, которые снова и снова выполняют одну работу, является эффективной. Но это требует серьезного предварительного планирования и максимальной точности не только внутри самого завода, но и с внешними поставщиками и даже с транспортными средствами, которые забирают готовую продукцию.
Индивидуальные производственные процедуры могут незначительно отличаться в зависимости от компании, но первым шагом всегда является определение того, что будет построено.«Мы регулярно встречаемся с нашими группами продаж и производства, чтобы составить прогнозы», — говорит Луай Аун, менеджер по стратегическому планированию Honda of Canada Mfg. Компания изначально составляет долгосрочные прогнозы на несколько лет. Затем прогноз на каждый год разбивается на ежемесячный график, который определяет точные модели и цвета строящихся автомобилей.
На этой фотографии от 14 марта 2014 года рабочие конвейера собирают автомобиль Chrysler 200 2015 года выпуска на сборочном заводе в Стерлинг-Хайтс, штат Мичиган.Конфигурация опций может зависеть от производителя. Некоторые автопроизводители, в том числе Honda, оснащают свои автомобили определенными функциями, которые различаются в зависимости от уровня отделки салона, в то время как другие предлагают элементы в составе дополнительных пакетов или в виде небольшого количества отдельных дополнений. Несколько небольших автопроизводителей, таких как Porsche, позволят покупателям выбирать из множества индивидуальных вариантов для создания индивидуального автомобиля.
Многие, если не большинство, из этих товаров будут предоставлены внешними поставщиками. Каждый дополнительный уровень выбора клиента добавляет сложности, начиная с производителя автомобилей, который должен заказывать нужное количество деталей у своих поставщиков, чтобы соответствовать его прогнозу продаж.Для чего-то, что кажется водителю достаточно простым, например ремня безопасности, требуются такие разнообразные компоненты, как сам ремень, пряжка, монтажное оборудование, а в некоторых автомобилях — механизмы защиты от столкновения. Каждый компонент может быть предоставлен другой компанией, и поставщик должен заказать и согласовать поставки, прежде чем он сможет собрать ремень безопасности и доставить его на автомобильный завод.
На автомобильном заводе заказы на автомобили загружаются в компьютеризированный производственный план. Лист технических характеристик автомобиля следует за ним по сборочной линии, через штрих-коды или бумажные распечатки, которые сканируются на каждой станции, чтобы убедиться, что в автомобиле используются нужные детали и цвета.На некоторых производственных участках цветные точки на автомобилях и деталях используются в качестве дополнительного наглядного пособия. Чтобы упростить координацию сборки, Honda запускает последовательности примерно из тридцати идентичных уровней отделки салона одновременно.
Процесс обычно начинается в кузовном цехе, где панели и компоненты штампуются на прессах. Роботы сваривают их вместе, и машина обретает форму. Пока он не раскрашен, что тоже делают роботы, его называют «тело в белом». После того, как его цвет будет нанесен, сборщики должны завершить сборку автомобиля.
Хотя некоторые детали устанавливаются индивидуально, многие компоненты поступают на конвейер уже собранными, например, тормоза или комбинации приборов. Известные как узлы, они устанавливаются в транспортном средстве как законченные единицы. Некоторые узлы производятся на собственных небольших сборочных линиях внутри завода, а другие поставляются поставщиками. Внутренние линии и поставки поставщика должны быть скоординированы, чтобы было достаточно готовых узлов для того количества автомобилей, которые будут построены в этот день.
Линия двигателей ожидает автомобилей, которые сойдут с конвейера на сборочном заводе Chrysler в Брамптоне, Онтарио.Эффективность движущейся сборочной линии зависит от рабочих, имеющих необходимые детали прямо рядом с ними. Программное обеспечение, которое контролирует производственный процесс, отслеживает количество автомобилей, идущих по конвейеру, что соответствует количеству деталей, которые должны быть доступны сборщику, когда автомобиль достигает каждой рабочей станции. Сравнивая эти числа по мере выполнения каждого задания, компьютерная система знает, когда в каждом бункере осталось только несколько деталей, и сигнализирует о том, что необходимо доставить свежий запас.