Производство композитных и гибридных изделий
СЕРИЯ ПОДГОТОВИТЕЛЬНЫХ РЕАКТОРОВ РЕАКТОР
Применение:
Производство изделий из полимерных композиционных материалов (ПКМ)
- приготовление модульных однокомпонентных реакционноспособных смесевых композиций, готовых к использованию
- производство модульных однокомпонентных связующих составов
- производство модульных отверждающих систем
Краткое описание и состав оборудования:
Подготовительные реакторы обеспечивают качественное приготовление связующего состава и оснащаются:
- емкость реактора с терморубашкой или бункером обогрева
- мешалка с регулируемым электроприводом
- система терморегуляции с принудительным охлаждением
- горловина для ввода компонентов
- система введения наполнителей
- устройство вакуумирования
- модуль подготовки воздуха и избыточного давления
- дозирующие насосы
- смотровое окно с подсветкой
- аппликационный клапан
- модуль взвешивания
- шкаф управления, система контроля и автоматизации
Подготовительные реакторы применяются, как отдельная производственная единица, так и в комплексе с другим оборудованием, образуя отдельный производственный участок подготовки реакционноспособных связующих, а также раздельного приготовления специализированных связующих и отвердителей композиционных систем:
- подготовительный(ые) реактор(ы)
- автоматическая система заправки с устройством подъема крышки реактора
- система весового контроля
- вакуумный узел
- дозирующий узел
- печь для полимеризации
- УФ-отверждение
Применение в комплексе с другим оборудованием:
Вариант 1. Один реактор и более:
приготовление многокомпонентной смесевой композиции для использования полученной системы в течение времени жизни. Подача связующего осуществляется посредством регулируемого избыточного давления в реакторе.
Вариант 2. Один реактор и более в комплексе с дозирующим устройством:
(а) приготовление однокомпонентного связующего состава в реакторе с дозируемой фасовкой в тару для последующего использования в качестве компонента А,
(б) приготовление отверждающей системы с дозируемой фасовкой в тару для последующего использования в качестве компонента Б,
(в) смешивание, дегазация, дозирование и подача приготовленных модульных компонентов А и Б в требуемом соотношении, автоматическое поддержание и контроль рабочих параметров с выводом на панель оператора.
Преимущества:
- высокий уровень автоматизации процесса
- автоматическая система дегазации подготавливаемых связующих и отверждающих систем
- приготовление композиций как готовых к использованию, так и связующих и отверждающих систем по специальным рецептурам
- введение наполнителей, в том числе абразивных
- термостабилизация с возможностью принудительного охлаждения
- электро- или водяной обогрев реактора/термошкаф
- простота в использовании
- удобство управления и очистки реакторов
Производство изделий из композита
Композиты отвоевывают рынок у дорогостоящих натуральных материалов. Их наделили преимуществами, в зависимости от потребностей и условий эксплуатации. Лишили недостатков, которые присущи продукции из натурального сырья. Изготовлением, уникальных по своим свойствам изделий из композита, в Москве занимается компания «Спецпласт Технологии». Мы не только гарантируем высокое качество продукции, но и доступную цену.
Наше предприятие сотрудничает с мировыми лидерами в производстве материалов и оборудования. Технологи компании повышают квалификацию под руководством ведущих европейских специалистов.
Характеристики композитных материалов (стеклопластик, углепластик, АБС-пластик) позволяют их использовать практически во всех отраслях промышленности, строительстве, быту.
Композиты незаменимы, если от изделия требуются следующие свойства:
сложная форма. Любые объемные конфигурации перестали быть проблемой с появлением этих революционных материалов;
эстетические качества. Разнообразие фактур и расцветок позволяет использовать не только их невероятную прочность, но и красоту в изделиях;
индивидуальный проект. Использование этих материалов позволяет воплотить в жизнь любое дизайнерское решение.
единичное изготовление. Одинаково выгодно и серийное производство изделий из композита и небольших партий.
Начнется сотрудничество с компанией «Спецпласт Технологии» с изготовления 3-D модели. Уже на этом этапе, вы будет точно знать, как будет выглядеть ваше будущее изделие.
Чтобы максимально использовать возможности композитов, нужно учитывать их особенности.
Стеклопластик. Один из самых применяемых композитных материалов. Он обладает хорошей прочностью. Стойкий к повреждениям механического и химического характера. Долговечный. Широко используется в автомобиле и судостроении, строительстве, в том числе и в качестве декоративного материала. Диэлектрик.
АБС-пластик. Его сферу применения сужают некоторые недостатки материала — неустойчивость к ультрафиолетовому излучению. Но это не мешает его широко использовать для внутренней отделки. В производстве товаров бытового назначения, ему и вовсе нет равных. Пластиковая посуда, канцелярские принадлежности, садово-огородный инвентарь, игрушки, CD-диски – изготавливают именно из этого полимера.
Углепластик.
Наиболее дорогостоящий, из-за особенностей технологии производства, материал. Превосходит другие композиты в прочности, эластичности, термостойкости и легкости. При этом, чувствителен к точечным ударам. Область применения – обширна. От лезвий на коньках до болидов Формулы 1.
Какой бы материал вы ни выбрали, можете быть уверенными, что для производства изделий из стеклопластика, вы обратились к надежному партнеру. «Спецпласт Технологии» в кратчайшие сроки просчитает их стоимость, изготовит макет и приступит к выполнению заказа. Обращайтесь, и наши менеджеры предоставят бесплатную консультацию по номеру телефона 8 (495) 177-89-23, 8 (985) 440-85-35 либо через email: [email protected]
Отправьте заявку на рассчет и получите Ваше персональное выгодное предложение.
Нажимая на кнопку «Получить расчет» Вы даете согласие на обработку своих персональных данных.
Производство композитов напылением — технология, материалы, преимущества, области применения
Технология производства напылением получила распространение при мелко и средне-серийном производстве изделий, а также при производстве крупных стеклопластиковых изделий, таких как корпуса катеров, лодок, яхт, кабины автотранспорта, железнодорожных вагонов и т.д.Несмотря на то, что в данном случае подразумеваются определённые затраты на закупку специализированного оборудования для производства, технология производства напылением имеет ряд преимуществ перед технологией производства ручным формованием. Нанесение гелькоута и стеклопластика осуществляется с помощью специального оборудования. При этом отпадает необходимость в предварительном раскрое армирующих материалов и приготовлении смеси связующего, резко сокращается доля ручного труда при производстве изделия.
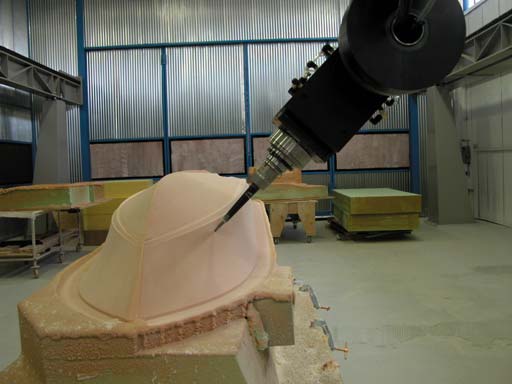
Армирующие элементы: стеклоровинг
Заполнители: не применимы. Сэндвич изготавливается раздельно.Преимущества:
- не требуется раскрой и подготовка смеси смола/отвердитель, что позволяет экономить время, полезные площади, работу персонала;
- существенно сокращаются производственные площади из-за снижения числа специально оборудованных мест для производства;
- увеличивается скорость производства;
- упрощается контроль над качеством;
- экономится фонд заработной платы при производстве;
- снижается себестоимость конечного изделия, так как стеклянный ровинг — наиболее дешёвый материал из стекла;
- существенно снижается количество отходов.
- меньше соотношение наполнитель/смола;
- меньше прочность изделия;
- длительное время контакта с вредными веществами;
- высокий вес;
- прочие недостатки приводят к тому, что производство изделий оправдано только из стеклопластика;
- качество конечного изделия в основном зависит от мастерства оператора установки.
КОМПОЗИТ» — Производство Композитных материалов
«ПМ-КОМПОЗИТ»
Завод по производству
композитных материалов
Автомобильная
отрасль
Железнодорожная
отрасль
отрасль 03
Строительная
отрасль
Энергетическая
отрасль
Потребительская
отрасль
Разрабатываем продукты из композитов для следующих отраслей:
Автомобильная отрасль
Железнодорожная отрасль
Аэрокосмическая отрасль
Строительная отрасль
Потребительская отрасль
Услуги компании
«ПМ-Композит» оказывает полный комплекс услуг по производству изделий из полимерных композиционных материалов
включая весь цикл инжинирингового сопровождения.
01
Совместная разработка
технического задания
02
Проведение исследований
и испытаний
03
Разработка дизайна
04
Компьютерное
моделирование
05
Производство
06
Разработка конструкторской
и технической документации
Перемещайте фотографии мышкой или стрелками клавиатуры
Преимущества
композитных материалов
Изделия любой
формы
Низкие затраты
Законченный
внешний вид
Гибкость
конструкционных
решений
Устойчивость
к коррозии
Стабильность
размеров
Долговечность
Высокая
ударопрочность
Радиопрозрачность
Звукопоглощение
Высокая
прочность
Долговечность
Низкие затраты на содержание
Законченный внешний вид
Высокая прочность
Устойчивость к коррозии
Высокая ударопрочность
Изделия любой формы
Гибкость констуркционных решений
Стабильность размеров
Звукопоглощение
Радиопрозрачность
разработка и производство изделий из композитов
Sagrit company specializes in the manufacture of fiber-reinforced plastic and thermoformed plastic components. We can produce fiber-reinforced parts (with glass and carbon fiber) via vacuum infusion, RTM, compression molding and also via hand lay-up and spray-up lamination.
The goal of the company is to develop applications of polymer composite materials in Russia on a base of existing European technologies as well as with using company’s own research.
Sagrit is playing several roles for its clients: firstly, it can be a supplier of parts from composites and, secondly, it can act as engineering and consulting company that helps to choose and evaluate the best suitable technology and to organize manufacture in the area of the client.
“Sagrit” is a full cycle manufacturing enterprise. We develop, design and manufacture products from fiberglass and other composite and polymeric materials, using modern high performance technologies. Products made of fiberglass and carbon fiber by custom orders are becoming more widespread, due to many advantages of composite materials, most important among which are: durability (resistance to corrosion and mechanical damage), dielectric properties, wide design possibilities, manufacturability (ease of manufacture), weight reduction compared to metal.
We manufacture matrixes on a high precision 5-axis CNC machine that allows to produce single-piece tooling, which in turn allows us to produce large details without unnecessary seams and with high accuracy.
We use different technologies of production from composite materials: RTM, vacuum infusion, spraying, molding of SMC prepregs, as well as pressing prepregs and reinforced thermoplastics (GMT, LWRT, Loprefin).
For customers who require production of small or medium series, and depending on the size of the product and requirements for its characteristics, we apply the method of vacuum infusion and spraying. In the case of high demands to the quality of the material, i.e. for heavyload products, we use the RTM technology.
For customers who have a need for the products of medium and large series, we can offer the technology of pressing of the prepregs. Depending on requirements for mechanical properties of the material, its thermal and chemical resistance, we use the method of pressing of SMC materials, pressing carbonfiber prepregs or alternative technologies using reinforced thermoplastics, such as GMT, LWRT, Loprefin.
A special role in our enterprise is given not the production of analogues, but to the development and production of innovative products from composite materials.
Sagrit acts for its customers both as a supplier of finished products from polymer composites, and as an engineering and consulting company – in selecting and technically and economically substantiating the optimum materials and technologies, as well as organizing production on the customer’s equipment.
Литье изделий из композитных материалов на заказ в Самаре
- Главная
- Изготовление изделий из композита
Из полимерных композитов мы выпускаем различные изделия, включая детали для промышленного и бытового оборудования. За счет двух и более компонентов в их составе, достигаются нужные свойства композита. В итоге материал тверд, пластичен, долговечен, не страдает от коррозии и влаги, эстетично выглядит. Композитная матрица в сочетании с наполнителями обеспечивает прочность. Конкретный состав варьируется в зависимости от того, какие свойства требуются.
Сфера применения композитных материалов
Детали из композита превосходят по характеристикам аналоги из металлов и сплавов. Свое применение различные вариации этого материала находят в строительстве зданий и сооружений — как жилых, так и коммерческих, промышленных и прочих.
Другие сферы использования:
-
создание осевых вентиляторов и ветряных энергоустановок;
-
разработка электрических транспортных средств, автомобилей и спецтранспорта;
-
обустройство территорий, оснащение и декорирование архитектуры.
Композитные детали используются в медицинской сфере, металлургии, химической и энергетической промышленности, при прокладке дорог. Они находят применение в разработке авиационной и космической техники, снегоходов, железнодорожного и водного транспорта.
Литье композитов
Процесс изготовления требует, чтобы были учтены условия эксплуатации, уровень механической нагрузки, температура и другие внешние факторы. Сначала проектируют форму и размеры изделия, разрабатывают материал согласно условиям. В процессе обязательно подбирают волокна и структуру композита, совершенствуют его итоговые характеристики.
Чтобы добиться соответствия заданным критериям, перед серийным производством изготавливают опытный образец. Его испытывают сначала при умеренной, а потом при высокой нагрузке. Современное оснащение позволяет выпускать детали с несколькими матрицами и гибридные элементы с разными наполнителями. В составе матриц — металл, керамика, полимеры, цемент, другие природные и искусственные соединения.
Особенности выпуска композитных изделий в ходе ручного формования:
-
основную работу проводят при помощи матрицы с защитным покрытием — за счет него создается внешний слой детали;
-
когда слой высыхает, укладывают наполнитель и пропитывают его связующим составом;
-
затем деталь подвергают механической обработке.
Выпуская элементы из композита, применяют формирование в условиях вакуума. В это время пропитывают армирующие материалы, укладывают дополнительные покрытия и вакуумную пленку. При инфузионном процессе создается вакуумный мешок с материалом внутри. Благодаря вакууму становится возможной пропитка.
Подавая смолу, для нижних и верхних форм применяют слой защиты. Когда слои высыхают, в форму выкладывают материал. Затем закрывают ее, чтобы подавать внутрь связующий состав.
Новые технологии выпуска композитных деталей открывают доступ к различным методам производства. Среди них — формование при помощи автоклава. Также задействуют пультрузию, прямое прессование, напыление, намотку и другие методики. Каждый из них имеет свои преимущества и находит применение в тех или иных условиях.
Для заказа изделий из композитных материалов звоните 8 (800) 301-92-80.
«В Ростовской области открыт центр по производству изделий из полимерных композитных материалов» в блоге «Технопарки, ОЭЗ, кластеры, инкубаторы…»
В Новочеркасске открылся научно-технологический центр по производству изделий из полимерных композитных материалов. Центр «Технология композитов» будет работать на базе Южно-Российского государственного политехнического университета (НПИ).
Заказы на изготавливаемую продукцию уже поступили от компаний ракетно-космической отрасли. Заинтересованность в получении композитных материалов из Новочеркасска выразил и вертолетостроительный завод в Ростове.
Создание НТЦ позволит сконцентрировать работы по развитию технологий для изготовления композитных изделий различного назначения методом автоматизированной выкладки, при использовании отечественных композиционных материалов.
Учёные вуза уже более сорока лет ведут разработки в области технологий, оборудования и программного обеспечения для создания изделий из полимерных композитных материалов методами непрерывной намотки. За это время НИИ ВИУС выпустило более 30-ти модификаций намоточных станков, на которых изготавливаются баллоны высокого давления, ракетные двигатели твердого топлива, судовые антенные обтекатели, детали авиационной техники, различные ёмкости и прочие изделия.
Перечисляя основные направления работы НТЦ — разработка оборудования для намотки, для выкладки, разработка отпускных механизмов, программного обеспечение для управления станками, разработка систем для испытания изделий из композитов — заместитель директора НТЦ «Технологии композитов» Дмитрий Князев отметил, что преимущества композиционных материалов широко известны: они позволяют получать лёгкие, прочные, жёсткие конструкции, при формировании которых можно добиться необходимых эксплуатационных характеристик.
— На настоящий момент существует около десяти способов изготовления композиционных изделий, мы в рамках НТЦ «Технология композитов» занимаемся двумя из них — намоткой и выкладкой, — подчеркнул Дмитрий Николаевич. — Под эти технологии разрабатываем и программное обеспечение, и оборудование. Намоточных и выкладочных станков — буквально единицы. Поэтому российские предприятия вынуждены покупать импортное оборудование. Уникальность НТЦ в том, что здесь станки производятся из наших материалов, с помощью наших конструкторов и инженеров, наши программисты пишут для них программы. В таком комплексе к созданию изделий из композиционных материалов методом намотки и выкладки кроме нас никто не подходит.
В числе заказчиков НТЦ «Технология композитов» компании с мировыми именами: ПАО «Ракетно-космическая «Энергия им. С.П. Королева», АО «Корпорация «Московский институт теплотехники», АО «Конструкторское бюро приборостроения им. академика А. Г. Шипунова», АО «Центральный Научно-исследовательский институт специального машиностроения» и многие другие.
Руководство по композитным материалам: Производство — NetComposites
Если рассматривать композитные материалы в целом, существует множество различных вариантов материалов на выбор в областях смол, волокон и сердечников, каждый из которых обладает собственным уникальным набором свойств, таких как прочность, жесткость, ударная вязкость, термостойкость, стоимость, производительность. и т. д. Однако конечные свойства композитной детали, изготовленной из этих различных материалов, зависят не только от индивидуальных свойств полимерной матрицы и волокна (а в многослойных структурах также сердцевины), но также зависят от способ, которым сами материалы спроектированы в детали, а также способ их обработки.
В этом разделе сравниваются несколько широко используемых методов производства композитов и представлены некоторые факторы, которые необходимо учитывать при каждом отдельном процессе, включая влияние каждого процесса на выбор материалов.
Опубликовано любезно Дэвидом Криппсом, Gurit
http://www.gurit.com
Мониторинг отверждения
Процесс, с помощью которого жидкий термореактивный форполимер превращается в твердое твердое вещество, называется «отверждением».
Узнать большеРаспыление
Описывает процессы нанесения распылением.
Узнать большеВлажная / ручная кладка
Описывает процессы мокрой укладки или укладки вручную.
Узнать большеОбмотка нити
Объясняет намотку нити накала и выделяет основные преимущества и недостатки.
Узнать большеПултрузия
Охватывает процесс пултрузии и некоторые варианты материалов.
Узнать большеПеренос смолы
Описывает методы, используемые при переносе смолы.
Узнать большеПроцессы инфузии
Охватывает различные процессы инфузии, включая SCRIMP, RIFT и VARTM.
Узнать большеФормованный препрег
Описывает, что такое предварительная подготовка, и объясняет процесс.
Узнать большеДизайн автоклава
Охватывает системы безопасности, контроля температуры, давления и вакуума, а также дает обзор будущих разработок.
Узнать большеПрепрег низкотемпературный
Описывает препреги низкотемпературного отверждения по сравнению с обычными препрегами.
Узнать большеИнфузионная пленка из смолы
Объясняет метод инфузии полимерной пленки.
Узнать большеПоделиться статьей
Твиттер Facebook LinkedIn Электронная почта
Перейти к формулам Вернуться в Ремонт
Производство композитов — Блог об аэрокосмической инженерииБлог об аэрокосмической технике
На протяжении последних четырех десятилетий использование армированных волокном пластиков (FRP) в инженерных сооружениях неуклонно расширялось: от спортивного оборудования и высокопроизводительных гоночных автомобилей до вертолетов и, в последнее время, коммерческих самолетов. Композиционные материалы, по сути, представляют собой комбинацию двух или более разнородных материалов, которые используются вместе, чтобы объединить лучшие свойства или придать новый набор характеристик, которых ни один из составляющих материалов не может достичь сам по себе. Инженерные композиты обычно состоят из отдельных слоев, которые имеют форму непрерывных прямых волокон (например, углеродных, стеклянных, арамидных и т. Д.), Внедренных в матрицу основного полимера (например, фенола, полиэфира, эпоксидной смолы и т. Д.), Которые являются ламинированный слой за слоем, чтобы создать окончательный материал / структуру.
Что касается производства современных композитных материалов, армированных волокном, наиболее важным аспектом является то, что материал и структура создаются одновременно. Следовательно, любые дефекты, возникающие в процессе производства, напрямую влияют на прочность и жесткость материала и конструкции. Каждая мелочь важна.
За последние 40 лет было разработано большое количество процессов производства композитов, включая: контактное формование, компрессионное формование, формование в вакуумном мешке / автоклаве, ротационное формование, формование с переносом смолы (RTM), обертывание лентой, намотку нитей, пултрузию, расширяющуюся камеру. молдинг и т. д.Все эти процессы имеют несколько общих характеристик; армирующие элементы приводятся в требуемую форму в инструменте или форме, смола и волокна сводятся вместе, возможно, при повышенной температуре и давлении для отверждения смолы, и формовка отделяется от детали после отверждения смолы. Различные методы производства могут быть классифицированы как , прямые процессы (например, RTM, пултрузия, контактное формование), в которых используются отдельные волокна и смола, соединенные вместе в точке формования, или непрямые процессы , в которых используются волокна, предварительно пропитанные смолой ( например.вакуумный мешок / автоклавное формование, компрессионное формование).
Выбор производственного процесса, естественно, будет иметь большое влияние на качество, механические свойства и стоимость изготовления компонента. Согласно Поттеру (1996), идеальный процесс можно определить как имеющий:
- Высокая производительность — короткое время цикла, низкая трудоемкость и т. Д.
- Минимальные затраты на материалы — материалы с низкой добавленной стоимостью, низкие затраты на хранение и транспортировку материалов
- Максимальная геометрическая гибкость — сложность формы и размер детали
- Максимальная гибкость свойств — диапазон матриц, диапазон типов армирования, возможность контролировать механические свойства и индивидуальные характеристики
- Минимальные требования к отделке — изготовление формы сетки
- Надежное и высококачественное производство — низкий процент брака, низкая вариабельность и т. Д.
Не существует производственного процесса, который одновременно удовлетворял бы всем этим требованиям; самое главное, некоторые из этих требований могут быть взаимоисключающими. Ниже показано сравнение 5 наиболее распространенных процессов.
Сравнение технологий производства композитов (1)
Контактное формование
Схема формования контактов(1)
Это старейший и наиболее примитивный производственный процесс, но также наиболее широко используемый во всем мире.При контакте формовочная смола вручную наносится на сухую арматуру, помещенную на поверхность инструмента, и это можно сравнить с приклеиванием обоев с помощью кисти. Затем инструмент и ткань закрываются вакуумным мешком, и воздух из-под мешка удаляется для отверждения ламината при атмосферном давлении. Однако, поскольку прилагаемое давление относительно низкое и отверждение обычно происходит при комнатной температуре, объемная доля арматуры ограничивается естественной плотностью упаковки. Кроме того, качество полностью зависит от квалификации персонала, и из-за сложности надежного обеспечения высококачественного ламината практически невозможно квалифицировать конструктивные элементы контактного формования для коммерческих самолетов. Наконец, из-за ограниченного внешнего давления пористость трудно контролировать, что сильно влияет на вариабельность толщины ламината.
Корабль HMS Wilton, усиленный пластиком (2)
С другой стороны, процесс очень гибкий, идеально подходит для разового производства и требует минимальной инфраструктуры. Хотя контактное формование является предпочтительным процессом для очень больших конструкций, геометрическая гибкость более ограничена с точки зрения создания деталей с мелкими деталями, радиусами углов и т. Д.По этой причине этот процесс широко используется в судостроении из стекловолокна / полиэфирной смолы и для планеров.
В перем. Мешок / автоклав
Укладка препрега для автоклавного отверждения (1)
В современных композитах автоклавные процессы являются наиболее широко используемыми, а автоклавное формование является предпочтительным процессом для аэрокосмической промышленности. В этих процессах используются предварительно пропитанные однонаправленные слои или тканые ткани, которые были частично отверждены или подвергнуты бета-стадии.Одним из недостатков является то, что пре-прег необходимо хранить в морозильной камере, чтобы не допустить улетучивания смолы. Множественные слои препрега укладываются на поверхность инструмента с заранее заданной ориентацией волокон для получения необходимой толщины, а затем покрываются разделительной пленкой, дышащей тканью и вакуумным мешком или силиконовым мешком под давлением. Воздух вытягивается из мешка для создания вакуума, а инструмент нагревается при повышенной температуре и давлении для отверждения смолы. В принципе, несколько циклов извлечения из формы выполняются путем покрытия ламината и применения вакуума после каждых 3-4 слоев, чтобы удалить лишний воздух между слоями.Это снижает коэффициент пухлости и помогает предотвратить расслоение между слоями и контролирует размер толщины. Регулярные циклы извлечения из формы и достаточное гидростатическое давление на деталь во время отверждения — два основных требования для получения хороших форм. Производительность автоклавного формования, как правило, довольно низкая, поскольку ручные циклы укладки, упаковки в пакеты и извлечения из формы требуют значительных затрат труда и времени. Более того, капитальные затраты на автоклавы огромны, что ограничивает их использование более крупными конструкциями, где эти затраты оправданы.Поскольку pre-preg больше не находится в состоянии с низкой добавленной стоимостью, затраты на материалы также выше.
Сэндвич с сотовой структурой с предварительной пропиткой для автоклавного отверждения (1)
Геометрическая гибкость по форме и размеру лучше, чем для большинства процессов. В последнее время стало возможным изготавливать весь пол вертолета как одно целое, что было бы невозможно при металлическом подходе. Формованные детали для автоклавов часто используются в сочетании с сотовыми заполнителями, так что можно изготавливать очень легкие компоненты.Это одна из причин, по которой доминирование формованных изделий для автоклавов, вероятно, сохранится в ближайшем будущем, по крайней мере, в аэрокосмической среде.
Обмотка нити
Схема процесса намотки нити (1)
При намотке нитей жгут волокон пропускают через ванну со смолой и наматывают на вращающуюся оправку, перемещаясь в продольном направлении вдоль оси вращающейся оправки.Если не используются липкие предварительно пропитанные жгуты волокна, путь, по которому следует жгут, должен точно следовать геодезическому пути (пути волокна, которые не вызывают проскальзывания волокон при натяжении). Любой простой спиральный путь на цилиндре определяется как геодезический путь, но как только вводится кривизна в двух направлениях (например, глобус), количество возможных путей становится очень ограниченным. По этой причине гибкость свойств довольно ограничена, так что обмотка накала обычно используется для изготовления трубопроводов, сосудов высокого давления и ракетных двигателей. В частности, сосуды высокого давления подходят для намотки нити, поскольку они имеют два четко определенных направления напряжений (кольцевые и продольные напряжения), которые могут согласовываться с направлением намотки.
Одним из недостатков намотки с нитью является то, что оправка часто находится внутри обмотки. Если в качестве оправки используется вкладыш из металла или полимера, он может образовывать постоянную часть конструкции, но чаще всего обмотка разрезается на концах для извлечения детали из формы. Геометрическая гибкость также ограничивается необходимостью наматывания круглых или призматических форм.Одним из основных преимуществ является то, что процесс поддается автоматизации, так что время цикла и затраты на рабочую силу могут быть низкими при высокой надежности и качестве. Этот последний аспект является одной из причин, почему прилагаются усилия для расширения геометрических границ процесса и возможных приложений.
Трансферное формование смолы (RTM)
Схема процесса трансфертного формования смолы (1)
RTM нельзя рассматривать как единый процесс, его лучше рассматривать как «производственную философию, в которой смола и волокна разделяются до самого последнего момента» (Potter, 1996).Тем не менее, все варианты процесса имеют общие особенности удержания немолотых волокон в замкнутой полости инструмента с приложением разности давлений к подаче смолы, так что смола проникает в арматуру. Инструмент может быть жестким или содержать гибкие элементы. Давление уплотнения на инструмент прикладывают с помощью механических зажимов, инструментального пресса или использования внутреннего вакуума и определяют достигнутую объемную долю волокна по отношению к смоле. RTM используется с 1970-х годов для изготовления обтекателей, а также лопаток компрессоров авиационных двигателей.Основной движущей силой дальнейшего развития процессов RTM является разработка методов изготовления, которые могут преодолеть ограничения геометрической сложности, налагаемые автоклавными формованными изделиями. С точки зрения производительности время циклов ниже, чем у большинства других процессов, а в автомобильной промышленности небольшие компоненты изготавливаются за считанные минуты.
Автомобильная панель, произведенная по RTM
Основным преимуществом RTM является использование материалов с низкой добавленной стоимостью (сухие волокна и смолы с низкой вязкостью), которые не нужно хранить в морозильных камерах, что снижает затраты на материалы и транспортировку.Однако основные преимущества RTM заключаются в их геометрической гибкости и гибкости свойств. RTM может использоваться с тканями, сшитыми UD, ткаными тканями и трехмерными тканями, а инжекция смолы может варьироваться для контроля объемной доли и, следовательно, жесткости и прочности компонента. Кроме того, небольшие компоненты с очень мелкими деталями изготавливаются на жесткой металлической оснастке, а более крупные компоненты могут изготавливаться на гибких формах. Наконец, с помощью строго контролируемого процесса можно создавать профили в форме сетки с минимальными требованиями к отделке.Однако все это происходит за счет более сложной технологии производства. Чтобы гарантировать высокое качество компонентов, необходимо тщательно контролировать впрыскивание смолы и поток смолы, чтобы вся арматура смачивалась в равной степени. Это требует довольно продвинутого моделирования гидродинамики и обширных испытаний, чтобы придумать форму формы, которая обеспечивает равномерный поток смолы ко всем частям компонента.
Пултрузия
Схема процесса пултрузии (1)
В этом процессе волокна вытягиваются из шпулярной доски и пропускаются через ванну со смолой для пропитывания волокон смолой.Затем пропитанные волокна пропускают через формовочную головку, чтобы удалить излишки смолы и предварительно сформировать приблизительную окончательную форму. Затем вводят матрицу для отверждения, которая принимает форму окончательного требуемого поперечного сечения пултрузионной детали. Матрица для отверждения нагревает компонент для уплотнения смолы, и затвердевший фасонный профиль вытягивается из матрицы под натяжением. Это означает, что производительность может быть очень высокой при текущем производстве, но упадет при меньших объемах производства, что потребует замены штампов нового поперечного сечения.Поскольку операция автоматизирована, затраты на рабочую силу низкие, а надежность и качество компонентов высокие. Процесс обычно ограничивается компонентами с постоянным поперечным сечением, что сильно ограничивает области применения. Пултрузия очень мало использовалась в аэрокосмической среде, но нашла применение при производстве стандартизованных профильных балок для строительных конструкций.
Автоматизированные процессы
Использование робототехники в производстве композитов растет быстрыми темпами и, вероятно, является наиболее многообещающей технологией на будущее.Очевидные преимущества автоматизации производственного процесса включают меньшую изменчивость размеров и меньшее количество производственных дефектов. Кроме того, можно более эффективно использовать загружаемый материал и снизить трудозатраты. Один многообещающий класс систем — это так называемые машины для автоматической укладки волокна (AFP), в которых используется роботизированная головка для укладки волокна, которая укладывает несколько предварительно пропитанных жгутов «щелевой ленты», позволяя разрезать, зажимать и перезапускать каждую жгуту. Пока роботизированная головка следует определенному пути волокна, жгуты нагреваются незадолго до нанесения, а затем уплотняются на подложке с помощью специального ролика.Благодаря высокому качеству современной робототехники машины AFP могут обеспечивать высокую производительность и обрабатывать сложные геометрические формы. Текущие области применения включают производство фюзеляжа Boeing 787 и обмотки квадратных коробок, которые затем разрезаются по длине для получения двух C-образных секций для лонжеронов крыла. Интегрированные производственные системы, разработанные такими компаниями, как ElectroImpact, предлагают захватывающие возможности «под ключ» для будущих конструкций самолетов. Эти системы сочетают в себе несколько производственных процессов, например размещение волокон и аддитивное производство на одной головке робота, и, следовательно, упрощают производство смешанных и интегрированных структур с меньшим количеством соединений и соединений.Эти системы также позволят инженерам разрабатывать более эффективные конструкции, такие как интегрированные ортосеточные или изосеточные композитные панели, которые в настоящее время трудно экономично производить в больших масштабах.
Фюзеляж Boeing 787 с нитью накала (3)
Ссылки
(1) Поттер, Кевин (1996). Введение в композитные изделия: проектирование, разработка и производство. Springer, 5-е изд.Чепмен и Холл, Лондон.
(2) http://www.tca2000.co.uk/wilton3small.jpg
(3) http://csmres.co.uk/cs.public.upd/article-images/nose-72668.jpg
Нравится:
Нравится Загрузка …
Похожие сообщенияСамые популярные методы изготовления композитов
К 2024 году объем мирового рынка композитов составит около 130,83 миллиарда долларов. Основной армирующий материал в U.С. — это стекловолокно. В 2017 году он зафиксировал рост в размере 2,1 миллиарда долларов.
Растет спрос на прочные, долговечные и легкие материалы. Многие отрасли промышленности обращаются к композитам, чтобы найти усиление определенной конструкции.
Они хотят решить проблемы, с которыми сталкиваются армированные волокном полимеры. Эти арматуры являются изделиями композитного производства.
В промышленности используются различные методы изготовления композитов. Ваше решение зависит от материала, конструкции и области применения композита.
Вот некоторые из самых популярных методов.
Ручная укладка — это основной метод изготовления термореактивных композитов. Процесс включает укладку слоев препрега на инструмент вручную для создания стопки ламината.
По окончании укладки необходимо нанести смолу на слой слоев. В другом варианте ручной укладки, известном как «мокрый», вам нужно покрыть каждый слой смолой, прежде чем накладывать их вместе.
2. Открытое формованиеКонтактное формование или открытое формование — это недорогой процесс, используемый при создании композитных материалов из стекловолокна. Перед началом изготовления форму сначала обрабатывают разделительным агентом и гелем.
Поместите формовочные материалы на верх формы путем распыления или укладки вручную. В процессе напыления вы должны одновременно распылять смолу и измельченные пряди на формовочную поверхность.
Затем уплотните ламинат рукой, используя валики, и на этом этапе добавьте любой сердцевинный материал.Последний напыляемый слой помогает разместить основные материалы между ламинатом. После этого вы можете дать формовке застыть.
Иногда можно использовать процесс укладки вручную вместе с укладкой распылением, чтобы сократить трудозатраты.
3. Способы введения смолыВ связи с высоким спросом на композитные материалы возрастает потребность в более высоких темпах производства. Многие люди заменяют процесс укладки альтернативными методами, которые способствуют автоматизации производства.
Эти методы изготовления включают:
Трансферное формование смолыЗдесь вы должны поместить в форму сухую арматуру, а затем перекачать смесь смолы и катализатора под низким давлением.
Используемая смола имеет низкую вязкость, поэтому она может проникать в преформу до того, как она затвердеет. Этот процесс позволяет производить высококачественные детали без необходимости в автоклаве.
Он имеет заметное отличие от литьевого формования смолы.Вместо того, чтобы вводить смолу и катализатор в виде смеси, вы вводите их двумя отдельными потоками.
Химическая реакция, которая происходит во время смешивания, затем происходит в форме, а не в дозирующей головке.
Литье под вакуумом для переноса смолы (VARTM)VARTM отличается от других процессов литья под давлением, поскольку не требует использования тепла или давления. Вместо того, чтобы перекачивать смолу под давлением, VARTM втягивает ее в преформу с помощью вакуума.
Таким образом, VARTM использует недорогие инструменты, что позволяет легко производить значительное количество недорогих и сложных деталей.
Обмотка накалаСущественным преимуществом метода изготовления волоконной намотки является низкая стоимость материалов. Этот процесс является непрерывным и может быть полностью автоматизирован.
Наиболее важной областью применения является изготовление валов клюшек для гольфа.
Прочие предметы, такие как цилиндрические детали, удочки и сосуды под давлением, составляют оставшуюся часть бизнеса.
ПултрузияМетод пултрузии — это простой и непрерывный процесс. Здесь вы сначала пропускаете армирующее волокно через горячую ванну со смолой. Затем ему придают особую форму по мере того, как он проходит через несколько формующих направляющих.
После этого он проходит через нагретую матрицу, прежде чем принимает свою окончательную форму и затвердевает. Продукты, полученные пултрузией, гладкие и не нуждаются в последующей обработке.
Этот метод используется в течение десятилетий при производстве стекловолокна и полиэфирных смол.
Трубопрокат Прокатка труб — это метод производства, который можно использовать для изготовления стержней и труб. Основная продукция — конические или цилиндрические трубы небольшого диаметра.
В этом процессе вы должны предварительно разрезать материал на узоры, которые помогут с архитектурой волокна. Затем их выкладывают на поверхность, где их перекатывают оправкой для уплотнения и удаления массы из материалов.
Вы должны перемещать детали выкройки через равные промежутки времени, чтобы обеспечить прочность трубы на изгиб.
Компрессионное формованиеЭтот метод полезен при обработке больших объемов термореактивных материалов. Это лучший вариант для производства более 10 000 деталей.
Композиционные листовые материалы производятся с использованием компаунда для изготовления листов. Сначала следует нанести пасту из смолы, а сверху залить измельченным стекловолокном. Затем вы можете покрыть стекловолокно последним слоем пасты из смолы.
Автомобильная промышленность изучает возможность использования листовых формовочных смесей с углеродным армированием.Это сделано для того, чтобы воспользоваться преимуществом прочности и соотношения жесткости к весу углерода.
Литье под давлениемЭто быстрый метод при низком давлении, распространенный при производстве наполненных термопластов. Процесс происходит быстро, скорость впрыска составляет от одной до пяти секунд. За час можно изготовить до 2000 мелких деталей.
Автоматическое литье под давлением BMC поднимается в рядах и захватывает некоторые рынки, занятые производителями металлических отливок и термопластов.
Важные сведения, которые следует учитывать при использовании методов изготовления композитных материаловКомпозиционные материалы обладают многими желательными свойствами, которые делают их пригодными для использования в различных областях.
Перечисленные выше методы изготовления композитов помогают формировать смолы и арматуру, придавая композитному материалу желаемую форму.
При работе с композитными материалами производители должны поддерживать безопасную рабочую среду. Им также следует решать проблемы здоровья и безопасности, используя защитное снаряжение и разрабатывая общеорганизационные политики мониторинга.
Свяжитесь с нами сегодня для получения дополнительной информации об использовании композитных материалов.
Композитные методы производства | Изучите композиты!
[Эта страница все еще находится в разработке, поэтому может показаться неполной. Это! ]
Есть много разных способов строительства из композитных материалов! Разнообразие может сбить с толку выбор, по какому пути идти с вашим проектом. Сложность усложняется тем, что две очень разные техники могут дать почти одинаковый результат! Эта статья представляет собой обзор наиболее часто используемых методов изготовления деталей из композитных материалов.Где возможно, я буду давать ссылки на серию моих видеороликов, демонстрирующих создание образцов плоского ламината, потому что смотреть, как парень делает что-то из листа, — отличный способ избавиться от множества отвлекающих факторов.
Ручная / влажная лейка
Укладка вручную (или влажная укладка) — это любой процесс, при котором ламинатор вручную смешивает смолу и арматуру. Оттуда его можно развернуть и оставить для застывания или поместить в вакуумный мешок. Ручная укладка требует, чтобы все детали и функции ламинирования были выполнены до того, как смола начнет отверждаться.Это действительно может ограничить количество возможных настроек и деталей. В общем, мокрая укладка может варьироваться от самых дешевых методов с использованием измельчителя и валика до очень дорогих, относительно высокопроизводительных методов с вакуумными мешками и эпоксидной смолой.
Распыление
Есть машины, которые смешивают смолу и распыляют ее из пистолета вместе с небольшими короткими нитями ровинга из стекловолокна. Обычно называемые «измельчители» или «оборудование для распыления», эти машины в сочетании с опытным оператором могут ламинировать очень быстро — и, в зависимости от внимания, уделяемого скатыванию ламината, — потенциально аккуратно. Полученный ламинат не отличается высокими характеристиками. Он богат смолой: легко составляет 60% по весу, а толщина варьируется, и ее часто трудно контролировать.
Для деталей, вес которых не является проблемой, но поверхности с гелевым покрытием и сложной геометрией — это может быть идеальным решением. Корпуса машин, автомобильные панели, душевые кабины, резервуары… есть много областей применения, где ламинирование распылением является отличным вариантом. Однако это может быть жалкая работа, требующая хороших средств индивидуальной защиты и хорошей системы циркуляции воздуха.Результат очень зависит от рабочего, и недостаточное внимание к деталям может привести к пустотам, пористости и искажению поверхности.
Открытое формование
Открытое формование — это процесс «смачивания» сухого армирования смолой в форме. Арматуру можно намочить на месте или на столе или даже пропитать пропиткой для ткани — машиной, используемой для одновременного смачивания больших объемов арматуры. Результаты во многом зависят от навыков команды, выполняющей работу, и, как и при распылении, скручивание ламината для удаления воздуха является критическим шагом.Поскольку арматура отрезается от рулонов и помещается в форму, толщина становится гораздо более постоянной. Ламинаторы должны знать о скользящих стыках в углах и правильно ориентировать слои. Все это происходит в условиях постоянного тикающего времени гелеобразования смолы. Как только смола начнет затвердевать, время увеличится!
Вот несколько видеороликов, демонстрирующих открытое формование:
Открытое формование подходит для проектов, требующих прочности непрерывных волокон в дополнение к сложной геометрии и отделке поверхности гелькоутом. Детали могут иметь переменную толщину и дополнительное усиление по мере необходимости, а также использовать сердечники, такие как Coremat, пену и бальзу. Смолы обычно представляют собой полиэфирные или винилэфирные, хотя эпоксидная смола может быть хорошим вариантом для определенных видов работ. Как правило, из-за вязкости и стоимости будет иметь смысл вакуумировать эпоксидные ламинаты в мешках, чтобы воспользоваться преимуществами ламинатов с более высокими характеристиками, в которых не широко используется мат из рубленых прядей.
Влажная укладка с вакуумным мешком
Мокрая укладка в мешках похожа на «открытое формование» до такой степени, что вся арматура и смола ламинируются в форме.Вместо того, чтобы просто перемещаться и позволять смоле отвердеть, для покрытия детали применяется вакуумный мешок и связанные с ним расходные материалы, а вакуум используется для уплотнения ламината и удаления излишков смолы до того, как смола начнет отверждаться. Вакуумная упаковка — трудоемкая и материалоемкая работа, но она может существенно повлиять на характеристики ламината. Давление в вакуумном мешке, особенно в ламинате с сердечником, способствует лучшему склеиванию сердечника и помогает устранить пустоты в самом ламинате. Однако вы можете перестараться и высосать слишком много смолы — как вы можете видеть в этом видео:
Мокрая укладка в мешках, вероятно, лучше всего использовать для деталей небольшого объема на инструментах, которые либо не герметичны на 100% (для инфузии), либо не выдерживают высоких температур (предварительная подготовка).Для пенопласта или бальзы на фасонных поверхностях упаковка сердцевины в мешки — отличная идея, даже если шкурки отформованы открытым способом с только ручным уплотнением — иначе. прокатка и лопание пузырей. Так что, если вы собираетесь упаковывать только одну вещь — сделайте ее сердцевиной на оболочке со стороны формы. Для производственных целей настой обычно является лучшим и более последовательным выбором. Слишком много вариативности и зависимости от квалифицированного персонала, а при мокрой укладке ламинаторы контактируют со смолой в течение длительных периодов времени, поэтому для этого требуется серьезное защитное снаряжение.
Этот процесс может быть очень аккуратным и при тщательном выполнении может обеспечить отличное качество ламината. Вот видео образца ламината, полученного путем смачивания волокна на пластике — как на полшага до предварительной подготовки — хотя время гелеобразования смолы по-прежнему является ограничивающим фактором для времени укладки.
Одной из ситуаций, когда влажная укладка в мешки является лучшим ответом, является ламинирование вторичных соединений для сборки компонентов конструкции. Часто части, отформованные отдельно, собираются и склеиваются с помощью галтели из наполненной смолы — затем эти две части «склеиваются» или «склеиваются» вместе с материалом мокрой укладки.Как правило, «склейка» подразумевает вторичное склеивание «мат, биакси и полиэстер» открытым формованием, а «склейка» подразумевает мокрую укладку в мешки, как правило, с эпоксидной смолой. Я уверен, что в зависимости от того, где вы живете и с кем проводите время, существует множество совершенно разных терминов!
Настой
Таким образом, вы помещаете стопку сухого армирования в форму, а затем вакуумный мешок с какой-то причудливой водопроводной сеткой поверх — затем вы позволяете разнице давлений между внутренней частью мешка и некоторым количеством смолы в горшке снаружи сосать (толкать) смола через сухой ламинат — смачивание. Это вакуумная инфузия! Это не интуитивно понятно, и вам действительно нужно это увидеть, чтобы понять, что происходит.
Инфузия может выполняться с использованием одноразовых вакуумных пакетов, многоразовых вакуумных пакетов и даже жесткого двустороннего инструмента, который иногда называют «вакуумным трансферным формованием» или «VARTM», если вы инженер. Из-за возможности осторожной загрузки волокна и сердцевины, повторяемого содержания смолы и многоразовых вакуумных пакетов, инфузия является отличным выбором для производства. После того, как процесс запущен, вариативность может быть низкой, а качество детали высоким — особенно потому, что смола заполняет любые потенциальные пустоты.
Трансферное формование смолы (RTM) аналогично, но с RTM смола проталкивается через стек ламината с использованием гораздо более высокого давления. Подробнее о RTM ниже.
Вакуумная инфузия (также известная как: инфузия смолы)
VARTM (также известный как LRTM, вакуумное формование, Light-RTM)
Вакуумное формование смолы с переносом (VARTM) может охватывать множество основ, но обычно это процесс, такой как вакуумная инфузия, но где вместо мешка есть второй твердый или полужесткий инструмент.Сухое волокно ламинируют в одной (или обеих) половинах инструмента, а затем в полость вводят смолу только при атмосферном давлении. VARTM отличается от RTM тем, что RTM использует гораздо большее давление и требует, чтобы инструменты были очень тяжелыми и хорошо зажатыми.
Pre-pregs
С пре-прегами производитель предварительно объединяет смолу и арматуру в суспензию в частично затвердевшем состоянии. Производитель материала нанес ровно нужное количество смолы, а затем частично отвердил (обычно) и заморозил «предварительно пропитанные» арматуры, остановив отверждение и позволив пре-прегам храниться в замороженном состоянии в течение месяцев или лет. Производители разморозят пре-прег и ламинируют его в формы, добавляя ядра и элементы с высокой точностью и повторяемостью. Чтобы превратить пре-преги в готовые детали, их нужно «приготовить» в духовке или автоклаве. Повышенная температура запускает реакцию отверждения, и смола течет, а затем затвердевает, оставляя ламинат с очень точным содержанием смолы.
Подробнее читайте в моей статье «Основы ламинирования препрегами».
Pre-preg — действительно хороший вариант, если вы создаете относительно высокопроизводительный материал — и если у вас есть на это бюджет.Формование оправки, прессовое формование и укладка тяжелых однонаправленных «лонжеронов» обычно лучше всего выполнять с помощью предварительных прег. И действительно легкие вещи, такие как самолеты, гоночные автомобили и спортивное оборудование высокого класса, обычно изготавливаются с использованием материалов pre-preg.
Трансферное формование смолы (RTM)
Трансферное формование смолы похоже на инфузию, но вместо того, чтобы использовать разницу между вакуумом и атмосферным давлением для подачи смолы в и через сухую арматурную стопку, RTM использует насос или напорный бак, чтобы протолкнуть ее под гораздо более высоким давлением.«Давление нагнетания» RTM часто составляет около 10-20 бар (150-300 фунтов на квадратный дюйм), но может достигать 100 бар (1500 фунтов на квадратный дюйм) в некоторых высокопроизводительных методах с очень коротким временем цикла. Это большое давление! Обычно формы RTM либо скрепляются болтами, либо зажимаются в большом гидравлическом прессе с плоскими плитами для выравнивания форм. Поскольку давление очень велико, и это часто делается при высокой температуре, впрыскивание смолы может быть очень быстрым, а время цикла — очень коротким. Многие производители смол разработали смолы мгновенного отверждения, предназначенные для RTM и компрессионного формования.Их цель — сократить время цикла и сделать композиты более конкурентоспособными по сравнению с металлами и литьем под давлением для автомобилей и других приложений с большими объемами.
При вакуумной инфузии детали могут заменяться в лучшем случае каждые несколько часов. В RTM это может происходить каждые несколько минут. Естественно, со всем этим тяжелым инструментом, прессами и зажимными рамами это лучше всего для небольших деталей. Вы заплатите авансом за счет гораздо более высоких затрат на инструменты и оборудование, но для тысяч деталей в месяц RTM — один из лучших вариантов.
Пултрузия
В процессе пултрузии влажное волокно протягивается через формованную головку, которая действительно горячая. Волокно и смола идут с одного конца липкими и выходят полностью затвердевшей частью. Подобно экструзии (которая представляет собой процесс выталкивания), пултрузия (процесс вытягивания — нельзя проталкивать мокрый стекловолокно!) Производит длинные изделия с постоянной формой сечения. Он производит их очень точно и экономично, поэтому пултрузия — отличный вариант для длинных тонких вещей, которые могут заменить металлические профили.
Обратной стороной пултрузии является то, что установка может потребовать большого количества работы и специального оборудования. Матрицы, которые формируют и отверждают готовый профиль, дороги и должны быть тщательно спроектированы. Вы не собираетесь просто пойти на задний двор и заняться пултрузией в масштабе хобби! Но вы можете найти специалиста по пултрузии или купить готовые стандартные профили, которые очень удобны. Перила, трубы, настил, структурные профили — многослойные композитные детали используются во многих сферах.
Обмотка накала
Как и пултрузия, намотка филамента — это хорошо развитый промышленный процесс, который действительно хорош для относительно узкого диапазона композитных продуктов. Для намотки нити используется оправка, которая обычно представляет собой очень длинную узкую мужскую форму. Деталь изготавливается путем обертывания жгутов влажного волокна на оправку заранее разработанным способом. Жгуты обычно смачиваются смолой перед намоткой на оправку. Для управления направлением и углом наматывания каретка с намоточной направляющей перемещается по длине оправки, в то время как оправка вращается.Это синхронизированное движение позволяет укладывать волокно под определенным углом — вроде как на токарном станке можно нарезать резьбу! Посмотрите это видео от Rock West Composites о намотке нити накала.
Намотка из нити применяется при изготовлении трубчатых изделий, а также изделий простой вращающейся формы. Резервуары высокого давления, конические столбы, лонжероны — наиболее часто намотанные нитью детали нагружаются таким образом, чтобы образовалось много кольцевых (вокруг середины под углом 90 градусов к оправке) волокон и смещенных по оси слоев.Возможно нанесение волокна под нулевым градусом (вдоль оси оправки), но это более сложно. Намотка нити обычно представляет собой процесс «открытого формования», при котором влажное волокно наматывается и уплотняется только за счет приложенного усилия натяжения. Иногда перед отверждением снаружи детали наматывают слой «липкой ленты» — это уплотняет материал и обеспечивает хорошую отделку поверхности.
Для деталей с более высокими эксплуатационными характеристиками, использующих углеродное волокно и эпоксидную смолу, вариант изготовления pre-preg с оберткой оправкой даст гораздо более легкие и жесткие трубчатые конструкции.Это намного дороже как с точки зрения труда, так и с точки зрения материалов, но для более толстых и сложных трубчатых конструкций это действительно хороший вариант. Это больше похоже на «ручную намотку ленты», и ее можно отверждать в печи или автоклаве.
Компрессионное формование
Как и RTM, компрессионное формование отлично подходит для производства небольших деталей с геометрией формования «со всех сторон». Множественные компоненты пресс-формы и вставки создают полость, в которую загружается формованный материал. Формы обычно загружаются в большие гидравлические прессы, и детали отверждаются под высоким давлением и температурой.Компрессионное формование может выполняться как с термореактивными, так и с термопластичными смолами, а также с волокнами самых разных типов и длин. Возможна сложная геометрия и переменная толщина деталей, что делает композитные детали функционально подобными металлическим отливкам.
По сравнению с RTM, прессованные детали содержат смолу уже в форме, а не только сухое волокно. Давление зажима уплотняет ламинат, смолу, арматуру и завершает нагрев. Поскольку давление уплотняет весь ламинат, детали, полученные компрессионным формованием, могут иметь гораздо более высокое содержание волокна, чем большинство процессов RTM.Естественно, существует ряд гибридных процессов, которые устраняют разрыв — например, «RTM зазора» — который похож на RTM, где смола вводится в слегка приоткрытую форму, которая затем сжимается.
ATL / AFP — автоматическая отложенная передача
Когда вы получаете робота для ламинирования ваших армирующих материалов — это просто здорово! Автоматическое размещение волокон (AFP) — это процесс, в котором используются средства автоматизации («роботы») для нанесения отдельных жгутов арматуры на поверхность формы. Эти жгуты могут быть сухими или предварительно пропитанными и содержать систему термопластов или термореактивных смол.Автоматическая укладка ленты (ATL) — это аналогичный процесс, при котором робот помещает более широкие ленты (обычно предварительно подготовленные) материала в поверхность формы или на нее. Разница заключается в различии между «лентой» и «паклей». ATL обычно больше подходит для ламинирования более крупных и плоских поверхностей, таких как обшивка крыльев или панели фюзеляжа самолетов. AFP больше подходит для более мелких и сложных деталей, и, поскольку отдельные жгуты не очень широкие, их можно «направлять» при нанесении на форму.
ATL и AFP очень дорогое и сложное, поэтому на данный момент оно имеет смысл только для крупномасштабных проектов, где количество деталей, которые необходимо производить, огромно — и, по прогнозам, на долгие годы.Другим большим преимуществом является то, что он очень воспроизводим и имеет встроенный контроль качества, позволяющий записывать каждое движение. Между человеческими ламинаторами нет интерпретации или возможности недопонимания — и машины могут работать стабильно круглосуточно. Однако программирование должно выполняться осторожно, и люди-инспекторы и операторы должны внимательно следить за процессом и следить за тем, чтобы все было в порядке. Так что это здорово, если вы Boeing или Airbus, но для вашего магазина композитных материалов по соседству это далеко.
Посмотрите несколько видеороликов о крупномасштабных машинах AFP от MTorres и Electroimpact — они показывают, насколько большими, дорогими и потрясающими могут быть автоматизированные композиты!
Достигнут прогресс в создании автоматизированных композитов в меньших и менее дорогих масштабах. Такие компании, как Automated Dynamics (посмотрите видео !, Coriolis Composites и ADD Composites, создают машины меньшего размера для AFP, часто устанавливаемые на промышленных роботах. Они более гибкие для небольших партий компонентов и могут быть запрограммированы с помощью более простых и менее дорогих (но наверное еще дорого!) софт.Машины для укладки плоской ленты также используются для изготовления преформ для компрессионного формования — обычно с использованием термопластичных смол. Это может обеспечить очень высокую производительность и подходит для автомобильной промышленности. Посмотрите это видео, на котором показана линия изготовления заготовок Dieffenbacher Tailored Blank Line от преформы ATL до пресс-формования.
3D-печать
В начале 2020 года будет полдюжины серьезных компаний, производящих 3D-печать композитов, а может, и больше. Это начало конвергенции автоматизации и компоновки композитов в гораздо меньшем масштабе, чем технологии ATL и AFP, используемые для производства аэрокосмических деталей.Ознакомьтесь с моим обзором 3D-печатных композитов на конец 2019 года, чтобы узнать больше о вариантах. Наступил 2021 год, и все быстро развивается — нужно будет обновить!
Keystone Engineering
Компания Keystone Engineering — лидер в производстве высокопрочных и жаропрочных композиционных материалов. Сверхвысокое качество продукции достигается за счет запатентованных технологий производства и методов впрыска смолы.
Составные формы продукта
Формы из готовых композитных материалов включают трубы и стержни до пятнадцати футов в длину и различных диаметров.
Доступны высококачественные композитные листы различных размеров и толщины.
Уникальные формы материалов изготавливаются с помощью наших точных форм по индивидуальному заказу.
Композитные материалы могут быть обработаны в соответствии со спецификациями конструкции детали в нашем собственном точном механическом цехе.
Композитные изделия и технологии изготовления
Ламинирование
Мы специализируемся на производстве эпоксидного ламината высшего качества, который приближается к максимально достижимым свойствам для материала, армированного стекловолокном.
Наша запатентованная технология изготовления труб и стержней обеспечивает отличное смачивание смолы, в результате чего получается композитный продукт с постоянным содержанием смолы более 30%.
Нашим самым популярным армирующим материалом для ламината является стекловолокно, обычно E Glass или S. У нас есть опыт производства эпоксидных ламинатов, армированных углеродным волокном.
Различные рисунки ткани подходят для различных применений инструментов. Наши инженеры могут предоставить рекомендации по материалам, касающимся ваших материальных потребностей.
Высококачественные композитные материалы нестандартной формы, изготавливаемые по индивидуальному заказу, изготавливаются вручную с использованием наших устойчивых к высоким температурам, не содержащих пустот систем смол и драпируемых высокотехнологичных армирующих материалов. Наши инновационные методы ручного производства практикуются и совершенствуются с 1950 года.
Обмотка нити
Наша четырехосевая намоточная машина способна производить современные композитные материалы со сложными, специально разработанными узорами армирования, такими как спиральный ветер, ветер с нулевым углом, ветер под большим углом и узор ветра из бутылки.Композитные детали длиной до пятнадцати футов и диаметром до тридцати дюймов наматываются армирующими материалами из E-стекла, S-стекла, кевлара или углеродного волокна в сочетании с нашими передовыми полимерными системами.
Смола для инъекций
Для введения смолы в армирующий материал используются высокие температуры и высокое давление. Впрыскиваемые материалы включают: эпоксидную смолу, фторуглеродную смолу, поликарбонаты, полиимиды, ароматический полиэфир и другие высокоэффективные материалы.
Разработка материалов, продуктов и процессов
«Книга Санджая Мазумдара под названием« Производство композитов »предназначена для использования в качестве учебника для студентов колледжей и / или в качестве самостоятельного занятия для инженеров и профессионалов в области композитных материалов … Книга хорошо написана и иллюстрирована, логически организована и проста в понимании. . Эта книга приветствуется в моей библиотеке и рекомендуется читателям, интересующимся производством композитов ».— Йован Мийович, профессор Политехнического университета
«… очень хорошая книга, которая дает исчерпывающий охват по многим аспектам производства композитов… Для новичка эта книга обеспечивает хорошее введение во многие аспекты производства композитов, которые должны быть известен.«
Профессор Хоа, пионер курса по производству композитов, CompositesWeek
»… замечательный контрольный список для тех из нас, кто проработал 30 лет в композитной промышленности. Это прекрасный набор знаний, который мы все можем использовать для анализа. Эта книга очень нужна в отрасли, чтобы помочь обучать новых людей ремеслу, которому большинство из нас научились в школе проб и ошибок . .. Я больше не вижу эту книгу, так как ее читают все здесь … очень впечатлен эта новая книга.«
— Джон Тернер, старший инженер-технолог Hitco Carbon Composites, Inc.,
» Подробное руководство по композитам, которое охватывает аспекты проектирования, производства, инструментов и затрат в этой сложной области для аэрокосмических и коммерческих приложений. Эта книга — отличный источник информации по всем дисциплинам, объединяющий как вводные, так и дополнительные ресурсы в одной публикации ».
— Джеральд Э. Саттон, вице-президент RTM
Advanced Technical Products, Inc., Intellitec Division, DeLand, Florida, USA
«Эта книга подходит для широкого круга пользователей. Она фокусируется на фундаментальных процессах, которые инженер или руководитель программы должен учитывать при планировании использования передовых композитов в своем проекте. Книга охватывает новейшие технологии и вопросы дизайна по мере развития науки о композитном дизайне «.
— Джон Маркс, вице-президент и генеральный директор COI Materials Inc., Сан-Диего, Калифорния, США
«… Предоставляет широкий обзор тем, связанных с производством композитов… Собирает воедино ключевые ссылки и предоставляет рекомендации, которые помогут ориентироваться в этом комплексе. поле… Охватывает многие темы, которые не часто обсуждаются в других источниках, такие как планирование производства, стоимость и переработка… »
— Тимоти Гутовски, профессор
Департамента машиностроения, Массачусетский технологический институт, Кембридж, Массачусетс, США
« Это хороший , базовые знания в области производства композитов и разработки продуктов.Главы, посвященные оценке затрат и планированию производства, очень обширны. Он содержит множество ссылок на источники более подробной информации ».
— Д-р Джон О. Тейлор, вице-президент по разработке и исследованиям, Goodrich Corporation, подразделение подшипников Glacier Garlock, Торофар, Нью-Джерси, США
Процессы | Композиты UK
Существует множество способов обработки композитных материалов FRP, и метод обработки необходимо рассмотреть на ранних этапах, чтобы решить, что лучше всего для каждого приложения.
На свойства готовой детали влияют не только свойства материалов компонентов, но и способ включения волокон. Лучшее выравнивание волокон и более высокое давление при обработке улучшат объемную долю волокна, что приведет к лучшим механическим свойствам.
Стоимость материалов, пресс-форм и оборудования, требуемые свойства готовой продукции и количество деталей, которые необходимо изготовить, будут факторами при принятии решения о процессе.
В этом разделе кратко рассматриваются некоторые способы обработки FRP, однако мы рекомендуем подкрепить эти знания дополнительным обучением по данной теме.
Мокрая укладка
Это квалифицированный ручной процесс, который требует небольших капиталовложений и широко используется для изделий небольшого объема, таких как лодки и изделия на заказ.
Арматура (тканая или рубленая) аккуратно укладывается в форму, на нее наносится матрица (смола) и распределяется валиком или кистью. Затем его оставляют для отверждения при температуре окружающей среды на несколько часов или на ночь.
Для получения хорошей отделки поверхности в форму можно добавить гелькоут до того, как в нее будет помещена арматура.Верхняя поверхность — это сторона формы, обращенная вниз.
Видео любезно предоставлено Центром материалов будущего (CFM), Университет Южного Квинсленда, Тувумба
Wet Spray-Up
Смола подается через трубку и смешивается с катализатором в ручном пистолете-распылителе. Волокно (подаваемое с бобины) измельчается в потоке смолы, когда оно распыляется на форму. Затем его оставляют для отверждения при температуре окружающей среды.
Это быстрый и простой метод, но он приводит к низкой объемной доле волокна с произвольно ориентированными волокнами.Приложения включают нестандартные детали в малых и средних объемах, такие как ванны, бассейны, резервуары для хранения.
Вакуумная инфузия
Слои сухой ткани (слоистые куски) укладываются в форму и накрываются пленкой или вакуумным пакетом, запечатанным по краям. Ткань уплотняется под вакуумом, когда смола всасывается из резервуара. Между тканью и мешком может потребоваться проточный слой, особенно для менее проницаемых тканей из углеродного волокна. Это хорошо для крупных деталей, таких как корпуса лодок, лопасти ветряных турбин или мостовые конструкции.
Трансферное формование смолы (RTM)
Сухая ткань укладывается в форму, состоящую из двух (или более) частей, которую затем закрывают в нагретом прессе. Смолу вводят под давлением (например, от 10 до 20 бар) до тех пор, пока ткань не пропитается, а инструмент не нагреется для отверждения смолы. Поток может поддерживаться вакуумом (тогда это называется вакуумным усилением — VARTM).
Повышение давления сокращает время цикла, и термин RTM высокого давления (HP-RTM) используется там, где давление составляет до 150 бар в смесительной головке и от 30 до 120 бар внутри формы, в зависимости от размера и геометрии детали. .Этот процесс требует подходящей металлической оснастки и хорошо подходит для массового производства от 100 до 10 000 единиц в год.
RTM Легкий
Вариант вакуумной инфузии и RTM, который сочетает в себе преимущества недорогих инструментов и оборудования с простым процессом пропитки путем перекачивания RTM смолы. Верхняя часть формы легкая и может быть гибкой, в некоторых случаях используется силиконовый «мешок», сделанный путем распыления силиконового компаунда на узор. Нацелен на детали с низкой производительностью.
Препрег
Ткани препрег (предварительно пропитанные смолой) разрезаются на слои (многослойные части), которые складываются, обычно вручную, и разглаживаются на поверхности пресс-формы. Это самый популярный процесс для высокоэффективных углеродных волокон в аэрокосмической отрасли и автоспорте. Некоторые производители в настоящее время используют автоматизированную укладку ленты или автоматическое размещение пакли вместо препрега, уложенного вручную.
Деталь можно отвердить несколькими способами:
Автоклав: Собранная часть упаковывается в вакуумный мешок и уплотняется под вакуумом, затем отверждается в автоклаве (сушильный шкаф) при температуре около 120–180 ° C и давлении 2–6 бар.
Духовка: Детали, помещенные в вакуумные мешки, можно вулканизировать в печи, приложив лишь вакуумное давление. Доступны низкотемпературные препреги, отверждаемые при температуре 60–100 ° C под вакуумом. Это хорошо для больших деталей, где достаточно большой автоклав не рентабелен.
Горячий пресс: Обработка в печи и автоклаве обычно занимает несколько часов. Для более короткого времени цикла слои препрега могут быть уложены в соответствующую металлическую оснастку и отверждены в прессе под высоким давлением с быстрой теплопередачей.Затем деталь может быть отверждена и извлечена из формы всего за несколько минут, но инструмент стоит дорого. Его можно подвергнуть последующему отверждению в духовке.
Обмотка накала
Жгуты волокна протягиваются через ванну с жидкой смолой и наматываются на вращающуюся цилиндрическую оправку в различных ориентациях. Это часто используется для изготовления труб и резервуаров.
Многоосевая намотка нити накала может использоваться для создания сосудов высокого давления или других форм путем наматывания жгута на оправку с фигурными концами. В этом случае оправка может оставаться внутренней облицовкой.
Формовочные массы
Формовочные смеси обладают отличными электрическими и противопожарными характеристиками, а также отделкой поверхности «Класс А» от формы. Поток в форме означает, что приспособления могут быть встроены в деталь, что снижает затраты на сборку.
Объемная формовочная масса может быть обработана путем впрыскивания в форму под высоким давлением или методом компрессионного формования. Применения включают автомобильные компоненты, электрическое оборудование, бытовую технику.
Формовочная смесь для листов изготавливается методом компрессионного формования и может использоваться в сочетании с ткаными / однонаправленными тканями или препрегами.Применения включают легкие и прочные панели кузова автомобилей, электрические шкафы, душевые поддоны.
Непрерывные процессы
Для получения продукта постоянного поперечного сечения используется несколько непрерывных процессов:
Пултрузия: Множественные ровницы и / или ткань вытягиваются с катушек через ванну со смолой в нагретую фильеру, где смола затвердевает и формируется форма. Профиль протягивается через машину и разрезается на необходимую длину автоматической пилой. Типичные изделия — это структурные профили, кабельные лотки, полосы, стержни или трубы.
Обмотка с натягом: Как пултрузия, но ровинг наматывается на затвердевший профиль, когда он выходит из матрицы. Это предотвращает расщепление профиля и увеличивает прочность на изгиб.
Сплошной лист: Кровельные фонари и плоские листы могут быть изготовлены путем распыления смолы на движущуюся несущую пленку и измельчения волокон на смоле. По мере того, как он опускается в печь, ему можно придать форму, пропустив профилированный шаблон. Затем его обрезают по длине.
Намотка непрерывной нитью: Как намотка нити накала, но для изготовления длинных труб.
Термопласты
Термопластические композиты обычно производятся путем смешивания полимерных волокон с армирующими волокнами и нагревания в форме для плавления полимера с образованием матрицы. В гибридном процессе, известном как формование, термопластичный компаунд с короткими волокнами впрыскивается в термопластический препрег в одной форме. Это может избавить от необходимости впоследствии добавлять крепления и т. Д.
Есть некоторые термопласты, которые можно обрабатывать как термореактивные пластмассы, потому что они вступают в реакцию и полимеризуются в форме, но после этого их все еще можно переплавить.