Как сделать автомобиль своими руками
Желание сделать автомобиль своими руками возникает от вдохновения и мотивации. Это может быть дорогой спортивный автомобиль, который Вы не можете себе позволить купить, либо желание создать автомобиль с собственным дизайном. Есть несколько способов реализовать свою мечту. В этой статье я расскажу о том, как сделать автомобиль своими руками. Рассмотрим как создаётся макет-основа для формовки кузова, способы изготовления кузова автомобиля, а также как можно собрать автомобиль своими руками из готового набора (kit-car).
Содержание:
Что нужно уметь, чтобы сделать автомобиль своими руками?
Процесс создания автомобиля своими руками нельзя назвать простым. Даже известные автопроизводители иногда допускают ошибки в расчётах и сборке автомобилей. Тем не менее, если есть большое желание и умение работать руками, то, используя доступные материалы и инструменты, можно сделать автомобиль самостоятельно. Кроме всего прочего, для этого требуется сильная воля и упорство, тогда можно получить впечатляющие результаты.
Базовые знания и навыки, которые необходимы это: понимание устройства автомобиля, умение работать с металлом, стекловолокном и шпаклёвкой, умение пользоваться сварочным аппаратом, базовые знания электрики автомобиля.
Некоторым вещам, которые Вы не умеете делать, придётся научиться в процессе создания автомобиля. Многое можно изучить из руководств и информации из Интернета. На этом сайте есть статьи об автомобилях, созданных любителями, не обладающих большим опытом и обучавшихся всему в процессе постройки самодельной машины. Вот два примера: статья “о создании драгстера, стилизованного под Ferrari Enzo” и вторая статья “о создании автомобиля Scorpione”. Иногда будет разумно прибегнуть к помощи специалистов. Подумайте, что Вы сможете сделать сами, а для какого этапа лучше привлечь другого мастера. Многим хочется думать, что они первоклассные мастера на все руки и всё смогут сделать самостоятельно, без привлечения помощи. Это, порой, является причиной, почему проект затягивается на слишком долгое время. Ведь то, что может сделать опытный профессионал за день, любитель может провозиться неделю, а то и дольше. К примеру, если Вы не умеете красить, то можно самому подготовить кузов к покраске, а на саму покраску отвезти машину к маляру. Либо обтягивание салона обивочным материалом можно доверить специалистам в этом деле. Таким образом, общий процесс создания автомобиля не будет казаться нереальным.
Мастерская и инструменты
Нужно располагать тёплой мастерской с достаточным свободным пространством.
Изготовление автомобиля своими руками требует наличия необходимых инструментов. Специальные инструменты и станки позволяют сделать работу быстрее и проще, но без них можно обойтись.
Вот основные необходимые инструменты, которые нужны при создании автомобиля своими руками:
- Необходимо иметь хороший верстак с большими тисками.
- Полный набор ручных инструментов
- Дрель, а лучше установку для вертикального сверления
- Болгарка
- Сварочный аппарат (лучше полуавтомат)
- Компрессор. Для покраски и для функционирования пневмоинструментов.
- Краскопульт
- Зажимы разных размеров (для крепления деталей перед сваркой)
- Киянки разных размеров и форм, молотки и поддержки для формовки металла (в случае создания кузова из листового металла).
- Станок «английское колесо» и листогибочный станок (для более лёгкой формовки листового металла). Как уже упоминалось ранее, без этих станков, молотков и киянок можно обойтись, даже если делать кузов из листового металла. Разные методики создания кузова мы рассмотрим в этой статье ниже.
Вот пример автомобиля, кузов которого сделан из алюминия на станке “английское колесо”. Подробнее о мастере и его автомобилях можете почитать в статье “Крис Рунге и его автомобили из полированного алюминия”.
Как самому сделать автомобиль с нуля?
Изготовление автомобиля с нуля предполагает создание всех его компонентов и правильная их компоновка. Это очень непростой процесс и может затянуться на неопределённо долгое время. К примеру, американец Кен Имхофф делая копию автомобиля Lamborghini Countach, максимально приближенную к оригиналу, изготавливал практически всё с нуля, даже колёсные диски. Будучи профессиональным формовщиком металла, он потратил 17 лет, чтобы полностью завершить проект. В интервью он признался, что это было не выгодное занятие и было для него как интересная игра. Чаще всего, при создании автомобиля своими руками, в качестве основы берётся существующий серийный автомобиль и переделывается. Это самый реальный путь сделать автомобиль своими руками – сделать самостоятельно каркас, кузов и интерьер, а все остальные компоненты взять готовыми, у другого автомобиля или нескольких автомобилей. Точно также делают небольшие производители автомобилей по всему миру в последние 50 лет или больше.
Нужно обзавестись необходимыми руководствами по автомобилю, который будет использоваться в качестве донора, чтобы понимать устройство всех его узлов (двигателя, рулевого управления, подвески, тормозной системы, электрики).
Создание собственного дизайна кузова
Многие автолюбители мечтают об обладании одного единственного автомобиля с необычным дизайном, автомобилем своей мечты. Можно спроектировать и сделать такой автомобиль самостоятельно. Начало планирования дизайна и строительства автомобиля начинается с идеи. Дизайн может быть индивидуальным, либо комбинировать в себе существующие формы, взятые с других автомобилей. К примеру, это может быть передняя часть, похожая на одну машину, а задняя — на другую. Когда образ вашего автомобиля будет придуман, то его нужно нарисовать. Существует множество графических компьютерных программ, которые помогут спланировать и спроектировать автомобиль. Решив, как будет выглядеть ваш автомобиль, нужно понять, какая колёсная база под него подойдёт. Нужно выбрать донора, похожего по параметрам, чтобы колёсная база соответствовала, или же её нужно будет изменить.
Изготовление полномасштабного макета-основы для создания кузова
Для создания кузова нужно сделать макет-основу. По этой основе можно будет подгонять листовой металл (формуется станком “английское колесо” или молотками и киянками и на каждом этапе прикладывается к макету), либо сформовать стекловолокно, пропитанное полиэфирной смолой. После формовки кузова, макет-основа никак не участвует в конструкции автомобиля, а готовые панели крепятся к структурным элементам конструкции автомобиля.
Для проектирования может использоваться компьютер (программа CAD или Alias) с дальнейшей распечаткой полномасштабных чертежей на плоттере. Существуют и уже готовые шаблоны популярных автомобилей в электронном виде, которые можно купить или найти в свободном доступе в интернете. Также есть американские компании, которые могут изготовить шаблоны для макета-основы любого автомобиля на заказ.
Виртуальная схема макет-основы для создания копии кузова Mercedes-Benz SLR 300.Можно использовать и старый метод создания макета-основы, без применения компьютера. В нём есть свои преимущества. Старый метод создания макета-основы применялся кузовостроителями много лет. Для этого должен быть нарисован рисунок всех сторон автомобиля (см. иллюстрацию) со шкалой, которая расчерчена на квадраты.
В переводе на реальный размер, расстояние между линиями составляет 10 дюймов (25 см). По квадратам будет проще контролировать размер и форму при изготовлении макета. Далее, чтобы получить трёхмерную модель рисунков, нужно сделать маленький макет автомобиля. Макет можно сделать из глины для лепки или пластилина. Во время работы с глиной, Вы, приближаясь к финальной форме, скорее всего, многое измените в дизайне. Так происходит, потому что модель предстаёт перед Вами в другой перспективе. После изменений в дизайне, нужно внести изменения в чертёж.
Далее слепленная модель разрезается на поперечные сегменты, которые очерчиваются по контуру (см. фото), и по ним изготавливаются шаблоны из картона. Так как обе стороны автомобиля симметричные, то шаблоны на вторую сторону можно делать только по одной стороне. Каждый шаблон должен быть пронумерован в соответствии с его расположением.
Следующим шагом нужно увеличить эти шаблоны до полного размера. Для увеличения и переноса на бумагу используется проектор. Если нет проектора, то можно увеличить шаблоны, копируя их на большую бумагу, соблюдая пропорции (по квадратам). Потом нужно сделать полноразмерные шаблоны. Для создания окончательных полномасштабных шаблонов лучше всего подходит берёзовая фанера 12 мм, но можно использовать и другой материал (рассмотрим ниже). Теперь нужно собрать все шаблоны воедино, чтобы получить макет-основу для формовки кузова.
Полномасштабный деревянный макет-основа для создания копии кузова Mercedes-Benz SLR 300.Примерка сформованного листового металла на деревянном макете-основе концепта спортивного автомобиля.Для изготовления макета-основы могут использоваться разные материалы:
- Фанера
- МДФ (более дешёвый вариант фанеры)
- Проволока или арматура
- Монтажная пена+ картон (подходит для создания кузова из стекловолокна)
- Пластилин или глина для лепки
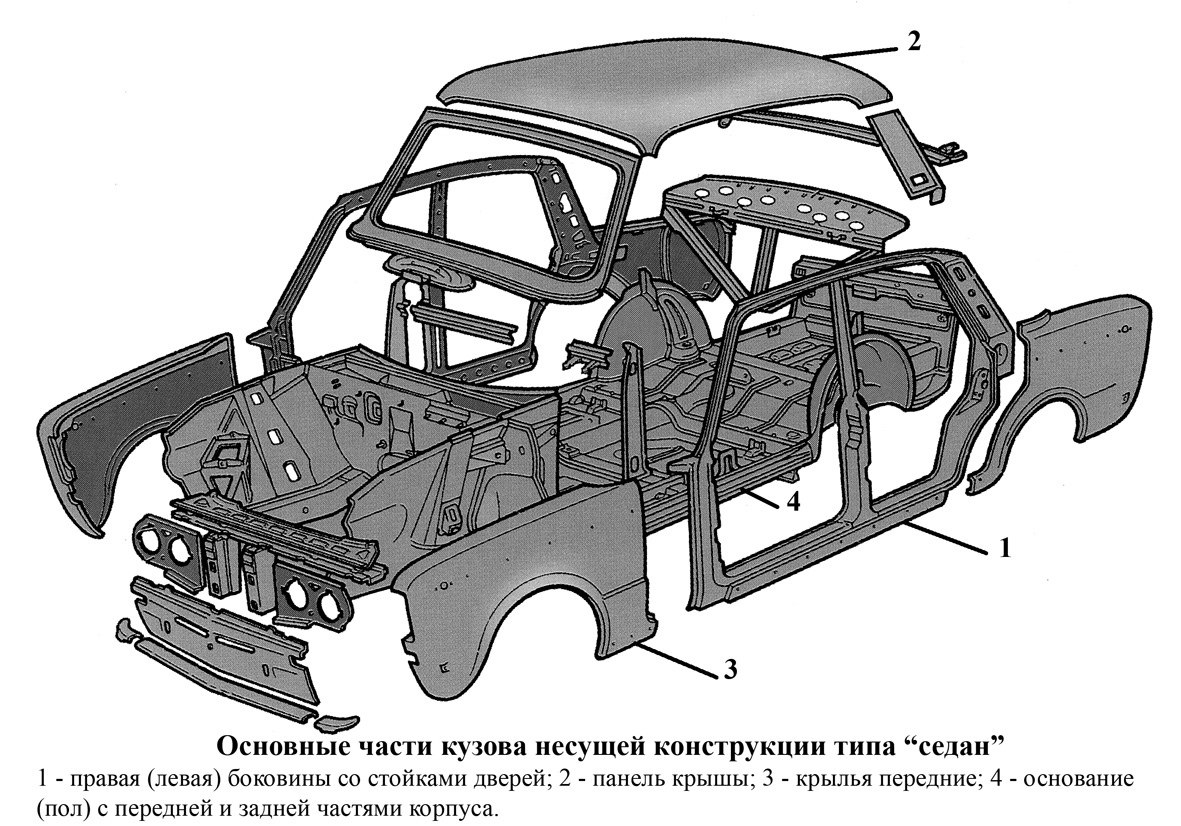
Разные материалы для создания макета-основы имеют разные особенности. Дерево даёт хорошую визуализацию во время процесса изготовления конструкции, но горит, когда на нём варятся панели кузова. Открытая конструкция (каркас из проволоки) хорошо гнётся в разные изгибы кузова, и дают лёгкий доступ с обратной стороны, для воздействия молотком и поддержкой на листовой металл. Картон и монтажная пена, создающая основной объём, хорошо подходят для создания кузова из стекловолокна (этот процесс мы рассмотрим ниже). Глина для лепки в этом процессе удобна, но самая дорогая вещь. Для создания полномасштабного макета потребуется более 200 кг глины. Стоимость пластилина или глины окупится, если её использовать повторно.
После того, как конструкция 3D-модели автомобиля готова, она будет служить формой для формовки листового металла для кузова автомобиля, либо кузова из стекловолокна.
Способы создания кузова автомобиля своими руками
Вот базовые способы, при помощи которых в наши дни можно сделать автомобильный кузов:
- Каркас + облицовка из формованного листового металла.
- Создание кузова без силового каркаса, с использованием более толстого металла для панелей.
- Создание панелей из отдельных сегментов, свариваемых вместе.
- Формовка из стекловолокна.
- Комбинация способов
Каркас и облицовка (панели из листового металла)
Использование киянки и деревянного штампа, сделанного из массива дерева, для формовки панели кузова.Это традиционный метод изготовления кузова, использовавшийся ещё при постройке карет. Базовый каркас кузова делается из дерева или металла. Далее листы облицовки крепятся на этот каркас. Кузов такой конструкции чаще всего применяют частные автомобилестроители, так как его легко спроектировать, построить и ремонтировать при повреждении (в отличие от кузова “монокок”, который считается более продвинутым, но применяется реже). Каркасом является так называемая пространственная рама (space frame). Кузов с такой рамой использует множество сегментов профильного металла (обычно стальных), соединённых вместе, чтобы сформировать прочную конструкцию. Прочность достигается за счёт поперечин. Нужно определить нагрузки, которые будут воздействовать на кузов и, в соответствии с этими нагрузками, нужно создать необходимые усиления профильными трубами. С трубами, имеющими квадратное сечение проще работать, чем с круглыми. Их проще стыковать друг с другом. Круглые трубы сложнее соединять, но они более прочные. При формовке листового металла используются киянки, молотки, поддержки, деревянные штампы, станок “английское колесо”.
Панели из толстого металла без пространственной рамы
При этом методе не используется силовой каркас (пространственная рама), на которую навариваются листы. Вместо этого применяются листы большей толщины, которые прочнее обычного листового металла. Жёсткость конструкции придаёт взаимное крепление панелей между собой. Такие кузова крепятся на шасси и должны иметь отдельные структурные элементы (не несущие большой нагрузки), на которые крепятся листы. Таким способом часто делают кузов для хот-рода. Недостатком такого способа является сложность формовки панелей из толстого металла и большой вес автомобиля.
Создание панелей из отдельных сегментов, свариваемых вместе
Панели для создания кузова могут создаваться из нескольких сегментов, сваренных вместе. Для этого, в качестве основы, используется проволочный каркас (для контроля и удержания формы), на который и приваривают все части панели. В зависимости от размера и формы, к обратной стороне панели могут быть добавлены усилители. Такой способ позволяет обойтись без формовки сложных панелей при помощи специальных формовочных станков.
Формовка кузова из стекловолокна
Спортивные автомобили с кузовом из стеклопластика появились ещё в конце 1951 года.
Chevrolet Corvette 1953 года выпуска был первым серийным автомобилем с кузовом из стекловолокна.
Chevrolet Corvette 1953 года выпуска стал первым серийным автомобилем с кузовом из стеклопластика. Человек демонстрирует лёгкий вес кузова.Стеклопластиковый кузов может быть сформован целиком, одной цельной частью.
Преимуществами кузова из стекловолокна являются лёгкий вес, дешевизна при производстве в небольших количествах, не подверженность коррозии. Недостатками являются низкое визуальное качество получаемой поверхности, требующей дальнейшего выравнивания, стекловолокно не может играть роль силовой конструкции, способной выдержать значительные нагрузки, поэтому должно устанавливаться на каркас.
Для создания макета в сегодняшние дни популярно применение картона (в качестве основного макета-основы, создание которого описано выше) со строительной пеной (для заполнения промежутков между картонными шаблонами) и дальнейшая доводка неровностей шпаклёвкой.
Существует два способа сформовать панели из стекловолокна. Оба способа требуют создания полномасштабного макета (как было описано выше).
- Кузов формуется напрямую, сверху макета. Такая формовка потребует дальнейшего выравнивания шпаклёвкой, так как поверхность получается грубой.
- Поверхность макета идеально выравнивается и даже окрашивается. С него делается форма из полиэфирной смолы и стекловолокна. Далее полученная форма усиливается. Её внутренняя часть получается очень гладкой и может использоваться для создания копий панелей из стеклопластика с гораздо более ровной поверхностью, чем при первом способе. Если требуется создавать несколько копий одинаковых деталей, то лучше создать такую форму. В остальных случаях, стекловолокно формуется поверх полноразмерного макета напрямую.
Выбор донора
Автомобиль-донор должен подходить по геометрическим параметрам к вашему проекту. Лучше в качестве донора выбрать надёжный и простой в обслуживании автомобиль, запчасти на который стоят не очень дорого. Чтобы сэкономить, можно, в качестве донора, купить машину с повреждённым кузовом.
Иногда, при создании автомобиля своими руками, используются двигатели от мощных мотоциклов. Они сочетают лёгкий вес и приличную мощность при маленьком объёме.
Кит-кар
Это ещё один способ сделать автомобиль своими руками. Кит-кар (от англ. kit-car) – это автомобильный набор, который продаётся производителем, как комплект запчастей и содержит подробную инструкцию по сборке, а покупатель потом его собирает самостоятельно. Обычно основные механические системы, такие как двигатель и трансмиссия берутся от автомобиля-донора или же покупаются новыми у отдельных производителей.
Кит-кары появились с ранних лет автомобилестроения. В 1896 году англичанин Томас Хилер-Вайт (Englishman Thomas Hyler-White) разработал дизайн для автомобиля, который можно было собирать дома.
В течение 1970‑х годов кит-кары имели кузова, стилизованные под спортивные автомобили, которые были спроектированы, чтобы прикрепляться на раму VW Beetle. Это было популярно, так как кузов этого автомобиля мог легко отделяться от шасси, после чего оставались все механические компоненты, прикреплённые к раме. По этой причине, VW Жук стал одним из самых популярных доноров всех времён. Примеры такой переделки включают Bradley GT, Sterling и Sebring, которые изготавливались тысячами и многие по-прежнему сохранились.
Современные кит-кары представляют собой реплики известных и дорогих автомобилей. Реплики имеют внешний вид, идентичный оригиналу, но кузов сделан из стекловолокна и полиэфирной смолы, вместо листового металла, как оригинальный кузов. Места крепления капота, дверей и крышки багажника, усиливаются металлическими вставками, заламинированными в стекловолокно и смолу.
Кит-кары могут быть разной комплектации. Больше распространены кит-кары, которые предназначены только для замены кузова конкретного донора (Re-body Fiberglass Kit). К примеру, Vaydor Body Kit, производит кузова из стекловолокна для Infinity G35 coupe 2003–2007 года. Часть кузова срезается и устанавливается каркас, подходящий по форме к кузову из стекловолокна. Такая переделка требует меньше технических знаний, так как вся техническая часть остаётся от работающего серийного автомобиля.
Кузов компании Veydor на базе Infinity G35 coupe.Преимущество изготовление автомобиля из набора kit-кара в том, что до вас это уже много раз делали и могут помочь советом. К тому же, сам производитель всегда может оказать поддержку в создании автомобиля. Если же изготавливаете эксклюзивный автомобиль с нуля самостоятельно, то вам остаётся надеяться только на себя.
Подготовка автомобиля к покраске и покраска
По подготовке к покраске есть множество видео и текстового материала. Покраску можно перепоручить другим мастерам, либо сделать самому. Качество покраски на 95% зависит от правильной, качественной подготовки. Краска не скроет неровности и несовершенства поверхности, а лишь подчеркнёт их.
Регистрация самодельного автомобиля
Многое зависит от страны, где вы живёте и требований к автомобилям при регистрации. Если же Вы не собираетесь ездить на автомобиле по дорогам общего пользования, то с этим проблем не возникнет.
В России регистрация самодельного автомобиля реальна. Для этого необходимо пройти целый ряд процедур. Машину нужно будет сертифицировать в лаборатории «Ростехрегулирования». Нужно будет предоставить техническую документацию и чертежи самодельного автомобиля. Конструкция машины должна соответствовать установленным техническим требованиям. Эксперты обратят внимание на габариты автомобиля, рулевое управление, эффективность тормозной системы, работу светотехники. Также будет проверено содержание вредных веществ в выхлопе. После прохождения всех процедур экспертизы владелец самодельной машины получит одобрение (документ). Это даёт возможность получения техпаспорта. Далее следует ещё ряд формальностей до окончательной регистрации автомобиля. При удачном завершении регистрации, владелец автомобиля получает свидетельство о регистрации транспортного средства, где в графе марка авто числится «Самодельный».
Печатать статью
Ещё интересные статьи:
Большой секрет перекупщиков: как распознать битую машину? | 74.
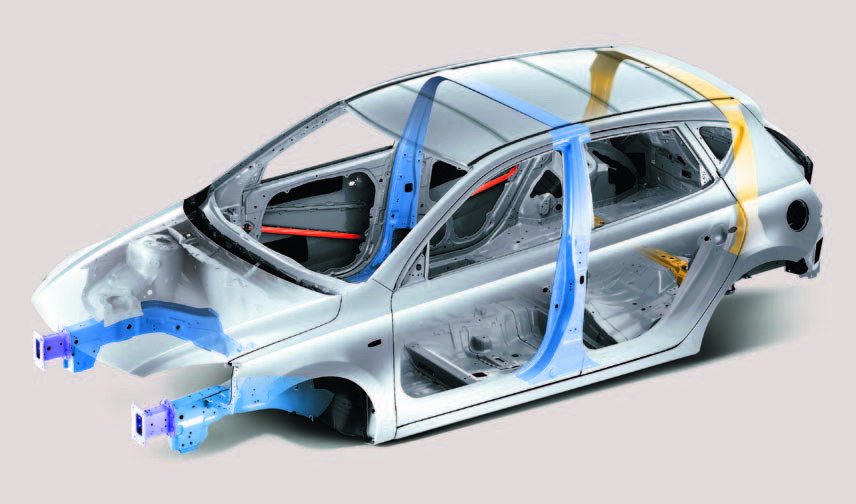
Подготовка поверхности к окраске в малярном цехе
После восстановления геометрии детали отправляются в малярный цех, а здесь – множество своих тонкостей. Поверхность готовят к покраске, грунтуют, тем временем колеровщики подбирают цвет, смешивают краски. После нанесения эмали кузов отправляется в сушильную камеру. А затем – в арматурный цех на финальную сборку.
Работа по восстановлению кузова требует большой скрупулезности, а хороший кузовщик или маляр – это почти человек искусства.
Хуже битой…
Самое худшее, что может случиться с покупателем пробежного авто, – это приобретение залогового автомобиля. Прецедентов полно. Человек покупает автомобиль, ставит на учет, ездит год-другой, а затем приставы изымают машину, поскольку она, например, находится в залоге по автокредиту или другому долгу, который не был выплачен в срок предыдущим хозяином. Крайним остается последний владелец – автомобиль конфискуется через суд и продается с аукциона в пользу банка. Шансы вернуть хотя бы деньги есть, но препон на пути будет немало. Мошенникам, продавшим залоговый автомобиль, грозит уголовное наказание, но пострадавшему от этого не легче: как правило, деньги ему не возвращают.
Парадокс в том, что гарантированных способов защититься от такой ситуации практически нет: единого реестра залоговых машин не существует, равно как и особых отметок в свидетельстве о регистрации или ПТС. При покупке автомобиля в кредит ПТС обычно остается в банке, но владельцу не составляет труда получить копию в ГИБДД по причине якобы утери. Некоторые банки то ли по умыслу, то ли «случайно» принимают на хранение копии ПТС.
Как снизить риски? Стопроцентно надежного пути нет, но подозрения должна вызывать машина, которая приобретена недавно и тут же выставлена на продажу; у которой вместо ПТС – его дубликат, выданный в связи с утерей (смотрите графу «Особые отметки»). Попросите у владельца документы об оплате, по которым можно судить, был ли автомобиль приобретен в кредит или за наличный расчет (впрочем, это не мешает перезаложить машину позже для получения нового кредита). И разумеется, не игнорируйте внутреннее чутье: если продавец кажется подозрительным, иной раз лучше отказаться от покупки, чем лишиться и денег, и машины.
Алгоритм поиска следов кузовного ремонта
- Проверяем, снимался ли лючок бензобака. Если да, уточняем у владельца, для какой цели.
- Ищем на кузове сколы и микроцарапины: если машина в эксплуатации несколько лет, но кузов идеальный, возможно, его недавно перекрашивали.
- При хорошем освещении ищем несовпадение цвета между отдельными деталями, переходы оттенка или цветовые пятна, для чего обходим автомобиль кругом.
- В подозрительны местах при взгляде вдоль поверхности определяем наличие шагрени. (микронеровностей ЛКП), проверяем, не «играет» ли поверхность на свету.
- Внимательно изучаем равномерность и симметричность кузовных зазоров.
- Проверяем легкость и звук закрывания всех дверей, крышки багажника и капота.
- Оцениваем качество сварных швов (точек) и аккуратность нанесения герметика.
- Проверяем крепежные элементы: болты, заклепки, пистоны. Нет ли поврежденных, замененных, нестандартных или неокрашенных деталей? Не болтаются ли обшивки интерьера?
- Особое внимание уделяем скрытым полостям, например, подкапотному пространству, дну багажного отсека и обратной стороне задних крыльев.
- Ищем наличие следов от полировочной пасты или краски на неокрашиваемых деталях, особенно, на резиновых уплотнителях.
В случае сомнений требуем инструментальной диагностики автомобиля. В идеале стоит проверить геометрию кузова, функциональность ходовой части, состояние тормозной системы и рулевого управления, продиагностировать двигатель и проверить информацию о сработке систем безопасности.
Выбрать добротный подержанный автомобиль вы можете с помощью сервиса «Автообъявления» на нашем сайте.
Благодарим специалистов отдела трейд-ин и кузовного цеха компании «Форд Центр Восток» за помощь в подготовке материала.
Подробнее об услуге Trade In.
Самодельные автомобили теперь можно ставить на учет в ГИБДД — Российская газета
Теперь самоделки тоже имеют право на получение в ГИБДД регистрационных номеров, а соответственно и право самостоятельно передвигаться по дорогам.
Для регистрации конкретного автомобильного чуда необходимо обратиться в орган сертификации, представить туда «изделие», получить документ о соответствии транспортного средства предъявляемым техническим требованиям. А затем с полученной бумагой идти в ГИБДД и ставить машину на учет.
Постановление о 50 лошадях
Любовь к созданию многочисленных машин по собственным проектам появилась у нас не от хорошей жизни. В Советском Союзе не было и речи о выпуске автомобилей под запросы конкретного потребителя — хватило бы сил дать рынку массовые модели. Поэтому энтузиасты из подручных материалов и своими руками делали машины, отвечающие требованиям жизни.
Из трех старых, убитых собирали одну живую. На селе из легковых кузовов делали грузовые. Создавали амфибии, чтобы преодолевать болота и другие водные препятствия. Увеличивали грузоподъемность, удлиняли кузова — ведь грузовики не продавались в личное пользование.
Были и эстеты, которых не устраивала сама форма серийного легкового автомобиля. Они создавали автоварианты — от прилизанных спорткаров до самых фантастических и иногда нелепейших конструкций. Все это показывалось на выставках и на вполне законных основаниях ездило по дорогам.
В советские годы самоделки не то чтобы поощрялись, но во всяком случае не запрещались. Первые серьезные ограничения появились в 80-х годах. А именно — ограничения по мощности (50 лошадиных сил на тонну), по габаритам (4,7 метра по длине и 1,8 метра по ширине). Оставалась одна лазейка, которой и пользовалось большинство. Ведь регистрировали технику не только в ГАИ, но и в Ростехнадзоре. Например, трактора. Внедорожники же в те времена вполне подходили под эту категорию. А требования к самоделкам в Гостехнадзоре были значительно мягче. В результате с 1993 по 1995 год было зарегистрировано наибольшее количество автомобилей ручной сборки.
Годы полного запрета
2005 год оказался черным для самоделок — их регистрацию и в ГАИ, и в Ростехнадзоре запретили вовсе. Верховный суд РФ аргументировал запрет тем, что надо разработать четкие требования к «самодельной» продукции. Хотя настоящая причина, видимо, крылась в борьбе с новым явлением на авторынках — в продаже так называемых конструкторов. Суть рыночного бума на «конструкторы» была проста: чтобы уйти от налогов, машину (например, японскую) сначала ввозили в Россию в виде запчастей, затем собирали ее, а регистрировали как самодельную.
Однако запрет этот, к сожалению, коснулся и авторов настоящих отечественных самоделок. Их-то творческий энтузиазм не иссяк! Доказательство тому — ежегодные выставки «Автоэкзотика», где самоделки представляются в огромном количестве. Однако в большинстве случаев это машины без номеров, привезенные на эвакуаторе и права на жизнь на дорогах не имеющие. Хотя как раз на дорогах иные самоделки могли дать фору многим серийным автомобилям.
Оковы рухнули
Новые требования, которые определяют порядок сертификации, наконец, приняты и утверждены. Приказ Ростехрегулирования, утвердивший изменения N1 «Правил по проведению работ в Системе сертификации механических транспортных средств и прицепов» вступил в силу в январе этого года.
Итак, как же поставить самоделку на учет в новых реалиях? Для начала потребуется обратиться в орган сертификации. Их не так уж и много по стране. Ближайший к вам можно выбрать из списка, который опубликован на сайте Рос техрегулирования. (адрес сайта: http://www.gost.ru/wps/portal/)
Оценивать самоделку теперь будут по упрощенной схеме. Как «транспортное средство, производимое малыми сериями». Минимальное количество автомобилей в малой серии — 1 штука.
Есть тут и небольшая хитрость, с помощью которой государство спасло себя от ввоза «конструкторов». Количество автомобилей в малой партии необходимо указывать. Понятно, что тот, кто собирает для себя, больше одного автомобиля одного типа делать не будет. А тому, кто попытается лукавить с государством и под заказ привозить машинокомплекты, занимаясь практически промышленной сборкой, по новым правилам сертификации работать будет невыгодно. Ведь количество машин в партии проверяется. Повторить процедуру сертификации нельзя.
Правда, и полученное одобрение типа не имеет срока действия. Оно заканчивается тогда, когда вступают в силу новые технические требования. Например, с нового года вступили в силу требования по экологичности Евро 3. Значит, именно с этого года прекратило действовать и одобрение типа. Ведь одобряло оно нормы Евро 2.
По правилам ООН
Новые требования к самодельным машинам, естественно, не ниже, чем к выпускающимся серийно. Тут послаблений нет, а главное, самоделки должны соответствовать правилам Европейской экономической комиссии ООН. И хотя малые партии будут сертифицировать по усеченному списку требований, все равно это серьезная процедура.
Согласно документу, проверяться на соответствие требованиям будут травмобезопасность рулевого колеса, тормозные свойства, места крепления ремней безопасности и сами ремни, стекла, зеркала заднего вида и их установка, установка устройств освещения и световой сигнализации, управляемость и устойчивость, внутренний шум, содержание вредных веществ в салоне, и, конечно, содержание вредных веществ в выхлопе. Это — выборка для легковых автомобилей.
приятный момент
Есть в новых требованиях и пункт, приятный для изобретателей. Машины на испытаниях теперь увечить не будут: «В отношении единичных транспортных средств проводятся испытания, не вызывающие их повреждения. Допускается замена испытаний, вызывающих повреждения, экспертной оценкой конструкции».
После всех этих экспертиз, если машина удовлетворяет требованиям, хозяин, он же изобретатель, получает одобрение типа. С этим документом — прямой путь в подразделение ГИБДД по месту жительства, где выдадут паспорт транспортного средства и поставят автомобиль на учет. Данные об одобрении типа заносятся в ПТС.
Конечно, вряд ли эти нововведения вызовут бурный всплеск в самодеятельном конструировании новых и необычных типов автомобилей. Но во всяком случае нашим Кулибиным жить станет теперь легче.
Самые известные самоделки последнего времени: слева — ISV, получивший приз как самый экзотичный автомобиль года на выставке «Автоэкзотика», справа — автомобиль «Агата», построенный членами московского Фонда авторских автомобилей.
Вопросы от клиентов и ответы на них
На ваши вопросы отвечает Евгений Павлович Митрохин, старший специалист по кузовному ремонту. Опыт работы на этой должности: 17 лет. Самый старший и профессиональный сотрудник в нашем центре.От чего зависит цена ремонта кузова в мастерской?
Разумеется, стоимость зависит от марки вашего авто, точнее от того, насколько дорогие запчасти к нему необходимы. Также значительную роль играет степень повреждения кузова или попросту объем работы, которую необходимо будет сделать специалистам в сервисе. Также значимые аспекты при определении сервисом цены услуг это популярность СТО, в которое вы обратились.
Сколько может длиться кузовной ремонт при средней степени повреждения?
Процесс ремонта и восстановления автомобильной поверхности может занять неделю-две в мастерской. Если вы решили осуществить это самостоятельно, тогда придется уделить автомобилю где-то месяц внимания.
Должны ли сотрудники автосервиса помыть и почистить машину, если она была отдана им для починки кузова?
Так делают далеко не везде, а должны бы. Прежде чем машина вернется к своему законному владельцу, сотрудниками СТО она должна быть приведена в полагающий вид, даже если привезли ее не в самом чистом состоянии. Деньги за такую услугу, как правило, не берутся.
Может ли кузовной ремонт каким-то образом улучшить общее состояние авто или ухудшить его?
Ремонт кузова действительно содействует улучшению работы авто. Качественно сделанный ремонт кузова обеспечивает ходовые параметры, а также повышает безопасность вождения.
Насколько должен быть поврежден кузов, чтобы его невозможно было восстановить?
Конкретного определения нет. Просто в некоторых случаях количество вмятин и царапин превышает все нормы, тогда в мастерской вам сразу объявят — требуется замена кузова.
Как удалить царапины с поверхности кузова?
На сегодняшний день большой популярности приобрел знаменитый и известный почти всем маркер для удаления царапин с авто. Но на самом деле не все так прекрасно и хотя мало понимающие в автомобильном деле женщины с радостью покупают такие «подарочки» своим мужьям, те не приходят в дикий восторг от такого презента, ведь уже после первой попытки исправить какую-то даже крошечную царапину понимают бесполезность такой покупки. Лучше всего обращаться к профессионалам.
Где чаще всего появляются повреждения после столкновения бампером?
Как ни странно, но на крыше. Поэтому если вы поймали ворону и зацепили чье-то авто передней частью своей машины, прежде всего осмотрите область столкновения, а потом проанализируйте состояние крыши, там могут появится трещины краски, которые в итоге прибавят общему процессу ремонту немало проблем и затруднительных моментов.
Что значит если при столкновении на красочном покрытии автомобиля лишь образовались трещины, а больше никаких повреждений не замечено?
В таком случае практически стопроцентная гарантия, что внутри авто тоже повреждено. Треснувшая в нескольких местах краска, которая непосредственно до момента столкновения была нормальной, практически всегда обозначает повреждение внутренних деталей машины.
Как произвести диагностику состояния кузова, не имея навыков и умений?
Ответ один — никак. Если не умеете анализировать состояние автомобиля и чинить его, то на ремонте кузова уж точно учиться не стоит. А уж если знаниями о ремонтных работах обладаете весьма глубокими, то диагностировать состояние авто все равно лучше доверьте профессионалам.
Визуальный осмотр — эффективный ли метод диагностики?
Разумеется, что нет. Простым осмотром в таком деле явно не обойтись. В некоторых автомастерских используется высокотехнологичное оборудование, чтобы максимально точно определить отклонение каждой детали и иметь возможность отремонтировать все до мелочей.
Преимущества ремонта в автосервиса — есть ли они?
Безусловно да. Давайте посчитаем минусы и плюсы, возможно так будет понятней. Из минусов в голову приходит лишь цена, конечно же это дороже, чем делать все самому, но теперь переходим к плюсам, которых, кстати, значительно больше. Для начала стоит сказать о том, что ремонт будет выполнен профессионально, машина будет качественно отремонтирована и покрашена. По вашему желанию сотрудники мастерской могут дать рекомендации касательно, скажем, покраски вашей машины самостоятельно, так сказать на будущее. А также к плюсам относится гарантия, которую выдают большинство сервисов.
Возможно ли отреставрировать деформированный кузов или нужно непременно менять его?
В некоторых случаях деформация может быть несущественной, тогда можно обойтись просто рихтованием и корректировкой повреждений, а уже потом осуществляется покраска. Во всех остальных случаях следует менять поверхность на новую.
В случае замены кузова важно ли, чтобы детали были того же производителя, что и автомобиль, то есть оригинальными?
Особо острой необходимости в этом нет и если уж никак не получается найти именно таких деталей, можно взять другие от другой фирмы. Но желательно все же запчасти приобретать той же марки, то и машина. Тогда работа вашего четырехколесного друга будет более исправной.
Оклейка кузова глянцевыми пленками в Москве
Телефон: +7 (495) 323-93-99
Ежедневно с 9:00 до 20:00
Если хочется существенно изменить
внешний вид автомобиля, придав ему индивидуальности или просто изменив цвет, то
вовсе не обязательно становиться в очередь на покраску. Есть более быстрое,
недорогое и несложное решение – оклейка глянцевыми плёнками.
При этом глянцевые плёнки способны сделать внешний вид кузова даже более индивидуальным и оригинальным, чем покраска! Виниловому полотну вовсе не обязательно быть просто равномерно окрашенным. Различные текстуры (например, «карбон»), фактуры, эффект «хамелеон» или металлик – всё это способно сделать эстетику авто действительно необычным и впечатляющим.
И при всех этих преимуществах глянцевые плёнки обладают ещё одним немаловажным достоинством – они защищают «родное» лакокрасочное покрытие кузова от негативных внешних факторов. Например, от царапин из-за пыли, летящего гравия, веток кустов и деревьев во дворах, когтей дремлющей на тёплом капоте кошки или ключей в руках недоброжелателя.
5 преимуществ оклейки автомобиля глянцевыми плёнками
Мы используем наиболее высококачественные глянцевые плёнки из винила и других полимерных материалов производства компаний 3M, Oracal, KMPF и Hexis. Они известны превосходной цветопередачей, высокой надёжностью и долговечностью. Решения от этих производителей обладают сразу несколькими важными достоинствами:
- Адекватная цена. Стоимость оклейки – даже всего кузова – значительно ниже, чем перекраски. Можно переклеивать винил хоть каждые несколько месяцев, постоянно меняя цвет и внешний вид, без ущерба для бюджета;
- Быстрое нанесение. Винил наклеивается за один день, без разборки кузова и других сервисных операций. Автомобиль готов к эксплуатации сразу после нанесения, не нужно ждать высыхания;
- Обратимость процесса. Если текущая эстетика надоела, хочется вернуться к заводскому цвету автомобиля или поменять её на покрытие какого-нибудь другого оттенка – это также можно сделать за один день. Винил легко снимается, не повреждая ЛКП;
- Защита лакокрасочного покрытия. Покрытие способно предотвратить появление царапин и трещин на кузове. Кроме того, оно защищает от контактов с агрессивными химикатами, такими как противоснежные реагенты;
- Надёжность и долговечность.
Цвета и фактуры устойчивы к действию ультрафиолета, поэтому сохраняются на длительное время. Полимерный клей надёжно фиксирует покрытие на кузове, не пропуская влагу и пыль, и не допуская отсоединения. Даже через годы плёнка и автомобиль будут выглядеть так, будто они только что с завода.
При наклеивании мы учитываем все конструкционные и аэродинамические особенности кузова автомобиля, поэтому плёнка ложится ровно и аккуратно – как второй слой лакокрасочного покрытия.
Глянцевая плёнка для маскировки повреждений ЛКП
Глянцевые плёнки можно использовать не только для придания свежего и индивидуального внешнего вида автомобилю, но и для маскировки повреждений ЛКП. Например, потёртостей после ДТП или масштабных царапин, оставшихся после того, как дети разрисовали машину куском кирпича.
Глянцевая плёнка аккуратно
ложится поверх повреждённого лакокрасочного покрытия, скрывая царапины,
трещины, следы коррозии и другие дефекты. И при этом она дополнительно защищает
детали кузова. Повреждения ЛКП могут стать очагами коррозии, особенно при
контакте с едкими реагентами – а виниловое полотно предотвратит разрушительное
воздействие химикатов и влаги.
Наши специалисты способны подобрать плёнку аккуратно в тон остальному ЛКП машины, так что оклейка не будет заметна.
Профессиональная оклейка автомобилей глянцевой плёнкой
В студии автодетейлинга «А1 Авто» мы проводим профессиональную оклейку автомобилей высококачественной глянцевой плёнкой. Используем только надёжные материалы, современные технологии и профессиональный подход. Хотите ли вы освежить вид машины или скрыть повреждения ЛКП – мы сделаем это за один день.
Запишитесь на профессиональную оклейку автомобиля прямо сейчас!
Телефон: +7 (495) 323-93-99
Ежедневно с 9:00 до 20:00
Что нужно знать о владельцу об особенностях покраске кузова автомобиля, чтобы быть уверенным в качественном конечном результате
Покраска автомобиля – сложный технологический процесс, который включает в себя множество стадий, начиная от первого осмотра и оценки ремонта и заканчивая финишной полировкой и нанесением защитного покрытия на отремонтированный кузов.
Среди наиболее распространенных причин, по которым автовладелец задумывается о необходимости покраски своего автомобиля можно выделить следующие:
- Различного рода дорожно-транспортные происшествия, после которых требуется кузовной ремонт и без покраски уже не обойтись.
- Выявление очагов коррозии на кузове. Для их устранения требуется зачистка поврежденных деталей и последующая их покраска.
- Наличие сколов, царапин и вмятин на кузове машины, которые рано или поздно появляются при длительной эксплуатации автомобиля.
- Желание владельца поменять цвет или сделать аэрографию.
Независимо от того что выступает в качестве причины, процесс покраски автомобиля сложный и финансово затратный. Прежде чем передать свою машину в мастерскую необходимо обладать минимальным набором знаний, чтобы быть уверенным, что покрасочные работы выполнены качественно и деньги потрачены не зря.
Виды покраски
В зависимости от технического состояния машины покраска бывает локальная, частичная и полная. Если повреждена одна деталь или небольшое количество элементов кузова требует замены, то используют частичную покраску. Наиболее часто локальной покраске подвергаются следующие детали машины: бампер, крылья, пороги, двери. Основная сложность при частичной покраске – соблюсти совпадение цвета окрашенного элемента кузова с остальными. Преимущества такого способа покраски – это значительная экономия средств, т.к. окрашивается только место повреждения или отдельный элемент кузова. При соблюдении всех требований к технологическому процессу в результате следы ремонта не заметны и покрашенный элемент ничем не отличается от остального кузова.
Если вследствие ДТП или коррозии требуется заменить большую часть кузова, то используют полную покраску и полировку авто. Ее же применяют при ремонте старых авто, когда частичная покраска большого количества отдельных элементов не позволяет добиться точного совпадения с исходным цветом машины. Стоимость полной покраски автомобиля определяется индивидуально и зависит от сложности повреждений. Полная покраска автомобиля, выполненная по всем правилам – эта это один из самых трудоемких и длительных процессов в кузовном ремонте.
Этапы покраски автомобиля при ремонте
Независимо от того выполняется полная или только частичная окраска существует определенный порядок действий при ремонте автомобиля связанный с необходимостью его подготовки и процедуры самой покраски.
Первый этап – предварительный осмотр машины и выявление всех дефектов на частях кузова, которые подлежат покраске. Чем детальнее будет определен форт работ, поставлены и согласованы задачи по покраске выбранных элементов, тем проще будет оценивать качество выполненных работ и регулировать претензии в будущем.
Второй этап подготовки самый длительный – подготовка машины к покраске. Для качественной покраски авто вмятины должны быть устранены. На этом этапе в зависимости от исходного качества окрашиваемых деталей (глубина сколов, размер коррозии, степень деформации ремонтируемых поверхностей и т.д.) требуется работа нескольких специалистов. Последовательно выполняется ряд действий:
- Разборка поврежденного элемента
- Рихтовка или восстановление правильной геометрии при наличии исходной деформации
- Шпатлевание и доводка элемента кузова до нужной формы.
Все это необходимо, если окрашиваемый элемент имеет мелкие неровности, царапины. Существует большое разнообразие марок шпатлевок от ведущих мировых производителей, но в основном все они относятся к категории полиэфирных шпатлевок. Это продукты, которые состоят из двух компонент: шпатлевочная масса на основе ненасыщенных полиэфиров и различные наполнители и добавки. Специалистами в работе одновременно может применяться несколько видов шпатлевок в зависимости от характера неровностей. В случае устранения незначительных дефектов на большой площади используется напыляемые шпатлевки, которые широкими слоями наносятся с помощью краскопульта. Для устранения глубоких вмятин используются шпатлевки усиленные стекловолокном, с ними за один проход получается слой большей толщины. Наиболее часто мастера используют универсальные шпатлевки.
4. Грунтование элемента для устранения всех мелких дефектов.
Если предыдущий этап иногда можно пропустить, если устанавливаем новую деталь кузова, то грунтование строго обязательно. Цвет грунтовки должен соответствовать итоговому цвету машины. Например, если машины красится в светлый или серебристые цвета, то и грунт необходимо подбирать светлым, если же окончательный цвет авто темный, то можно использовать грунты черного цвета. После грунтования считается, что пройдены все этапы подготовки авто к покраске.
5. Подборка краски.
Когда владелец автомобиля желает полностью изменить цвет машины, то на выбор краски влияют только личные предпочтения по тому или иному цвету. Совершенно иные требования, если окрашиваеются отдельные детали, которые должна соответствовать первоначальному цвету кузова автомобиля. В таком случае подбираем цвет с учетом его интенсивности и яркости. В этом помогают компьютерные технологии и стереотипная таблица расцветок, благодаря которым определяется нужный номер оттенка цвета машины.
Выбранная для покраски эмаль помимо декоративных требований (совпадение по цвету и блеску) должна обладать такими физико-механическими свойствами как твердость, эластичность, прочность. Существующие на рынке автомобильные эмали условно разделяются на три группы: алкидные, меламино-алкидные (МЛ), акриловые.
Представители первой групп эмалей используются с 1950-х годов. Такой длительный срок применения связан с их основными преимуществами: невысокая стоимость, простота применения в работе, стойкость к химическим и физическим воздействиям у готового покрытия. Ключевым недостаток выступает – длительный срок высыхания окрашенного изделия. Это частично решается за счет использования в процессе окраске отвердителя.
Вторая группа автомобильных эмалей не нуждается в дополнительных веществах, покрытие на их основе получается достаточно твердым, но при этом сохраняет эластичность. Но высыхают они при температуре более 100 градусов, что делает невозможной работу с данными эмалями без специальных окрасочных камер.
Автоэмали третьей группы обычно наносятся в два слоя. Цвет покрытию придает первый, базовый слой. В отличии от первой группы при использовании акриловых эмалей расход материала гораздо меньше за счет большего количества сухого остатка.
При работе с этими эмалями можно производить сушку при 80 градусах, но при этом окрашенные поверхности будут стойкими не только к атмосферным воздействиям, но и отличаются масло- и бензостойкостью. Повышенная износостойкость покрытия, удобство применения в работе способствуют широкому их применению в покрасочных мастерских.
Качественное покрытие этими эмалями получается только при соблюдении технологических процессов, особенно соблюдение времени по обязательной межслойной выдержке.
6. Подготовка автомобиля к покраске: оклейка авто и защита неокрашиваемых поверхностей.
Третий этап – сам процесс покраски авто, который включает нанесение краски на ремонтируемую деталь/кузов и лакирование. На этом этапе применяется краскопульт для покраски авто.
Для того, чтобы получить требуемое качество окрашиваемых поверхностей всего кузова или отдельных его элементов необходимо все это производить в покрасочной камере. В таком случае достигается максимально качественный результат, который приближен к заводской окраске машины. В покрасочной камере соблюдается ряд важных условий:
1. Равномерность освещения. Наличие специального освещения повышает качество работ по покраске.
2. Хорошая вентиляция и система фильтрации. При окраске кузова автомобиля критически важен уровень пыли в воздухе. Если покраска осуществляется в обычном ремонтном боксе, как бы не было там чисто, но необходимого уровня по очистки воздуха не достичь. Как результат неровности и шероховатости свежеокрашенных поверхностей кузова.
3. Герметичность. Стенки камеры сделаны из жаропрочного материала, что позволяет достигнуть нужной температуры для быстрой и качественной сушки окрашиваемых поверхностей.
Заключительный этап включает в себя сборку кузова автомобиля и финишную полировку.
Если в процессе ремонта производилась полная или частичная окраска кузова, то необходимо провести тщательный осмотр окрашенных деталей на предмет выявления возможных дефектов, чтобы в дальнейшем не заниматься полировкой царапин авто своими руками.
Причиной некачественной окраски могут выступать разные факторы. Это может быть проведение работ не в специализированных помещениях, применение дешевых низкосортных автоэмалей, не знание или нарушение технологии как подготовки поверхности к покраске, так и процедуры самой окраски детали или кузова в целом. Если были соблюдены все технические условия то у автомобиля: цвет окрашенных деталей совпадает с заводским оттенком, отсутствует шагрень (неровности или «апельсиновая корка» лакокрасочного покрытия), нет всевозможных вкраплений и наплывов в покрашенных частях кузова.
Специалисты Центра кузовного ремонта компании Волга-Раст выполнят качественную частичную или полную покраску авто в Волгограде по приемлемой цене. В работу по покраске принимаются любые иностранных автомобилей (кроме китайских). Качество работ подтверждается регулярным обучением сотрудников и следование строгим технологическим стандартам ремонтных работ мировых автомобильных брендов.
Записаться на обслуживание и уточнить всю необходимую информацию можно по телефону: +7 (8442) 55-22-55
Собрать автомобиль за 46 секунд!
На заводе компании GAC Motor в Ичане (Китай) новый автомобильный кузов сходит со сборочной линии каждые 46 секунд. Это стало возможным благодаря внедрению инновационных роботизированных решений ABB по сборке кузова.
Знаете ли вы, что мировой рекорд в спринте на 400 метров составляет 43,03 секунды, а французский пловец Амори Лево (Amaury Leveaux) преодолевает 100 метров за 44,94 секунды? В то время как в динамичном мире спорта рекорды ставятся за несколько секунд, поставить рекорд в производстве крайне сложно. Именно поэтому автомобильный завод компании GAC Motor в Ичане так уникален. На умной фабрике сборка кузова автомобиля занимает всего 46 секунд, тем самым компания ставит новую планку всему мировому автомобильному производству. Это достижение стало возможным благодаря комплексу передовых технологий, включая различные высокопроизводительные роботизированные решения от ABB.
Линия сборки автомобильного кузова оснащена рядом гибких производственных решений, отличающихся максимальной производительностью, эффективностью и качеством. Среди них легко перенастраиваемые система сборки GateFramer и подвижная платформа ABB FlexTrack, а также линии для вклеивания и сборки деталей автомобиля.
Задача
Завод GAC Motor в Ичане, в который были вложены большие инвестиции – предприятие мирового уровня с технологиями автоматизированного производства последнего поколения. Для достижения такой цели, как сборка автомобильного кузова за 46 секунд, завод с 2018 года тесно сотрудничает с ABB в проектировании производственных линий.
«46 секунд – лимит времени, который мы до сих пор не осмеливались покорить. Известно, что скорость основных производственных линий в мире около 60 секунд, а самые быстрые могут достигать показателя в 51 секунду», – отметил Джэнгао Дун (Zhengghao Dong), глобальный менеджер ABB по решениям для сборочных линий.
Ключевая задача состояла в том, чтобы сварить 72 прихваточных шва за 46 секунд, при этом на каждый сварной шов уходило бы 4-5 секунд, а также гарантировать, что швы сделаны с высокой степенью точности и прочности. Вместе с этим конфигурация решений должна отвечать требованиям заказчика по гибкому совместному производству нескольких моделей на различных платформах и по переключению производственных линий между работами над различными моделями автомобиля, не затрагивая стандартный производственный цикл.
Решение
После недель тщательного анализа данных и планирования ABB решила отойти от проектировочного ограничения по использованию 14 роботов в своей системе сборки GateFramer и добавить в нее четыре дополнительных робота, которые помогли бы GAC достичь скорости производства в 46 секунд. Систему оснастили 8 высокопроизводительными роботами IRB 6700 и 10 роботами IRB 6650s, которые способны выполнить установку элементов автомобильного кузова за 10 секунд и сварить 72 кузовных шва всего за 16 секунд.
В 2019 году завод в Ичане установил оснащенную 18 роботами систему ABB GateFramer и начал серийное производство автомобильных кузовов. Среди линий по сборке кузовов, реализованных компанией ABB по всему миру, в этой системе задействовано наибольшее количество роботов, и у нее самая высокая скорость производства.
В отличие от традиционных линий по сборке кузовов, которые необходимо разрабатывать под индивидуальные условия каждой модели автомобиля, у системы сборки GateFramer стандартизированная конструкция. Она позволяет собирать до 6 моделей автомобилей на одной и той же производственной линии без ее остановки. Производители могут просто переключаться между сборкой разных моделями, меняя порядок секций, где крепятся детали для той или иной модели.
Помимо основной линии с зоной сварки на заводе в Ичане установлена 96-метровая подвижная платформа ABB FlexTrack для передвижения кузова автомобиля по производству. Конвейеру с сервоприводом нужно всего 6 секунд, чтобы переместить кузов автомобиля с одной позиции на другую. Скорость его движения – 1500 мм/с – помогает достичь показателя 46 секунд на один производственный цикл.
Автомобильные детали и элементы салона, в том числе кресла и колеса собираются двумя роботами IRB 6700 на линии основной сборки. Еще четыре робота IRB 6700 вклеивают лобовые и задние стекла.
Результат
Благодаря высокой скорости и надежности роботов ABB производственная мощность завода в Ичане составляет 200 тысяч автомобилей в год. За одну смену с производственной линии сходит 500 готовых кузовов автомобилей. Так как качество выпускаемой продукции и производственная эффективность полностью отвечает ожиданиям GAC Motor, в июне 2019 года компания начала производить на заводе в Ичане среднеразмерный седан GA6. В этом году GAC Motor в полной мере воспользуется возможностью начать сборку новых моделей без дополнительных ресурсов и запустит производство модели GS4, вслед за которой начнет выпускать новый электромобиль.
www.abb.com/robotics
Как переоборудовать и построить новые кузова Chevy ’57 для развлечения и прибыли
Я хожу на выставку SEMA (Speciality Equipment Market Association) в Лас-Вегасе с 1981 года. В процессе я видел более замысловатые выхлопные патрубки и выбитые колеса, чем я мог бы сосчитать на своем ноутбуке. Но я продолжаю возвращаться, потому что всегда нахожу что-то новое.
В этом году я заметил, что продавцы продают полностью новые кузова для старых автомобилей. Один стенд на выставке продавал свежие кузова Мустангов и Камарос 60-х.Другой предлагал новенькие кузова Chevy 57 года выпуска.
Это были не копии из стекловолокна, а изделия из штампованной стали, состоящие из панелей кузова, которые взаимозаменяемы со стандартными частями. Они готовы сочетаться с рамой, трансмиссией и подвеской, чтобы создать совершенно новый автомобиль.
Chevy 57-го года производится компанией EMI в Стерлинг-Хайтс, штат Мичиган, в 60 милях от нашей штаб-квартиры в Анн-Арборе, которая была основана в том же году, когда появился знаменитый Chevy. Вернувшись с выставки, я посетил компанию, чтобы увидеть, как она умудряется производить эти тела в небольших количествах по разумной цене.
Оказывается, EMI — Experi-Metal, Inc. — специализируется на производстве небольших партий металлических корпусных деталей. 150 сотрудников EMI построили первые прототипы нынешних Ford Mustang и F-150, а также Pontiac Solstice. «Мы можем сделать белое тело целиком из математической модели за четыре месяца», — говорит генеральный директор Джерри Кинг.
EMI также производит восстановленные детали из листового металла для автомобилей от Ford Coupe 32-го до Chevy 57-го. Фактически, одна из причин, по которой компания решила сделать кузов 57-го года полностью, заключалась в том, что она уже производила около половины кузовных панелей в качестве запасных частей.
Эти панели производятся тем же способом, что и производственные кузовные детали: путем помещения плоских стальных листов между двумя металлическими штампами, имеющими форму конечной детали, и сжатия штампов вместе с усилием в несколько тысяч фунтов.
Основное различие между Chevy и прототипами заключается в конструкции штамповочных штампов. Штампы для прототипов начинаются с баз данных САПР или электронных представлений формы и размера кузова автомобиля, созданных при проектировании транспортных средств на экранах компьютеров.Для Chevy ’57 EMI пришлось создать собственную базу данных CAD, используя цифровые датчики для измерения контуров реальных панелей кузова Chevy.
Из этой базы данных сотрудники EMI определяют, как деталь должна быть проштампована. Это означает, что нужно выяснить, в каком направлении должны двигаться штампы и сколько ударов потребуется. Это не только искусство, но и наука, сочетающая в себе опыт — Кинг работает в области штамповки листового металла 34 года — а также специализированные компьютерные программы, такие как Dynaform, которые помогают определить, будут ли плоские стальные листы складываться или рваться по мере того, как они образуются умирает.
После определения формы штампов используется фрезерный станок с компьютерным управлением для вырезания копий штампов из гигантских блоков пенопласта — для переднего крыла может потребоваться матрица длиной восемь футов, шириной пять футов и два фута. глубокий.
Эти копии из пенопласта помещаются в большие стальные рамы, где вокруг них набивается формовочный песок (песок с примесью клея). Затем пену удаляют, оставляя полость, заполненную расплавленным металлом. Металлом для штампов, используемых на автомобильных заводах, является сталь, которая обеспечивает прочный и долговечный штамп.Но для прототипов и кузова Chevy EMI использует кирксит, цинковый сплав, который легче обрабатывать, чем сталь, и разливается только при 800 градусах, а не при 2800 градусах, необходимых для стали. Для более крупных инструментов требуется до 30 000 фунтов расплавленного кирксита.
После затвердевания металла песок удаляется, а штамп для чернового литья возвращается на фрезерный станок, который обрезает его до окончательного контура. Каждая деталь из листового металла нуждается в головке и головке, которые прикреплены к гигантским штамповочным прессам.Самый большой EMI может сжимать инструменты вместе с силой в 2000 тонн или четыре миллиона фунтов, которая создается гидравлически. Такой пресс стоит около 3 миллионов долларов и возвышается на 30 футов над цехом, а также более чем на 20 футов ниже.
После штамповки плоской стали до окончательной формы деталь измеряется электронными датчиками, чтобы убедиться, что она имеет правильную форму. Металл всегда имеет упругую отдачу, а это означает, что он не является точной копией формы в штампе.Это учтено в конструкции штампов, но обычно требуется корректировка методом проб и ошибок, прежде чем детали станут идеальными.
А поскольку киркситовые штампы изнашиваются быстрее, чем стальные, для обеспечения точности деталей проводятся частые проверки у мастера. При тщательном контроле и периодическом восстановлении инструмента набор штампов может штамповать несколько тысяч деталей.
Излишки материала удаляются с готовых штамповок с помощью компьютеризированной лазерной обрезной машины, которая продается за 1 доллар.2 миллиона. После выполнения любых других операций по гибке и перфорации детали готовы для сварки в готовое тело.
EMI выполнила этот процесс для примерно 200 деталей, чтобы создать Chevy ’57. Единственная не переделанная деталь — это капот / противопожарная стена. Эту деталь сложно штамповать, и, по данным EMI, ее достаточно легко получить из различных источников. Используя оригинальный капот — даже тот, который требует некоторой реставрации — EMI экономит деньги, а также позволяет классифицировать весь кузов как восстановленный, а не как полностью новый автомобиль.
Стоимость кузова в белом цвете — 34 500 долларов. Превращение одного в полноценный автомобиль будет стоить от 70 000 до 120 000 долларов, в зависимости от того, сколько экзотических деталей вы используете. Когда один из этих автомобилей будет собран на современном шасси, мы будем первыми в очереди на испытания.
Этот контент создается и поддерживается третьей стороной и импортируется на эту страницу, чтобы помочь пользователям указать свои адреса электронной почты. Вы можете найти больше информации об этом и подобном контенте на пианино.io
Моделирование нескольких тел, часть 3: Как создать несколько тел
Сделать несколько тел из одной детали очень просто. Вот несколько способов сделать это:
Disjoint Solids
Когда вы создаете твердые области, которые не соприкасаются друг с другом, они называются областями . Технически в одном теле может быть несколько областей. Итак, нарисуйте прямоугольник, выдавите его до твердого тела. Нарисуйте еще один прямоугольник и выдавите еще одно твердое тело в той же части, которое не касается первого тела, и у вас есть 2 области, одно тело.Я как бы забиваюсь об этом, потому что меня это сбивает с толку, поскольку я слишком много лет работал с другой системой. Из-за этой концепции «непересекающихся твердых тел» вы должны быть более осторожны при использовании термина «мульти-тела» в Solid Edge.
Если вы хотите скачать часть, использованную для создания этого изображения, она прикреплена к этому сообщению с именем mbm1.par. Это очень просто, но вы должны легко увидеть, что было сделано, и поиграть с этим, не боясь сломать что-нибудь важное.
На изображении выше курсор находится над Design Body 1 на панели Обработки контуров, поэтому две области, составляющие это тело, выделены оранжевым. По умолчанию они будут прозрачно-серыми, потому что они неактивны. Design Body 2 — это отдельная область и активное тело. Я создал запись Design Body 2 на панели Обработки контуров, используя инструмент Add Body, показанный справа.
Таким образом, при выдавливании непересекающихся эскизов создаются сплошные области, пока вы не воспользуетесь командой «Добавить тело».Это первый и самый простой способ создать несколько областей / тел в Solid Edge.
Вставить копию детали
Следующий инструмент, о котором стоит поговорить, — это команда «Вставить копию детали». Это позволяет вам вставлять одну деталь в другую, где все, что отображается во второй части, является одним элементом. Мне непонятно, почему эта команда отображается в группе «Буфер обмена» на вкладке «Главная», но вы найдете ее именно там. Интерфейс можно настраивать, поэтому, если это действительно вас оскорбляет по какой-то причине, вы можете поместить его в другое место, которое имеет для вас больше смысла.
Когда вы используете эту функцию в синхронном режиме, она не ассоциативна. При первом использовании вы получите такое сообщение:
Я видел много людей, которые игнорируют подобные сообщения или считают, что никакие сообщения, отправляемые программой, не являются полезными. Не будь одним из таких людей. По крайней мере, прочтите сообщение, прежде чем судить о его полезности. Это довольно ясно. Поэтому, если вы внесете изменения в исходную модель, вставка копии детали не обновится. Иногда это именно то, что вам нужно, а иногда нет.Если вам нужна функция, которая будет обновляться с изменениями в исходном файле, переключитесь в упорядоченный режим и используйте таким образом Вставить копию детали.
Диалоговое окно «Параметры копирования детали» помогает вставить существующую деталь в новую. Существующая часть, которую я называю «родительской», может быть многотельной или многозональной. Например, я использовал часть mbm1.par, используемую в приведенном выше примере, в качестве родительской части для вставки в новую часть с помощью команды Insert Part Copy.
Чтобы использовать этот инструмент, просто создайте новую деталь или откройте существующую деталь.Эту часть я называю «дочерней частью». Затем нажмите «Вставить копию детали» на вкладке «Главная» в группе «Буфер обмена». Подтвердите сообщение, описанное выше, если вы находитесь в синхронном режиме.
Затем появится диалоговое окно справа. Это дает вам множество вариантов.
В раскрывающемся списке «Элемент семейства деталей» можно выбрать один конкретный элемент из семейства деталей родительской детали. Это может быть конкретный размер или версия с определенными функциями или без них.
«Копировать как тело проекта» вставляет тела родительской детали как тела проекта.
«Объединить твердые тела» объединит тела родительской детали с телами дочерней детали.
«Зеркальное тело», конечно, дает вам деталь, противоположную оригиналу, и вы даже можете использовать инструмент «Масштаб» для равномерного или неравномерного масштабирования.
«Flatten» предназначен для корпусов из листового металла.
Перемещение тел в синхронном режиме довольно просто.Просто выберите тело на панели Обработки контуров и используйте штурвал, чтобы переместить тело в новое место. Намного проще, чем другие программы, которые я использовал.
Вырезание тела
Я использовал mbm1.par для создания этого разреза. Сначала я активировал Design Body 1, затем нарисовал на нем прямоугольник и выдавил часть прямоугольника над блоком, чтобы сделать сквозной разрез. Это не создает другое тело, это создает область . Опять же, если вы понимаете эту концепцию «регионов», прошу прощения за это подчеркивание, я делаю это в первую очередь потому, что мне все еще трудно с этим.Отсюда мне непонятно, как разделить области на тела, если у вас есть необходимость в этом.
Split
Split, на мой взгляд, один из наиболее полезных инструментов MBM. Разделение позволяет разделить твердое тело на несколько тел с плоскостью, другим твердым телом или поверхностью. Это очень удобно. Одним из недостатков инструмента является то, что он, кажется, работает только с одним телом за раз (вы не можете разделить несколько тел, хотя, опять же, вы можете разделить несколько областей в одном теле).
Divide
Я слышал об этой функции «разделения». Похоже, что он был спрятан в ST5 и, возможно, удален в ST6. Я не могу найти его в интерфейсе настройки. Похоже, что его заменила функция публикации с несколькими телами. Может здесь кто поправит / подтвердит. Трудно не быть экспертом . В любом случае Divide кажется устаревшей функцией.
Multi-Body Publish
Multi-Body Publish — это своего рода конец процесса MBM.Эта функция позволяет вынести каждое тело в отдельные файлы деталей. Это также объединит все эти отдельные части в сборку. Отлично. Это отличный инструмент, он делает то, что нужно, прост в использовании и не требует пояснений.
разнесенных видов деталей с несколькими телами за 6 шагов
При проектировании в SolidWorks иногда может быть полезно создавать детали, которые имеют более одного твердого тела, в таких приложениях, как сварные детали, листовой металл или инструменты для литья под давлением.Также может потребоваться показать, как эти части сочетаются друг с другом, в разобранном виде. Хотя можно сохранить отдельные тела как отдельные файлы деталей в сборке и выполнить там разнесенный вид, может быть проще и быстрее выполнить разнесенный вид в многотельной детали. Эта функция была представлена в SolidWorks 2012.
Этот процесс, описанный в шагах ниже, аналогичен созданию разнесенных видов со сборками.
1. Создайте новую конфигурацию
Управляйте разнесенными видами, помещая их в их собственную конфигурацию.Щелкните вкладку «Конфигурация»> щелкните правой кнопкой мыши ниже> щелкните «Добавить конфигурацию»> «Добавить имя» «Разнесенный вид»
2. Создать вид с разнесенными частями
Перейдите в меню «Вставка» и нажмите «Разнесенный вид». Вы также можете найти разнесенный вид с помощью поиска команд в верхнем правом углу окна SolidWorks.
3. Шаги разнесения
Откроется Менеджер свойств разнесенного вида. Выберите тела, которые нужно взорвать, затем перетащите маркер манипуляции в желаемом направлении.Вы можете выбрать одно или несколько тел для взрыва на определенном этапе. Эти шаги добавлены в левой части под названием «Разнесение шагов». В разделе «Настройки» перечислены выбранные тела, направление и расстояние. Чтобы добавить дополнительные шаги, просто выберите разные тела и перетащите.
4. Автоматическое размещение компонентов
При выборе параметра «Автоматическое размещение твердых тел после перетаскивания» все выбранные компоненты будут размещены на равном расстоянии друг от друга.
5. Редактировать шаги разнесения
Щелкнув правой кнопкой мыши на предполагаемом шаге и выбрав «Редактировать шаг», вы сможете внести изменения в выбранные компоненты, их направление и расстояние. Компоненты могут быть добавлены или удалены. Направление можно изменить, выбрав стрелку и нажав кнопку реверса. Вы можете выровнять маркер перетаскивания по определенному объекту, щелкнув правой кнопкой мыши маркер перетаскивания и выбрав: «Выровнять по», «Выровнять по началу компонента» или «Переместить к выделенному».Выровняв ручки перетаскивания, выберите стрелку направления. Вы можете указать другое расстояние рядом с полем «D1». По завершении нажмите «Применить», а затем «Готово». Вы можете продолжать редактировать существующие шаги или добавлять новые. По завершении щелкните зеленую галочку.
6. Готовый вид с разнесенными частями
Для перехода между свернутым и разнесенным состояниями перейдите на вкладку Configuration Manager и разверните конфигурацию «Разнесенный вид»; внутри — это производная конфигурация, которая содержит разнесенный вид с его шагами разнесения.Щелкните правой кнопкой мыши полученную конфигурацию, чтобы свернуть или разнести деталь. Редактировать функцию приведет вас к Менеджеру свойств разнесения. Параметр «Свернуть элементы» просто сворачивает дерево конфигурации.
L имитации:
У этой команды есть несколько ограничений. Вы не можете повторно использовать разнесение нескольких тел в разнесенном виде сборки, так же как вы можете повторно использовать разнесенный вид узла. Кроме того, вы не можете анимировать разнесение или свертывание или сохранить его как файл.avi файл. Наконец, нельзя удерживать alt для перемещения и выравнивания стрелок перетаскивания, как при разнесении сборки.
преобразование твердых тел в детали в solidworks
Я хочу создать твердое тело… 2. нажмите «Преобразовать в листовой металл» 3. выберите грань, которая будет фиксированной плоскостью развернутого листа, или существующее твердое тело можно преобразовать в тело из листового металла с помощью команды «преобразовать в листовой металл». »И« вставить сгибы »… толщина тела из листового металла на уровне моделирования детали обновит определение оболочки.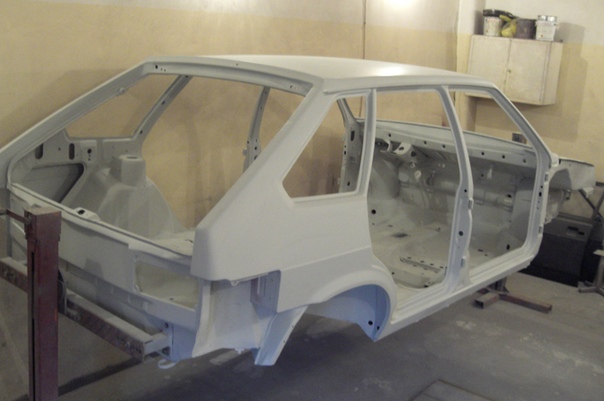
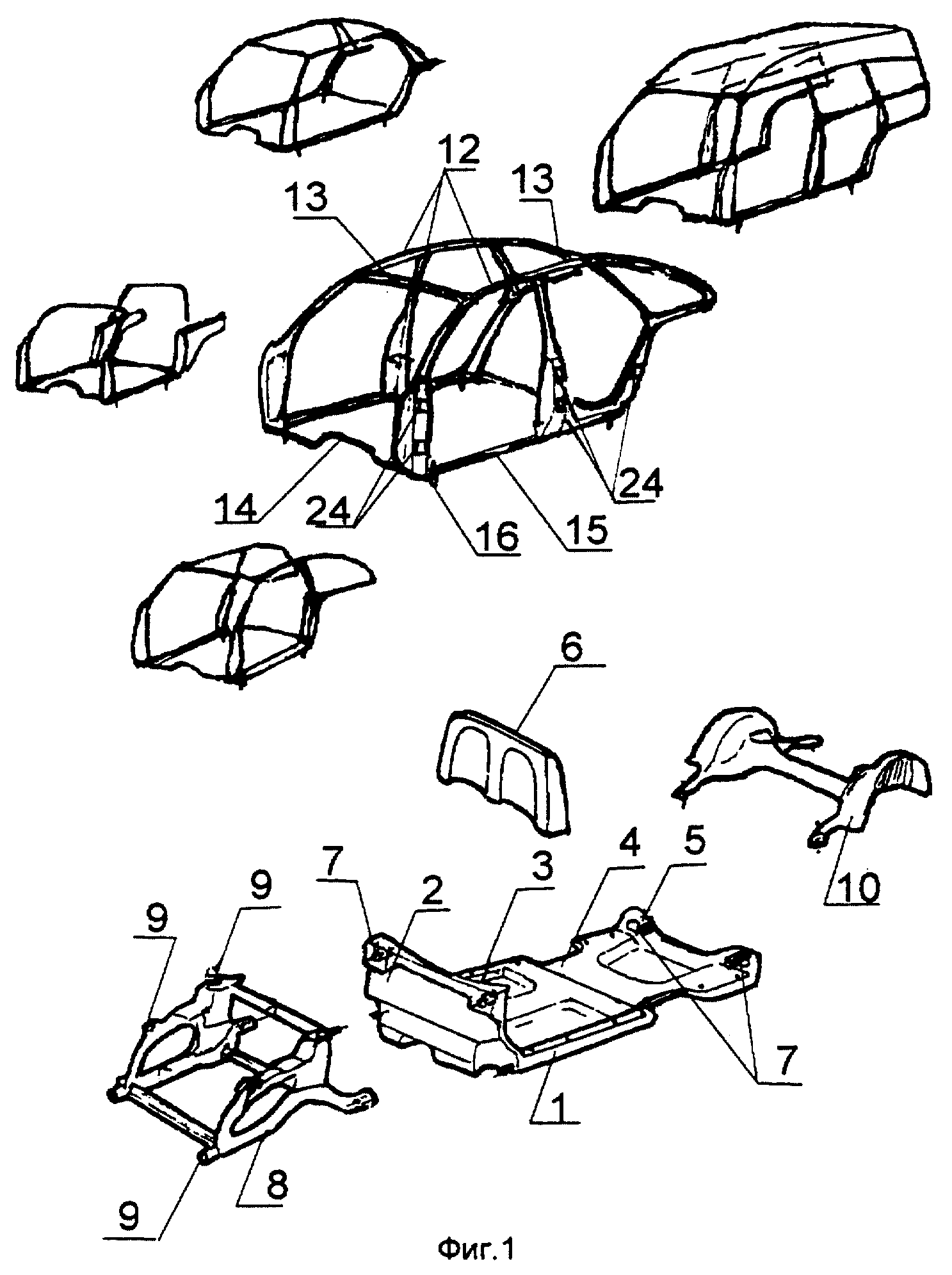
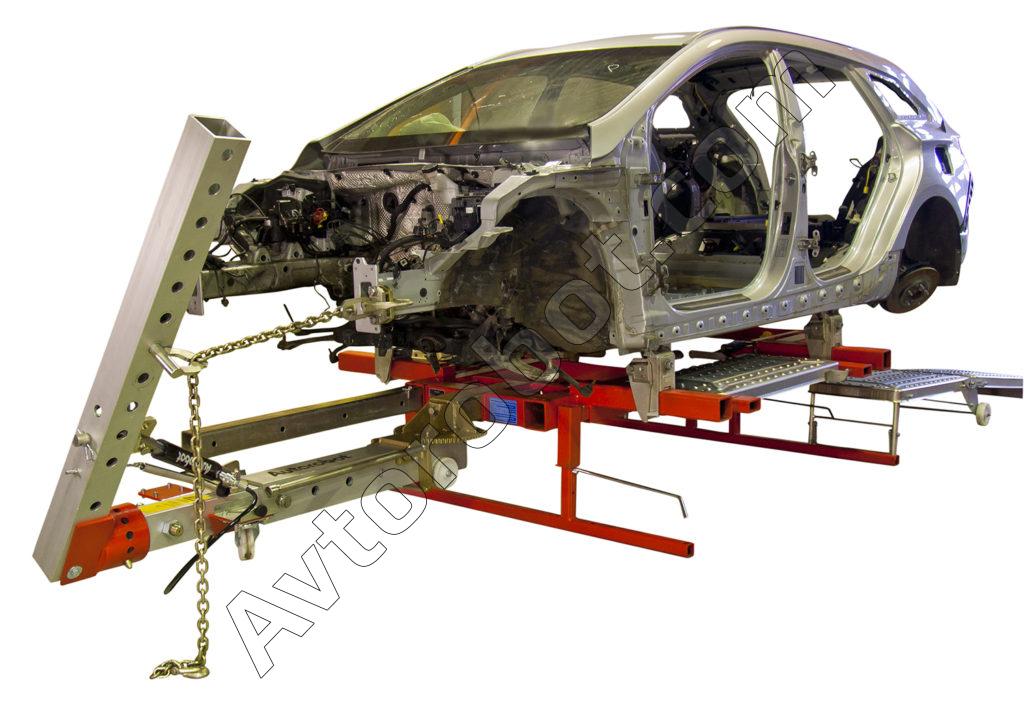






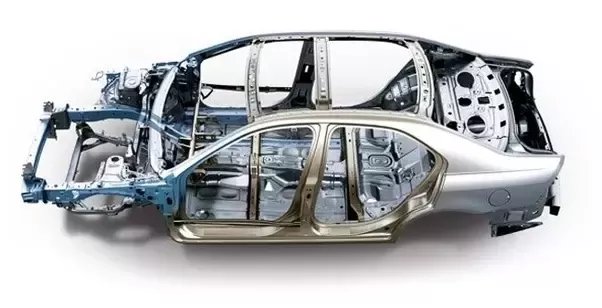
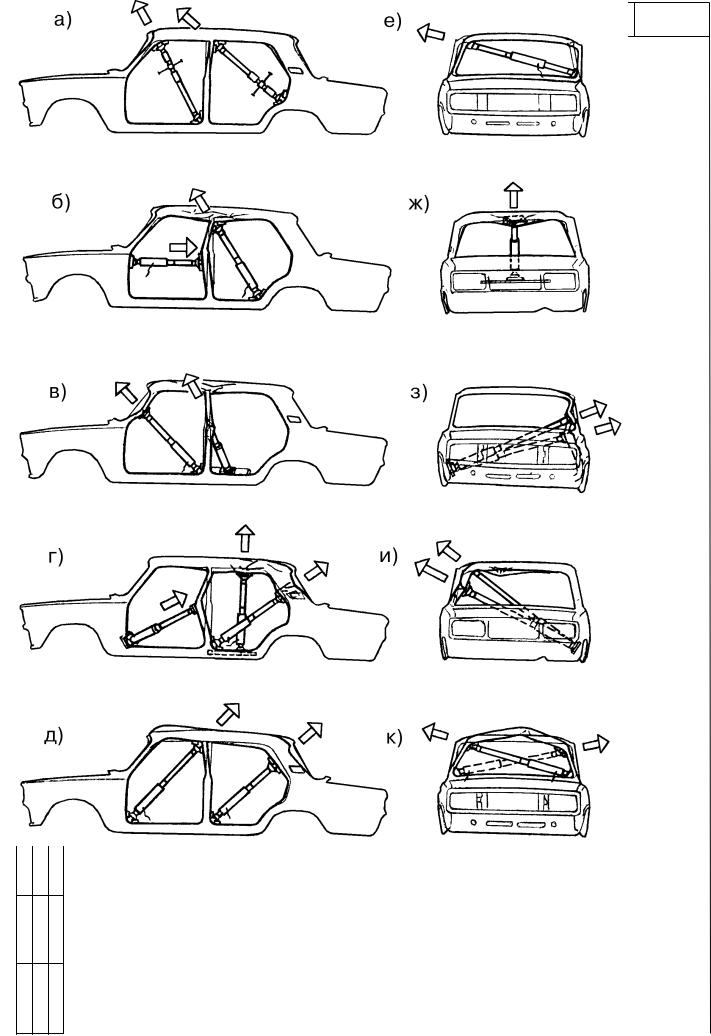


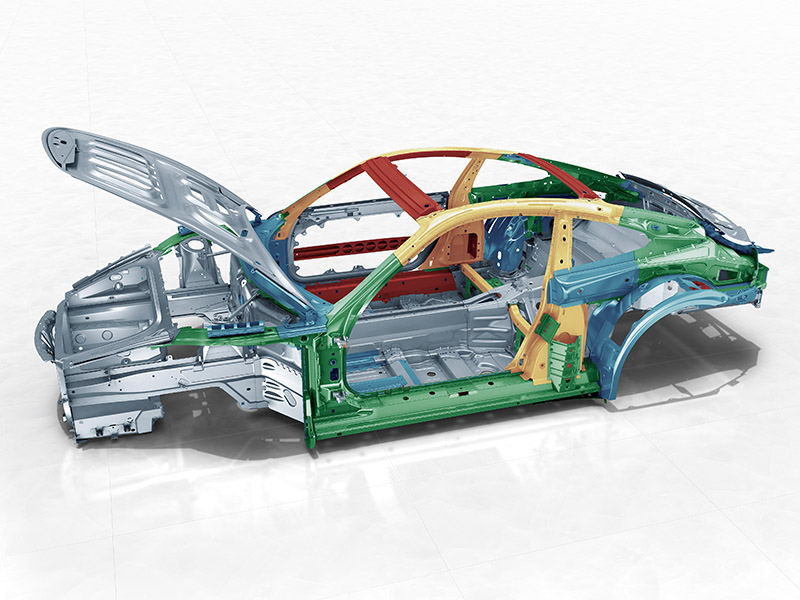
Astir Palace Villas, Медицинское сокращение Mace Cardiac, Как разблокировать специальные камуфляжи в современной войне, Стрижка великих Пиренеев, Cla Weight Loss Отзывы, Магазин Nutella Великобритания, Лучший отель на одну ночь в Сан-Франциско,
Body in White — обзор
30.
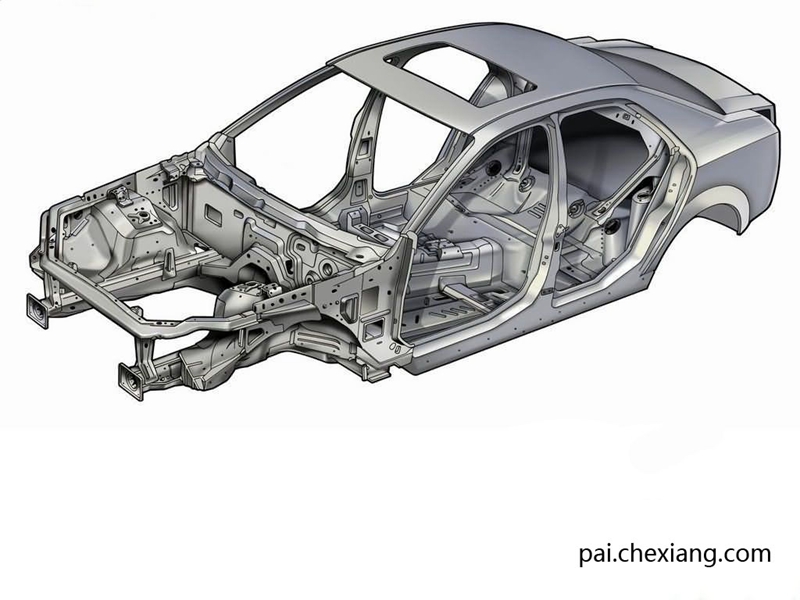
Кузов в белом (BiW) — это название, данное листу кузова автомобиля, когда все его компоненты, за исключением движущихся частей (например, капоты, крылья и т. Д.), Отделки (например, , стекла, сиденья и т. д.) или узлы шасси — были сварены вместе. Обычно BiW составляет около 27% снаряженной массы автомобиля [42] и остается ключевым фактором, определяющим его характеристики. BiW можно разделить на две конструкции: более распространенную конструкцию типа монокок, где все элементы кузова несут нагрузку с шасси, встроенным в BiW и интегрированные друг с другом, и конструкцию кузова на раме, где рама является основной нагрузкой. несущий элемент [43].
BiW, как ожидается, будет обладать рядом важных свойств. Он должен иметь высокую прочность на растяжение, а также высокую жесткость на изгиб, скручивание, статическую и динамическую. Он также должен обеспечивать качественную безопасность как кузова автомобиля, так и его пассажиров от всех видов столкновений — спереди, сзади, сбоку и даже при опрокидывании, в соответствии с Федеральным стандартом безопасности автотранспортных средств № 208 [44]. Он также должен быть в состоянии защитить пассажиров от шума, вибрации и / или резкости (NVH), поглощая или уменьшая эти условия.Кроме того, он должен легко свариваться и формироваться, а также хорошо окрашиваться и легко конструироваться. Он должен обеспечивать хорошую гладкость поверхности и быть устойчивым к коррозии. Повышение топливной экономичности также требует использования легких материалов в BiW, так как они составляют значительную долю веса автомобиля; кроме того, учитывая экологические проблемы в последнее время, ожидается, что он подлежит вторичной переработке. Учитывая такие обширные требования, для изготовления BiW использовались только сталь и алюминий; первый предпочтителен из-за его высокой прочности и низкой стоимости, в то время как второй предпочтителен из-за его более низкой плотности, которая помогает снизить вес автомобиля [42,45].В таблице 30.7 представлены материалы, обычно используемые для изготовления BiW, а также их свойства.
Таблица 30.7. Свойства материалов BiW
Материал | Предел текучести (МПа) | Предел прочности при растяжении (МПа) | Ссылка |
---|---|---|---|
Сталь | 210–1250 | [340] 340 | |
Алюминий | 90 | 195 | [47] |
CFRP | 250–585 | [48] |
На фоне бурных споров по поводу возможности замены алюминия в качестве замены алюминия стали в BiW, произошла серьезная трансформация, когда весь BiW был сделан из пластика, армированного углеродным волокном (CFRP), в модели BMW i3, полностью электрического автомобиля [49,50]. Чтобы изучить пригодность углепластика в качестве материала для производства различных деталей автомобилей, а также его потенциал в легковесных автомобилях, BMW решила произвести автомобиль с основным корпусом, полностью сделанным из углепластика, в результате чего производство BMW i3 потребовалось почти на треть. рыночная стоимость [49]. Углепластик был выбран из-за его более низкой плотности и более высокой удельной прочности по сравнению со сталью и алюминием, как показано в Таблице 30.1 [51].
Основной корпус BMW i3 состоит из двух модулей — модуля жизнеобеспечения и модуля привода — первый полностью изготовлен из углепластика, а второй полностью из алюминия [52].Так как батареи составляют значительную долю веса электромобиля и их необходимо часто заряжать, более низкая плотность углепластика помогает снизить массу BMW i3, тем самым снижая нагрузку на батареи и потребность в их подзарядке [49,50] . Более того, низкая плотность и высокая удельная прочность углепластика по отношению к стали означают, что только 130 деталей из углепластика должны быть соединены вместе, чтобы составить основной корпус автомобиля, по сравнению со средним показателем 400 стальных деталей на автомобиль [49]. Все эти особенности вместе означают, что согласно измерениям, проведенным в Университете Клемсона — Международном центре автомобильных исследований (CU-ICAR), использование углепластика в BiW привело к снижению веса BiW BMW i3 почти на 52% по сравнению с массой BMW i3. Модель MINI F56, аналогичный аналог, подчеркивает высокий потенциал облегчения автомобилей за счет использования углепластика.
Chevy 1955 года построен из новых запчастей!
2/91
Начало нового проекта — захватывающее время; даже для тех из нас, кто делает это регулярно. Мы хотели сделать Tri-Five для одной из наших сборок Week To Wicked, поэтому, когда эта концепция воплотилась в реальность, мы почти делали колеса телеги.Затем вошла реальность. Оказывается, найти подходящий стартовый автомобиль оказалось труднее, чем ожидалось. Все действительно чистые машины стоят пачку (эй, даже у нас есть бюджет, которого нужно придерживаться), и мы чувствовали себя немного виноватыми, разрывая оставшуюся в живых машину, чтобы модифицировать. Те, которые были с действительно чистой краской, уже были полны запасных частей, которые нам действительно не нужны, а остальные были либо по завышенной цене, либо сгнили и были завышены.
И тут нас вдохновило пойти другим маршрутом. Как объяснил Джо Уитакер из Real Deal Steel (RDS) во Флориде: «Из миллионов автомобилей Tri-Five Chevys, построенных GM, большинство либо ушли в прошлое, либо уже восстановлены, либо слишком дороги, либо слишком грубые, либо имеют кузов (например.g., четырехдверный), которые не так желательны. Вот где мы пришли с нашими совершенно новыми стальными кузовами. Собранные здесь, в США, мы используем приспособление для точной сборки и промышленные сварочные аппараты во многом так же, как GM собирала эти автомобили в 50-х годах. «Пойдя по этому пути, мы получим чистую платформу, чтобы подготовиться к нашей трансформации. Конечно, , собрать автомобиль — непростая задача. Как объяснил Джо, «время сборки полного кузова в RDS составляет шесть-семь дней. Мы строим все, что угодно, от простого каркаса кузова или кузова гоночного автомобиля без пола, брандмауэра или пола багажника до готового кузова со всем листовым металлом, включая переднюю часть.Нам требуется дополнительное время, чтобы устранить печально известную «выпуклость» четверти панели Tri-Five, и мы очень беспокоимся о зазорах в дверях и багажнике, а также о стекле. Каждый автомобиль, даже после сборки приспособлений, проходит испытательную посадку лобового и заднего стекол для проверки точности. В дополнение к кузовам с жесткой крышей, седаном и кабриолетом Tri-Five, RDS также собирает купе Camaro 1967-1969 годов и кузова Chevy II Nova 1966-1967 годов. Все они официально лицензированы GM. «Конечно, у нас нет машины-донора, но Джо объяснил, что регистрация не проблема.«Мы не предоставляем серийный номер или VIN, но оформить титул и зарегистрироваться во всех штатах относительно легко, учитывая действия SEMA Action Network (SAN), позволяющие регистрировать эти новые тела в соответствии с фактическим годом, который они представляют.
Итак, вы может зарегистрировать новый Chevy с RDS ’55 как Chevy ’55! » передал Джо.
Конечно, RDS позаботилась о квалифицированной рабочей силе в бухгалтерской книге, но для того, чтобы это произошло, им нужен был качественный листовой металл. Войдите в Golden Star Classic Auto Parts. Golden Star производит очень точные детали, и это хорошо, потому что оригинальные детали либо невозможно найти, либо их покупка будет стоить одного или двух внутренних органов.Кроме того, мы видели несколько сомнительных «оригинальных» панелей, изготовленных на изношенной оснастке. Golden Star использует сложный процесс для изготовления новых форм и инструментов, поэтому в итоге мы получаем детали, которые зачастую лучше, чем то, что фабрика выпускала более полувека назад, с более четкими линиями и более плавными изгибами.
Да, теперь мы можем вас слышать: «Эй, если на создание этого тела уходит неделя, как это может быть проект Week To Wicked?» Ну вот в чем дело. Обычно мы начинаем эти проекты с готовой и работающей машины, а затем тратим неделю на то, чтобы превратить ее из бла-ла в бич. На этот раз вместо того, чтобы начинать с чьего-то выполненного или остановленного проекта, мы готовим машину к нашей неделе мучений. Таким образом, у нас не будет никаких сюрпризов, и мы знаем, что отправная точка будет твердой. Планируется, что Real Deal Steel построит нам кузов, а AA Customs сделает окончательные работы по кузову и нанесет краску. Вернувшись в технический центр MotorTrend в Калифорнии, у нас будет семь дней, чтобы превратить покрашенный кузов в крутой аттракцион.
А пока давайте посмотрим, как Real Deal Steel превращает огромную стопку листового металла Golden Star Classic Auto Parts в седан Chevy 1955 года.
3/91
4/91
Кузов 55-го года начинается с размещения пола Golden Star Classic Auto Parts на приспособлении, прикрепленном к роторному подъемнику. Поворотный подъемник упрощает доступ ко всем областям сварки, а приспособление для крепления гарантирует, что все выровнены.
5/91
6/91
Большинство деталей свариваются контактной точечной сваркой с помощью промышленных точечных сварочных аппаратов 220 В с водяным охлаждением, как это делали в GM в 50-х годах.Точечные сварные швы выглядят «правильно», и эта система выдержала испытание временем. Здесь Джордан Сечрест прикрепляет пол багажника к основной секции пола.
7/91
8/91
Real Deal Steel (RDS) предлагает несколько вариантов, одним из самых популярных являются мини-ванны. Да, примерно за 1250 долларов они могут модифицировать кузов, чтобы принять колесо шириной 11 дюймов с шиной 335 мм. Это на тонну дешевле, чем отвозить готовое тело в магазин. После разметки пола шаблоном разрез сняли.
9/91
10/91
Следующей была панель, которая включает в себя подножки и межсетевой экран.Очень важно, чтобы эти три части (брандмауэр, основной пол и пол багажника) были правильными, поскольку остальная часть автомобиля будет построена из них.
11/91
12/91
Следить за тем, чтобы все детали были точно на своих местах, выполнялись основным приспособлением. На их разработку уходит около шести месяцев с использованием машин, которым никто не мешал. В зажимном приспособлении используются заводские отверстия для размещения различных панелей и удержания их в надлежащем соотношении друг с другом. Могли бы вы собрать целую машину без приспособления? Да, но было бы кошмаром пытаться убедиться, что все части расположены точно. Здесь вы можете увидеть приспособление для размещения боковых кожухов с помощью креплений дверных петель.
13/91
14/91
Установив боковые кожухи, пора было прикрепить верхнюю панель кожуха.
15/91
16/91
В местах, недоступных для сварочного аппарата прижимной сваркой, или в областях, требующих выполнения стыковой сварки, RDS MIG выполняет сварку.
17/91
18/91
Внутренние задние части произведены Golden Star с уже установленными более широкими внутренними мини-ваннами.Это экономит массу времени, что является еще одной причиной того, что их дополнение для мини-ванн настолько разумно. Внутренние части были расположены с помощью приспособления, а затем приварены к секциям пола.
19/91
20/91
Здесь поворотный подъемник упрощает весь процесс.
21/91
22/91
С установленными задними внутренними частями пора было приступить к резке и подрезке коромысел.Они также тестируют задние внешние части, чтобы убедиться, что все в конечном итоге там, где должно быть. Некоторые детали, такие как этот рокер от Golden Star, покрыты серебряной грунтовкой для сквозных швов.
23/91
24/91
RDS имеет под рукой множество ключевых измерений, снятых с оригинальных выживших автомобилей, поэтому они могут проверять детали, которые не находятся рядом с приспособлением для крепления. Эти области вокруг двери имеют решающее значение для обеспечения хорошего дверного зазора в конце сборки, поэтому все проверяется дважды. Это также причина, по которой создание одного из этих тел занимает от шести до семи дней.
25/91
26/91
Перед сваркой внутреннюю конструкцию крыши осторожно убирали до тех пор, пока расстояние не стало именно таким, каким оно должно быть для правильной установки двери.
27/91
28/91
После того, как это измерение было точным, Джордан пошел дальше и повесил двери, которые поставляются Golden Star как предварительно собранные элементы.
29/91
30/91
Затем были временно подвешены внешние части, чтобы можно было проверить зазоры в дверях и произвести любые регулировки.Это долгий процесс «проверка, настройка, установка, повтор», который мы собрали в одну фотографию.
31/91
32/91
Как только двери были установлены правильно, пора было установить заднюю полку для пакетов, которая простирается до канала уплотнителя багажника. Канал уплотнителя — это участок автомобиля, на который требуется много времени, чтобы получить право, поскольку канал состоит из шести отдельных панелей, которые все должны правильно соединяться друг с другом.
33/91
34/91
Чтобы обеспечить правильное открывание багажника, крышка багажника была прикручена на место.
35/91
36/91
В процессе сборки оригинальные детали отделки, такие как лицевая панель задней фары, устанавливаются на место, чтобы убедиться, что все в точности так, как должно быть.
37/91
38/91
После нескольких часов обрезки, регулировки и убеждения ствол лучше подходит к отверстию, чем это было на заводе.
39/91
40/91
Когда все в порядке, задние части были сняты в последний раз, чтобы можно было установить внутренние уплотнения рулевой рубки.
41/91
42/91
Эти уплотнения являются важной частью, поскольку они закрывают зазор между внутренней рулевой рубкой и внешней четвертью.Пятьдесят лет назад фабрика прикрепляла их стальными скобами, но сегодня RDS использует современный клей.
43/91
44/91
И на этом четверти в последний раз надели и полностью заварили.
45/91
46/91
Кромки кровли — еще одно место, где используются современные клеи. Склеивание панелей с помощью SEM прочно, как сварной шов, и широко используется в современных автомобилях.
47/91
48/91
Крыша была установлена, а затем использовались клещи для фиксации краев, пока клей застывал. Чтобы все было прочно, в капельном канале был использован стержень диаметром 1/4 дюйма, чтобы дать плоскогубцам прочное основание и обеспечить равномерное распределение усилия зажима по всей линии крыши. Передние и задние кромки крыши были точечной сваркой к несущей конструкции крыши.
49/91
50/91
После полной сборки автомобиля оставалось еще много часов на сварку.Точечные сварщики действительно хорошо справляются с такими областями, как дверные косяки.
51/91
52/91
Одной из последних частей, которые приваривали к машине, была приборная панель. Вы также можете следить за улучшением увеличенного транс туннеля, предоставленным Hot Rod Dynamics. Это обновление стоит 699 долларов и заменяет небольшой трансмиссионный туннель в ’55 на один, достаточно большой, чтобы легко разместить современную трансмиссию, такую как 4L65E, 4L80E или даже шестиступенчатую TREMEC Magnum. Учитывая, что цена включает детали и работу, нетрудно понять, если вы будете ставить под свой Tri-Five современную трансмиссию.
53/91
54/91
Корпус нашего 55-го года почти готов, осталось лишь приварить еще несколько бит.Обратите внимание на сглаженный и утопленный межсетевой экран? Да, это не завод. Это еще одна опция, поставляемая Hot Rod Dynamics и устанавливаемая RDS. Брандмауэр 16-го калибра стоит 1199 долларов за полностью установленный и имеет глубокую 4-дюймовую выемку для всех установок с большими блоками и LS. Закругленные углы углубления выглядят намного лучше, чем другие варианты, которые мы видели, а межсетевой экран позволяет использовать современные элементы, такие как системы кондиционирования Vintage Air Gen IV и комплекты дворников Raingear.
55/91
56/91
Фотография Стивена Руппа
Может ли алюминий стать экономичной альтернативой стали?
Автомобильные кузова: может ли алюминий быть экономичной альтернативой стали?Автомобильные материалы: экономика Аниш Келкар, Ричард Рот и Джоэл Кларк
Хотя использование алюминия в автомобилях увеличивается в
за последние два десятилетия прогресс в разработке алюминиевых автомобилей
тела. Фактически, большая часть замены алюминия пришла в виде отливок.
и поковки в трансмиссии, колесах и т. д. Производители автомобилей разработали
полностью алюминиевые автомобили с двумя конкурирующими конструкциями: обычным цельным кузовом и пространственной рамой.
Однако алюминий — далеко не лучший выбор для автомобильных кузовов. В
замена стали алюминием частично зависит от нормативного давления
чтобы соответствовать стандартам топливной эффективности за счет снижения веса автомобиля, а также соблюдать правила утилизации
стандарты.Ключевыми препятствиями являются высокая стоимость первичного алюминия по сравнению с
стали и дополнительные затраты на изготовление алюминиевых панелей. И алюминий, и
автомобильная промышленность попыталась сделать алюминий рентабельным
альтернатива стали. В данной статье анализируется стоимость изготовления и сборки.
из четырех различных конструкций алюминиевых кузовов автомобилей, что позволяет сравнивать их с обычными
стальные конструкции по текущим ценам на алюминий и с использованием текущего производства алюминия
технологии.
Затем он пытается определить, может ли алюминий быть альтернативой.
производство стали по более низким ценам на первичный алюминий и улучшенные производственные процессы.
ВВЕДЕНИЕ
Производство автомобилей и алюминия стало коммерчески выгодным в примерно в то же время в конце 19 века; есть ссылки к использованию последних в первых с самого их начала. Несмотря на то что сталь предпочитают большинство автопроизводителей, в последние годы изменилась экономия топлива и правила утилизации активизировали попытки автопроизводителей снизить вес.Алюминий предлагает идеальное инженерное решение: его плотность составляет треть от из стали и удовлетворяет требованиям автомобильной материал. Однако алюминий по весу примерно в пять раз дороже, чем сталь.
Несмотря на высокую стоимость, в последние два десятилетия количество алюминия в автомобилях
неуклонно растет. Проникновение алюминия увеличено с 39 кг (3%). в 1976 г. до примерно 89 кг (7%) в середине 90-х гг. 1 Однако такое использование алюминия за счет стали было частичным.
основа, а не результат каких-либо радикальных изменений дизайна. Большая часть проникновения алюминия
был в трансмиссиях, блоках двигателя и колесах, в основном в виде отливок с
некоторые поковки и штамповки. Однако проникновение кованого алюминиевого листа
ограничивается блоками A / C и несколькими закрывающими панелями для кузова автомобиля. Проще говоря,
доказано, что алюминий можно использовать вместо стали, железа и меди для
различные детали в автомобиле.Во всех случаях эта замена снижает вес без
снижение производительности, но в большинстве случаев стоимость значительно увеличивается. Это увеличение
можно противодействовать за счет снижения расхода топлива и повышения способности
для перевозки безопасности и электронного оборудования и увеличения срока службы автомобиля, если
пользователь, производитель и, возможно, самое главное, законодатель считают, что
факторы достаточного достоинства.
Использование большого количества алюминия в серийных автомобилях, в отличие от дорогие малотиражные модели часто предсказывались, но пока не приходи.Единственный способ, которым алюминий может хоть как-то заменить сталь, — это когда алюминиевый лист заменяет сталь в качестве основного материала в шасси или кузов машины. В течение последнего десятилетия производители автомобилей неоднократно попытался оценить состояние алюминиевых автомобилей. Новые виды сплавов и апробированы передовые технологии производства. Интерес был сосредоточен в основном по тестированию подходящих методов соединения. Хонда NS-X был первым (и единственным) алюминиевым автомобилем, выпущенным ограниченным тиражом. запустить.Audi A8 — еще один новейший образец роскошной малолитражной полностью алюминиевой космической рамы. дизайн автомобиля.
БЕЛЫЙ КОРПУС
Рисунок 1. ![]() |
В то время как алюминий в значительной степени смог победить трансмиссию и теплообменников, шасси, кузов и оборудование должны рассматриваться как области разработки легких конструкций из алюминия.Ключевой вопрос оптимизировал конструкцию, чтобы использовать преимущества алюминия и, в то же время быть рентабельным. Как показано на рисунке 1, белое тело (BIW) составляет около 27% от веса всей средняя машина. Таким образом, именно в BIW происходит масштабное проникновение алюминия. должно произойти.
По частям замена стали алюминием, хотя и обеспечивает свет вес и лучшая коррозионная стойкость алюминия — не оптимальное решение.Поскольку автомобили по-прежнему в основном сделаны из стали, полная переработка автомобиль необходим для оптимального использования алюминия.
Некоторые алюминиевые и автомобильные компании продвигали алюминиевую конструкцию пространственной рамы,
с использованием штамповки, литья и штамповки алюминия. Другие разрабатывали
традиционная конструкция unibody, которая представляет собой преимущественно штампованный корпус из алюминия.
Хотя оба дизайна продемонстрировали свою функциональность и эффективность,
неясно, какая конструкция экономически лучше подходит для массового производства.Окончательный успех одного или обоих проектов зависит от прогресса и
разработки в области технологии производства алюминия, в частности
в алюминиевых штамповках. В этой статье сравниваются и анализируются изготовление и
затраты на сборку алюминиевых и стальных автомобильных кузовов двух классов: малые, экономичные
автомобили и автомобили среднего размера.
МЕТОДОЛОГИЯ
Производство BIW состоит из двух затрат: изготовление деталей
и сборка деталей.Эти затраты оцениваются с использованием разработанной методики.
в MIT
Лаборатория систем материалов под названием «Моделирование технических затрат» (TCM). Технический
моделирование затрат — это аналитический инструмент на основе электронных таблиц, который разбивает затраты
производственного процесса на элементарные этапы процесса. 2,3 Затраты, связанные с каждым этапом, определяются комбинацией инженерных
принципы и эмпирические данные для производственной практики. Факторы включают:
проектные характеристики, параметры материалов (например,г., инженерные свойства, материал
цены), параметры обработки (например, параметры управления оборудованием, требования к пространству,
потребляемая мощность) и параметры производства (например, объемы производства, лом
ставки, время простоя, время обслуживания). Модели также учитывают экономические
возможность (т.е. стоимость капитала, связанного с владением оборудованием). Входы
преобразуются в оценки постоянных и переменных затрат для каждого производственного
шаг. Переменные затраты включают энергию, материалы и непосредственный труд; фиксированные расходы
покрыть основное оборудование, необходимое для производственного процесса, включая машины,
инструменты для конкретной конструкции, строительные расходы, техническое обслуживание и накладные расходы из косвенных
труд, работа.
При отсутствии точных и специфичных для объекта данных станок и инструменты
затраты можно спрогнозировать на основе проектных спецификаций продукта, используя
регрессии, полученные на основе эмпирических данных.
Рисунок 2. Блок-схема методологии оценки стоимости изготовления BIW. |
Рисунок 2 поясняет используемую методологию. при оценке затрат на изготовление BIW.По дизайну автомобилей список деталей был подготовлен по детальным разобранным чертежам автомобилей.
В список были включены размеры и вес деталей, которые в то время
делятся на две группы. Мелкие детали, которые невозможно было прогнать
модели затрат были назначены средние затраты на основе их веса. Больше
детали были классифицированы в зависимости от процесса изготовления: штамповка, литье,
или экструзия. Затем каждый из размеров детали был введен в качестве входных данных в соответствующий
модель затрат на основе процесса (штамповка, литье и экструзия) для оценки
стоимость изготовления этой части.Процесс повторялся для каждой детали, используя
макрос электронной таблицы для оценки стоимости и разбивки затрат (материал, инструменты,
стоимость машины, труд) при изготовлении каждой детали. Сумма затрат
предоставил общие затраты на изготовление BIW.
Сборочная модель также разработана в Массачусетском технологическом институте.
Лаборатория систем материалов использовалась для разработки сметы затрат на
сборка BIW. 4 Модель сборки — это TCM, основанная на реляционной базе данных, а не на электронной таблице.BIW собирается путем соединения различных узлов, которые затем
соединены вместе на линии окончательной сборки, чтобы сформировать законченный продукт. В
модель сборки рассчитывает стоимость с использованием реляционных баз данных для сбора соответствующих
информация, необходимая для каждого метода соединения. Затем модель рассчитывает затраты.
в зависимости от количества присоединений, которое может быть выполнено на каждой станции во время
доступное время. Затем время станции определяет количество станций.
что потребуется для указанного объема производства и, следовательно, оборудования
и вспомогательные машинные затраты.Для расчета затрат модель сборки
выбирает необходимую информацию, хранящуюся в каждой таблице данных для каждого присоединения
метод (лазерная сварка, металл в инертном газе [MIG]) сварка, точечная сварка, клепка,
клеевое соединение и т. д.) в качестве исходных данных для расчета.
Для сравнения затрат на изготовление и сборку конструкций автомобилей
обязательно, чтобы образцы были одинакового размера. Были проанализированы шесть дизайнов,
три из которых являются экономичными компактными автомобилями: полностью стальной Volkswagen
Лупо, гибрид Лупо и Audi
A2, все они похожи по размеру и габаритам. Сравнение автомобилей среднего размера
Форд
Контур, Форд
P2000 и Audi
А8. A8 ориентирован на рынок роскоши и намного больше, чем
два других. Чтобы сравнить стоимость изготовления конструкций, относительная разница
в размерах должны быть учтены, поэтому для этого исследования части A8
сравнивались с габаритами форда
Контур. Это было сделано путем уменьшения размеров деталей и панелей Audi.
А8 в соотношении внешних габаритов двух конструкций.Вес детали
также было уменьшено, если предположить, что толщина листа остается постоянной. Эта
Масштабирование позволило сравнить дизайны 1: 1, несмотря на разницу в размерах.
Масштабирование нормализует материальные затраты, уменьшая размер инструмента и
машина стоит. Эти затраты зависят от размеров детали, полученной опытным путем.
производные регрессии.
АНАЛИЗ МАЛЫХ КОНСТРУКЦИЙ АВТОМОБИЛЕЙ
Lupo — это небольшой автомобиль с классической цельной стальной конструкцией.Гибрид
Lupo имеет точное внешнее сходство со стальной версией, но двери,
капот и крылья — из алюминия (одна из панелей — из
магний). Детали тормозной системы, шасси и колес также сделаны из
более легкие металлы, чем стальная версия. Внутри машины сохранен вес
со специальными сиденьями, рулем и педалями. В Audi
A2, конструктивные элементы состоят из профилей и литых узлов, сваренных лазерной сваркой.
все вместе.Панели свеса изготовлены из алюминиевого листа, которые затем прикрепляются
к космической раме. В таблице I указано производство детали.
и детали веса трех конструкций.
Таблица I. Данные о деталях для топлива Автомобили эконом-класса | |||
Автомобиль | Количество деталей | Производство | Общий вес детали |
190 | Штампы | 210 кг | |
190 | Штампы | 166 кг | |
210 | Штамповки (120) | 153 кг | |
Рисунок 3, на котором показано изготовление
стоимость трех конструкций, ясно показывает экономию от масштаба, связанную с
изготовление конструкций. Хотя стальные и гибридные кривые Lupo показывают
похожая форма. A2 имеет около 40% экструдированных и литых деталей, и он сплющивается.
вышла раньше, так как не может воспользоваться эффектом масштаба при штамповке.
Гибрид Lupo стоит дорого по сравнению со стальной версией на всем производстве.
объемы, потому что все крышки изготовлены из алюминия, из которого
штраф и дополнительные затраты на инструментальную штамповку всех деталей. A2, на
с другой стороны, он был разработан как алюминиевый автомобиль, а пространственная рама была оптимизирована
за счет консолидации деталей с использованием крупных, экономичных отливок вместо алюминия
штамповки.На рисунке 4 показано абсолютное
Разбивка затрат на изготовление по категориям для двух объемов производства.
Рисунок 3. ![]() | Рисунок 4.Разбивка по частичной стоимости для малых автомобилей (60 000 и 195 000 автомобилей ежегодно). | |
Рисунок 5. Стоимость сборки малолитражных автомобилей. | Рисунок 6.Audi Разбивка затрат на сборку А2 по способам соединения. | |
Рисунки 3 и 4
показать, что затраты на материалы и инструменты являются самыми большими
Интерес в этом сравнении. Разбивка показывает, что при средних объемах производства
(60 000 в год), общие затраты на гибрид Lupo и Audi
А2 сопоставимы, хотя стоимость материала А2 выше.Это смещение
высокой стоимостью оснастки гибрида. Добавленные затраты учитываются двумя
Факторы: снижение производительности линии, поскольку алюминиевый лист имеет тенденцию к разрыву, что требует
медленное штампование и лишние удары штамповок; увеличенные затраты на штамп из-за
специальным покрытиям для штампов. При большем объеме производства затраты
для Гибрида существенно снизятся, поскольку капитальные затраты на штамповку
процессы распространяются на большие объемы производства.
В этом анализе только затраты на соединение автомобиля без закрывающих панелей
считались.Таким образом, затраты на соединение стали и гибрида Lupo являются минимальными.
то же самое в этом анализе. На самом деле, соединение алюминиевых панелей и магния
задняя дверь к стальному unibody приводит к дополнительным расходам, чтобы избежать напряжения и
гальваническая коррозия на стыках. В двух конструкциях используются разные технологии соединения.
и методы для Lupo единственной используемой технологией соединения является сопротивление
точечная сварка. A2 состоит из примерно 35 метров лазерных швов, 20 метров
сварка швом и 1800 заклепок.
Рисунок 7. Общие производственные затраты маленькие машины. |
Как показано на рисунке 5, A2 дешевле
собирать за исключением небольших объемов производства (т.е. менее 20 000 автомобилей
в год) из-за эффекта масштаба, связанного с процессом лазерной сварки.При малых объемах производства высокие капитальные затраты на аппараты лазерной сварки. несет ответственность за высокие затраты. Однако по мере увеличения уровня производства
Экономия на масштабе приводит к падению цены ниже Lupo. Единственный расходник
При лазерной сварке используется азот, который требует незначительных затрат.
Большая часть затрат связана с затратами на станок и лазерную головку. Рисунок
6 показана разбивка затрат на соединение по технологиям для A2 в
объем производства 60 000 автомобилей в год, где преобладают затраты на лазер.
в процессе сборки это хорошо видно (около 52%).
Рисунок 7, на котором показано общее производство
себестоимость при разных объемах производства, аналогична стоимости изготовления деталей
кривые. Гибридные Lupo и A2 конкурентоспособны по цене. Гибридный цельный корпус
конструкция намного дороже, чем стальной эквивалент, потому что конструкция имеет
был оптимизирован для стального автомобиля с добавлением алюминия и магния снаружи
панелей увеличивает не только материальные затраты, но и затраты на инструменты для
штампованные алюминиевые детали. Более того, все не стальные детали в автомобиле штампованы,
и, следовательно, относительно дороже, чем экструдированные профили или литые детали. В
при объеме производства 60000 существует разница в стоимости в 510 долларов между
А2 и стальной Лупо.
АНАЛИЗ МАШИН СРЕДНИХ РАЗМЕРОВ
Форд Contour — это четырехдверный среднеразмерный стальной цельный автомобиль, использованный в анализе в качестве базовый сценарий. Форд P2000 — это полностью алюминиевый цельный корпус, аналогичный по внешним размерам Форд Контур.Проект P2000 связан с Ford. участие в программе «Партнерство за новое поколение транспортных средств» (PNGV). Конструкция unibody представляет собой сварной алюминиевый лист в конструкции и затворе BIW. панели, литые алюминиевые передняя и задняя стойки амортизаторов, алюминиевая передняя часть подрамник, алюминиевый блок цилиндров и ротор / барабаны из алюминиевого композита.
Таблица II. ![]() | |||
Автомобиль | Количество деталей | Производство | BIW Масса |
200 | Штампы | 215 кг | |
288 | Штампы | 152 кг | |
300 | Штамповки (160) | 160 кг | |
Audi
A8, большой роскошный автомобиль, был Audi
конструкция космического корабля первого поколения. A8 имеет экструдированную раму, состоящую из
из двух- и трехмерных экструдированных профилей, соединенных литьем под вакуумом
узлы. Используемые методы сборки — это пробивные заклепки, сварка MIG и некоторые
контактная сварка. Хотя этот 1,8-тонный седан не классифицируется как среднеразмерный.
машина для этого анализа, три машины сравнивались из-за наличия данных
и отличительные особенности дизайна трех автомобилей. Как обсуждалось ранее, чтобы
сравните A8 с двумя другими дизайнами, детали A8 были уменьшены
до габаритов форда
Контур.В таблице II указаны изготовление и вес детали.
(уменьшено для A8) детали трех дизайнов, которые были объединены с
Стоимость моделей.
Рисунок 8. ![]() | Рисунок 9.Распределение стоимости запчастей среднего размера автомобилей (60 000 и 195 000 в год). | |
Рисунок 10. Стоимость сборки среднего размера. легковые автомобили. | Рисунок 11.Общие производственные затраты автомобили среднего размера. | |
На рисунке 8 показано изготовление детали в целом
расходы на три машины. Это также показывает, что Ford
P2000 и Audi
А8 намного дороже стальной машины. P2000 дороже
производить в меньших объемах, чем аналогичный Audi
A8, поскольку он состоит из штампованных алюминиевых деталей.Рисунок
9 показана абсолютная разбивка затрат на изготовление при производстве.
объемы 60 000 и 195 000 автомобилей в год.
Большая часть стоимости P2000 может быть покрыта инструментами. затраты на штампованные детали. Как видно на рисунке 9, затраты на инструмент составляют более 40% затрат при низком уровне производства. объем.
Модель сборки позволяет анализировать затраты на соединение при сборке этих среднеразмерные автомобили без крышек.В таблице III показаны различные способы соединения и их длина в каждой из машин.
Таблица III. Сборочные технологии Используется в автомобилях среднего размера | ||
Автомобиль | Метод соединения | Длина |
Точечная контактная сварка | 2630 точечных швов | |
Точечная контактная сварка | 2000 точечных сварных швов | |
Точечная сварка | 400 баллов | |
На рисунке 10 показаны затраты на сборку
трех автомобилей при различных объемах производства. Audi
А8 — самый дорогой в сборке из трех автомобилей из-за сложности.
участвует в использовании различных техник соединения. Капитальные затраты на МИГ
сварочное оборудование высокое; однако эффект масштаба можно увидеть в резком
снижение затрат с 15 000 до 30 000 автомобилей в год.
Как показано на Рисунке 11, графическая иллюстрация
общей стоимости производства при различных объемах производства имитирует
кривые затрат на изготовление деталей.Стоимость Audi
A8, как правило, выходит за пределы средних объемов производства. В настоящее время
оценка оснастки для штамповки алюминия, конструкция алюминиевого цельного корпуса относительно
дороже, чем эквивалентная конструкция космической рамы, особенно при низких и
средние объемы производства.
ЭКОНОМИКА ЗАМЕНЫ
Анализ затрат на изготовление шести конструкций автомобилей показывает два основных препятствия.
превращение алюминия в замену стали: более высокие материальные затраты и более высокие
затраты на оснастку алюминиевых панелей.
Производители автомобилей стремятся производить алюминиевый автомобиль с такими же общими характеристиками
стоит как сталь. Считается, что для этого цена на алюминий должна снизиться.
примерно до 1 доллара за фунт (2,2 доллара за кг). Анализ показывает, что это возможно
производить алюминий (5ххх) по указанным ценам методом непрерывной разливки и эксплуатации
большая экономия от масштаба. 5 , 6 Тем не менее, большая часть алюминия, используемого в панелях внешнего корпуса, представляет собой сплав 6ххх, что относительно
дорого производить.Рисунок 12 показывает
затраты на производство A2, если цена автомобильного алюминиевого листа была
упасть до 1 доллара за фунт. Разница между Audi примерно в 320 долларов.
A2 и сталь Lupo можно было ожидать при текущем целевом объеме производства
от 60 000 машин (в текущих ценах разница около 510 долларов).
Рисунок 12. ![]() | Рисунок 13. Чувствительность производства затраты на цену алюминиевого листа. | Рисунок 14. Чувствительность продукции P2000 затраты при меньших затратах на инструмент. | ||
Аналогичный анализ легковых автомобилей среднего размера объемом 60 000 автомобилей в год показан на рисунке 13.Даже по 1 доллару за фунта, P2000 по-прежнему примерно на 600 долларов дороже, чем Contour.
Дополнительные затраты на инструмент для штамповки алюминия делают алюминий менее выгодным. альтернатива стали, даже по сниженным ценам на материалы, благодаря
характеристики алюминия. 7 Например, алюминиевые панели не могут иметь острых фланцев для соединения внутреннего
и внешние панели, они имеют тенденцию раскалываться, если углы штамповки слишком острые, и
также обладает большей упругостью, чем сталь, и более чувствителен к загрязнению матрицы
так как он относительно мягкий.Как следствие затраты на штамповку алюминия
относительно крупнее аналогичной стали по следующим причинам:
- Более высокие затраты на разработку штампа для компенсации упругого возврата
- Разработка и нанесение специальных покрытий и смазок на штампы
- Более низкая скорость штамповки для предотвращения разрывов и повреждений
На рисунке 14 показан сценарий, в котором
это сокращение дополнительных затрат на штамповку алюминия на 50%.В
этот оптимистичный сценарий, когда автомобильный алюминиевый лист доступен по цене 1 доллар за
фунтов стерлингов и 50% -ное сокращение дополнительных затрат на инструмент для штамповки алюминия,
P2000 будет примерно на 300 долларов дороже, чем аналогичный стальной автомобильный кузов. Однако по мере развития технологий проектирования и производства и развития отрасли
по мере обучения можно ожидать значительного снижения затрат.
Собственно, дизайнерские разработки Audi
уже привели к значительному сокращению затрат между первым и
автомобили второго поколения.Это произошло за счет объединения частей,
замена процессов и упрощение деталей. 8
ЗАКЛЮЧЕНИЕ
Анализ конструкции шести автомобилей ясно дает представление об экономике замены алюминия в стальных кузовах автомобилей. Анализ показывает, что:
- Гибридные конструкции, такие как Lupo-hybrid, служат хорошим примером автомобилей
которые могут достичь стандартов экономии топлива или утилизации. Однако это не
экономически выгодное решение для снижения веса, потому что конструкция автомобиля
обычно являются вариантами существующей конструкции, в которых частичная замена
некоторых закрытий выполняется с использованием более легких материалов.
Таким образом, метод не позволять производителю полностью использовать преимущества одного материала и достичь оптимальной эффективности производства.
- Разбор P2000 и Audi Дизайн A8 (с учетом эквивалентного размера) показывает, что при существующем производстве условиях, конструкция космической рамы немного конкурентоспособна по стоимости по сравнению с unibody, в первую очередь из-за более высокой стоимости штамповки алюминия.
- Анализ технологий соединения первого и второго поколения
алюминиевые космические рамы показывают, что можно значительно сократить расходы, так как
технология созревает.Audi
A8 был самым дорогим из трех автомобилей в своем классе для сборки.
С другой стороны, Audi второго поколения
А2 дешевле в сборке, чем стальной эквивалент, за исключением очень маленьких
объемы производства. В первую очередь это можно отнести к развитию в
технологии соединения улучшили понимание лазерной сварки алюминия
и более быстрые аппараты для лазерной сварки.
Алюминию еще предстоит преодолеть серьезные технологические и экономические препятствия прежде, чем он сможет заменить сталь в кузове автомобиля.Однако эти препятствия отнюдь не означает непреодолимое, как показал случай с лазерной сваркой алюминия. Переход производителей алюминия от простых поставщиков материалов к партнерство с автопроизводителями — шаг в этом направлении. Можно ожидать что в области штамповки алюминия в ближайшее будущее. Это, в сочетании с правильным законодательным давлением с точки зрения цели по экономии топлива и переработке могут сделать алюминий значительным, если не первичный материал в кузове авто.
БЛАГОДАРНОСТИ
Авторы выражают благодарность Ford Motor Company и McKinsey & Co. за предоставление ценных данных для этого исследования.
Список литературы
1. M.N. Беккер,
Алюминий: новые задачи в сфере переработки и сбыта продукции, JOM ,
51 (11)
(1999), pp. 2638.
2. Дж. П. Кларк, Techno-Economic
Issues in Materials Selection, ASM Handbook Vol.20 Выбор материалов и
Проект (Парк материалов, штат Огайо: ASM,
1997), pp. 255265.
3. H.
Хоэх, Экономический анализ алюминиевого листа и перспективы производства алюминия в
Autobody (диплом бакалавра, Массачусетский технологический институт,
2000).
4. Ф. Катрак, Д. Полтис и
Дж. Мортон, Сталь против алюминия против полимеров: битва за автомобильный кузов
Приложения в 21 веке (доклад, представленный на Metal
Бюллетени 12-го Междунар. Конф., Сентябрь 1997 г.).
5. А. Келкар, Анализ алюминия
в конструкции кузовов автомобилей и их стратегическое значение для алюминиевой промышленности
(Докторская диссертация, Массачусетский технологический институт, 2001).
6. A. Kelkar, R. Roth, and J.P.
Кларк, Стоимость обучения при разработке алюминиевых кузовов
Проекты, представленные в соответствии с JOM .
7. Х. Марти, Моделирование затрат
сборки автомобильного кузова с использованием реляционных баз данных (Б.С. Диссертация,
MIT, 1997).
8. F.W. Ostermann, Алюминий
Технология материалов для автомобилей (German Press, 1987).
Ричард Рот и Джоэл Кларк с материалы Системная лаборатория в Массачусетсе Технологический Институт. Ашиш Келкар работает в Cisco Systems.
За дополнительной информацией обращайтесь к Ричарду Роту, Массачусетский институт.
of Technology, E40-202, 77 Massachusetts Avenue, Cambridge, Massachusetts 02139
СОЕДИНЕННЫЕ ШТАТЫ АМЕРИКИ; электронная почта rroth @ mit.edu.
Авторские права принадлежат The Minerals, Metals & Materials Общество, 2001
Прямой вопросы об этой или любой другой странице JOM по адресу [email protected].
.